Traction motors for e-mobility:
fully automatic potting of a busbar on the stator
Carolin Gachstetterr & Markus Rieger
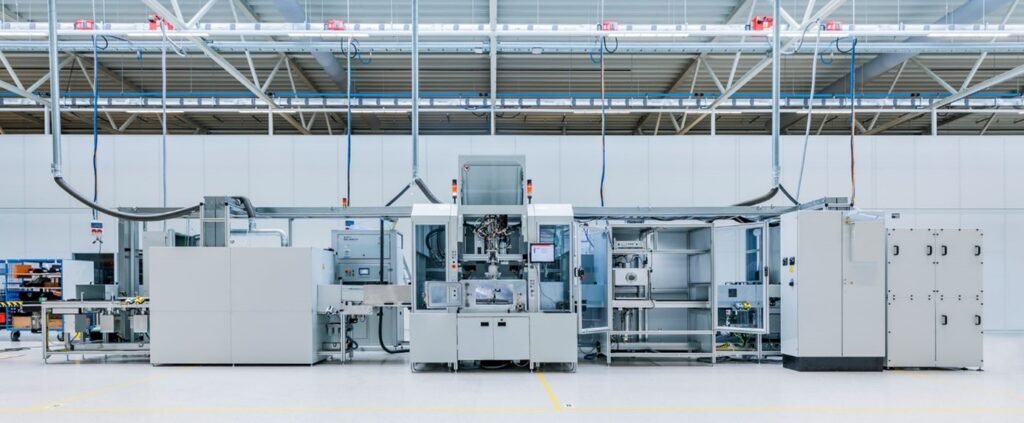
In the production of traction motors for electric and hybrid vehicles, there are a large number of different dispensing applications. The busbar potting (3 PH shift ring) is one of them.
Two main types of AC motors are used in modern electric cars: Asynchronous (ASM) and synchronous motors with permanent magnet (PSM). In both cases, there are busbars at the ends of the windings of the stator, which establish switching connections between the individual windings. To insulate the busbars from the cooling medium of the electric motor, the latter is encapsulated. The encapsulation must be carried out with high precision in order to avoid, for example, performance losses due to a reduced cooling effect.
Dispensing applications in the production of electric motors:
- The connection ring of a stator has various busbars that have to be insulated. For this purpose, the circuit ring is encapsulated with a newly developed reaction casting resin.
- The interconnection is mechanically fixed to the stator with a hot rivet joint in an upstream process.
- The copper windings of the stator are impregnated to increase heat dissipation, improve performance and prevent short circuits.
For a major German Tier1 supplier, bdtronic developed a complete fully automated production line for casting the shift ring on a stator (48-volt to 800-volt possible). The production line combines different technologies and thus achieves the shortest possible cycle and process time and meets the demanding customer requirements for a small footprint and efficient use of resources.
In addition to the heart of the production line, the vacuum dispensing unit, it consists of a preheating station by means of an infrared unit, a cleaning station, a low-pressure plasma unit for surface activation, a curing station with a second infrared unit, as well as the underlying conveyor belt and the loading and unloading station by a robot.
Components of the fully automatic production line:
- Preheating station with infrared technology
- Cleaning station
- Low pressure plasma system under vacuum
- Standard vacuum dispensing cell B5200-V with dynamic mixing head and 3-chamber vacuum technology
- Curing station with infrared technology
- Automated transport system with RFID and MES data connection
- Loading and unloading station with 6-axis robot
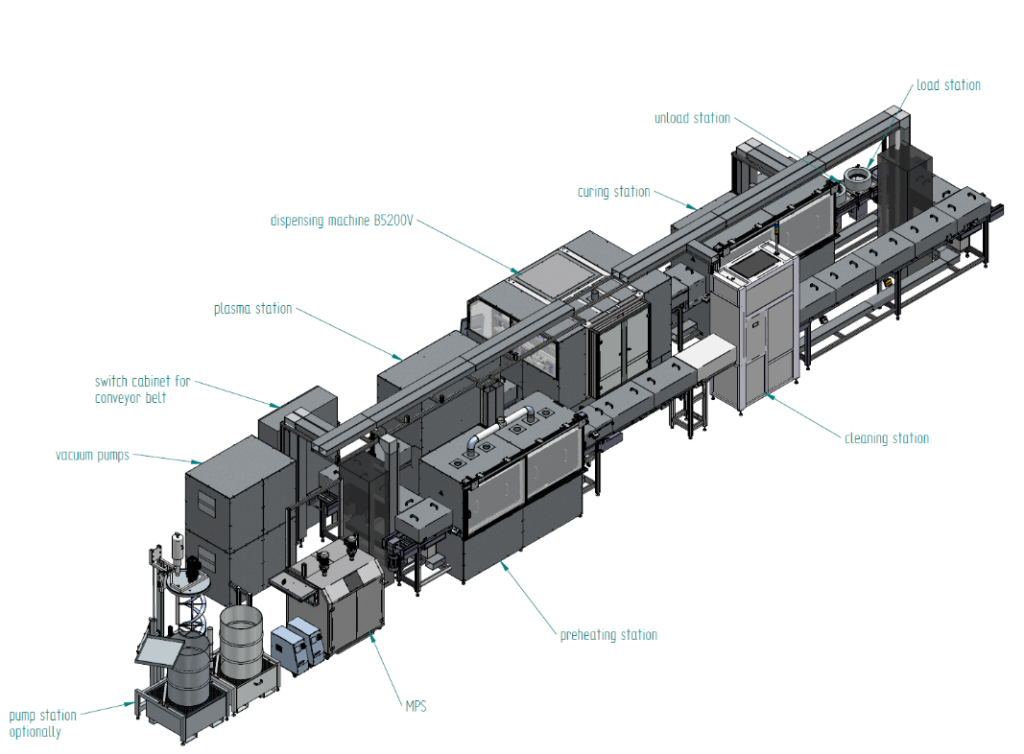
Standard vacuum dispensing cell with material preparation
The standard vacuum dispensing cell processes a highly filled 2-component epoxy resin. These are used as electro casting resins wherever protection against outside influences and high temperature resistance are required. Therefore, they are particularly suitable for electric motor applications. These special electro-potting resins are usually 2-component systems that must be precisely mixed and metered in the specified mixing ratio while maintaining the exact process temperature, because they react very sensitively to fluctuations in the mixture. The dynamic mixing system guarantees the highest mixing quality at all times, even with large viscosity differences, difficult mixing ratios and short processing times (so-called pot life) of less than three minutes.
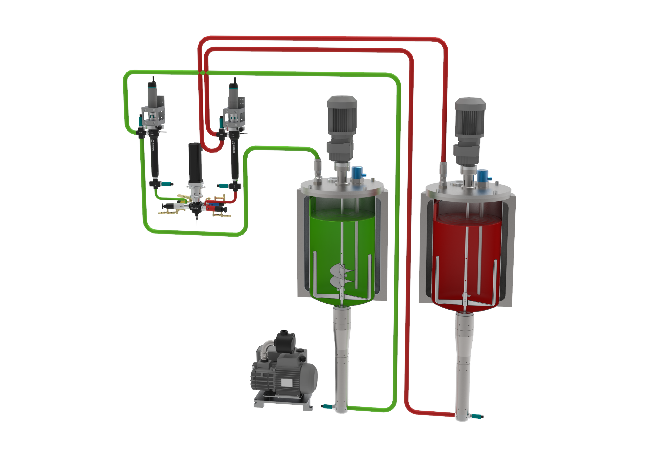
With the MPS material preparation system, the resin is permanently recirculated in the line system, tempered and prepared bubble-free under vacuum (here below 10 mBar absolute). The material preparation system can also be refilled during operation in order not to lose machine availability due to unnecessary downtimes during refilling (24/7 production possible).
The material is dispensed continuously and volumetrically by the pump technology with eccentric screws developed in-house by bdtronic and proven over many years. An elaborated temperature management system with different temperature zones in the material feed and the mixing head as well as potting in a vacuum chamber with 25 mBar ensure an optimal dispensing result on the component. Extensive trials in the recently expanded and technically upgraded Technology Centre have determined flexible dispensing rates between 1 and 3 g/s in advance, which will be realized in the series production system. Three-dimensional contours are also possible thanks to the high-precision axis system (servo control) in the vacuum chamber.
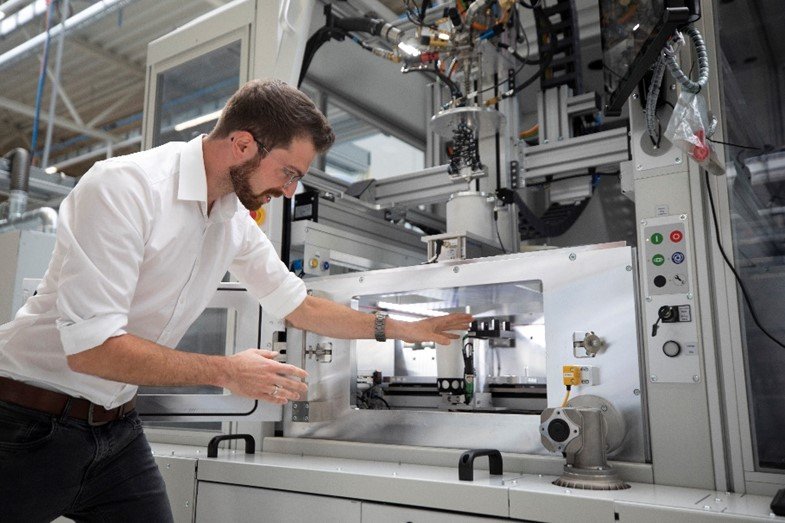
Process linkage offers advantages
In addition to the precise and repeatable dispensing task, the shortest possible cycle and process time is a key requirement in the automotive industry. This can be achieved on the one hand by the machine itself – among other things, a fully automatic 3-chamber vacuum system is used – and on the other hand by intelligently linking the process steps.
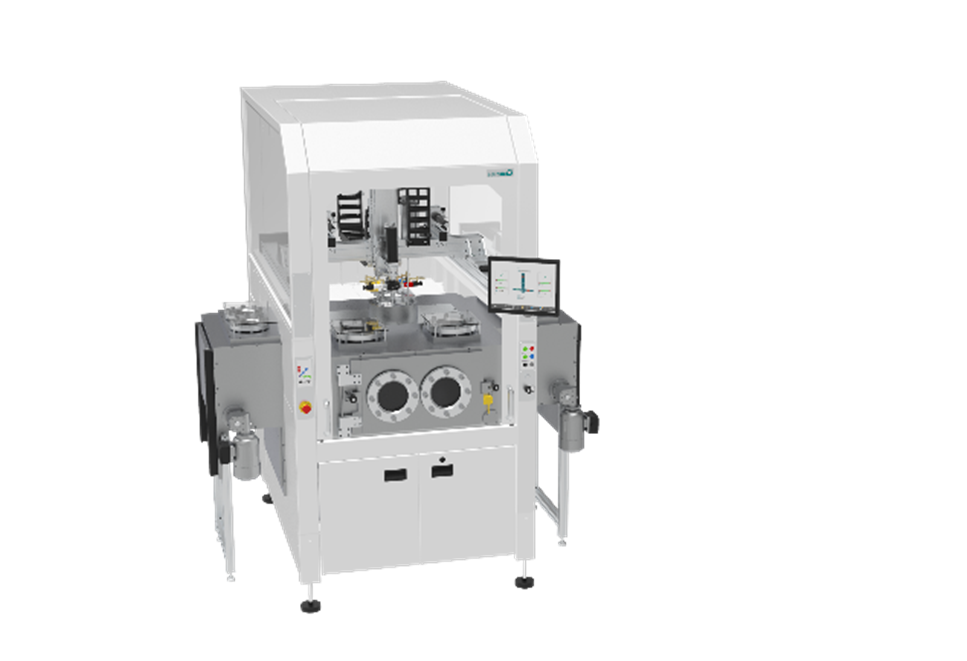
The vacuum plasma unit for surface activation of the components was integrated in such a way that the temperature loss of the preheated components is as low as possible. Here, too, technology developed in-house by bdtronic is used. Following the potting of the stator rings, the epoxy resin is annealed in an infrared unit to make the components handling-resistant for further processing.
The infrared technology offers several advantages: on the one hand, four different preheating positions can be used, on the other hand, the process time is minimized and the unit requires only a relatively small footprint. Furthermore, the energy demand is significantly reduced compared to conventional convection ovens. The production unit offers full MES tracking and thus meets the high quality requirements of the automotive industry.
Summary:
Smart linking of various process steps ensures the shortest possible cycle and process time. Perfect dispensing results with consistently high quality are guaranteed by highly developed technology from the dispensing specialist. The complete process parameters can be developed and sampled in the technology centre with original components for the series machine and can be transferred to series production.
Markus Rieger, Sales Manager, and Carolin Gachstetter, Marketing Manager at Bdtronic