Project SUSMAGPRO
Sustainable Recovery, Reprocessing and Reuse of Rare-Earth Magnets in a European Circular Economy
As electrification continues to rise, demand for Rare Earth Elements (REEs)—a group of 17 metals—grows across the world. In Europe, the demand for magnets, such as neodymium-iron-boron (NdFeB) used in motors, far exceeds supply. Estimates suggest that 90 percent of the EU’s demand cannot be met by locally sourced REEs. This shortage is because mining is feasible only if the ore has a sufficiently high content of rare earth metals, which Europe lacks. Consequently, Europe is heavily dependent on imports to bridge this 90 percent shortfall. China, producing between 70 and 80 percent of REEs for the global market, effectively controls the market, leading to rising demand and price volatility. This has prompted a European consortium to seek solutions.
SUSMAGPRO: A European Initiative
Alongside research looking to avoid the use of such materials in magnets one EU-funded project has taken the lead in developing processes to recycle and develop a stable secondary material from the reprocessed REEs. First created in 2019, SUSMAGPRO (Sustainable Recovery, Reprocessing and Reuse of Rare-Earth Magnets in a European Circular Economy), saw nineteen European organisations across seven countries, join forces to address the challenges of recycling and reprocessing for magnet reuse. The project not only looked at the process but also challenged engineers to think about designing for recycling from inception. SUSMAGPRO’s ambition from the outset was to revolutionise how magnets are recycled and also demonstrate the effective reuse of said recycled rare earth materials in several industries. Earlier this year, the project reached a key milestone in this journey in the field of automotive.
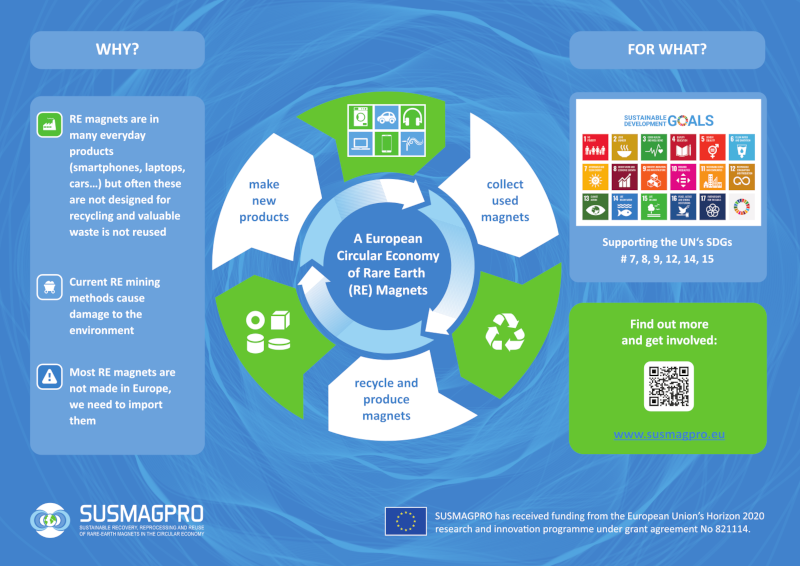
According to SUSMAGPRO, it has been estimated that approximately 2,000-3,000 tonnes per year of NdFeB are now available for recycling and this is expected to rise once today’s wind turbines and first wave of EVs reach the end of their life. For reference, the electric driveline of a passenger car contains up to five kilogrammes of metals such as neodymium, praseodymium and dysprosium, while a wind turbine generator has between 300 and 550 kilogrammes per MW.
Currently, end-of-life (EOL) magnets are recovered through shredding, chemical recycling, and pyrometallurgical routes. These methods are expensive, energy-intensive and not environmentally friendly, resulting in many valuable products ending up in landfills.
Getting round to a Circular Economy
SUSMAGPRO set about finding ways to produce a stable secondary source for REE by developing and demonstrating innovative pilot plants at Technology Readiness Levels (TRLs) 6–7. The goal is to enable clean and sustainable recycling of these most critical REEs from sources in the EU to be used in circular-economy recycling routes for three of the largest market segments for permanent magnets: automotive systems, water pumps and audio loudspeakers. The target set is that the developed short-loop reprocessing routes will enable the EU to gain a better foothold in the worldwide renewable energy systems (RES) device markets.
Design for recycling
ZF, a global leader in driveline and chassis technology as well as active and passive safety technology, has been an integral part of the SUSMAGPRO magnet recycling project. Alongside the automotive sector, where it is perhaps best known, ZF also serves market segments such as construction and agricultural machinery, wind power, marine propulsion, rail drives and test systems. It was therefore no surprise that such a project would interest its engineers both in Germany and at its UK R&D Hub in Solihull, UK. ZF’s involvement in the project saw it heavily involved both in how the recycled materials would perform but also how to design the thousands of motors it produces so that they can be more easily recycled. For the latter, ZF collaborated with Pforzheim University in Germany to consider how magnets can be easily extracted and recycled when the motor is no longer in use. “Optimising designs to make best use of critical rare earth materials, using magnet-free designs where appropriate, and ensuring rare earth metals where used aren’t lost at the end of a product’s life all contribute to a truly sustainable future,” notes Dr David Moule, electric drives technical specialist from the ZF Servo Drives Centre of Competence. “We want to reduce the amount of waste going to landfill, conserve resources by reducing the need for virgin materials and support the circular economy by keeping materials in use for as long as possible.”
University Challenge
Alongside the design element, ZF collaborated with the University of Birmingham, on the extraction and recycling of rare earth magnets from end of life motors. Its role was to look at the HPMS (Hydrogen-Processing of Magnet Scrap) route. This pioneering process enables the breakdown of end-of-life magnets into a Rare Earth (RE) rich alloy powder. Once separated from other elements and purified, the resulting RE alloy powders are ready to be reprocessed into new magnetic components without the need for chemical extraction or pyrometallurgy. “Rare earth magnets are difficult to separate from components as they are glued, coated and break up to a magnetised powder on shredding which then sticks to the ferrous scrap,” says Professor Allan Walton, professor of critical and magnetic materials. “Our Hydrogen Processing of Magnet Scrap (HPMS) technology offers an extremely efficient method to separate rare earth magnets, producing a demagnetised, purified alloy powder which can be fed into multiple parts of the value chain. Without such an efficient separation process it is difficult to see how recycling can be achieved at scale.” The HPMS process is licensed to Hypromag Ltd who scaling this technology in the UK, Germany and the USA.
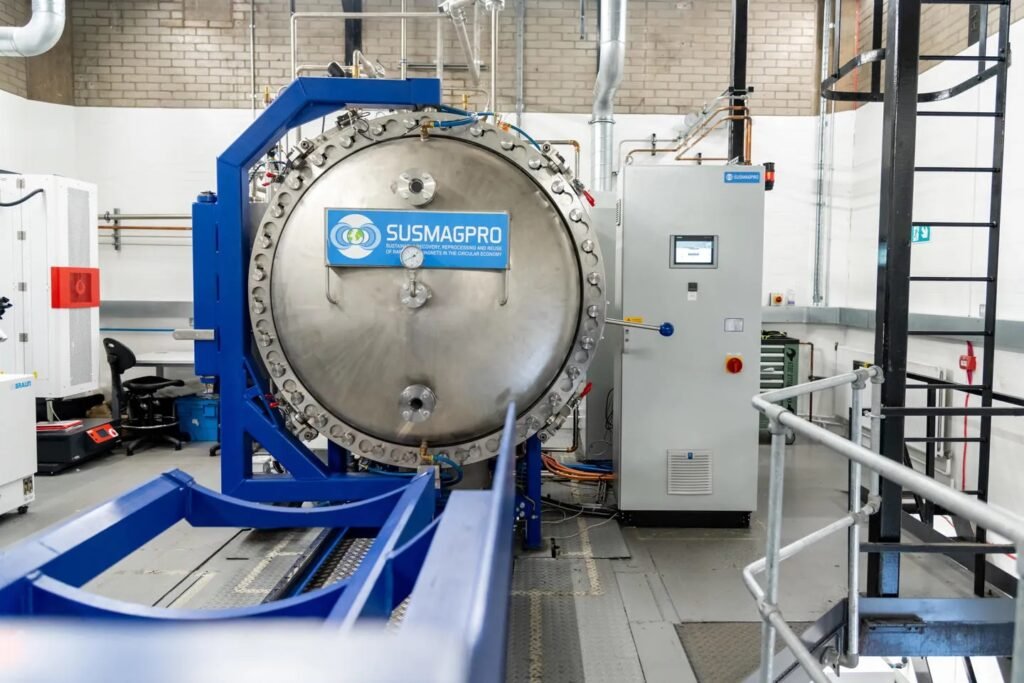
Increasing attraction
ZF played a crucial role in benchmarking the recycled products produced by the University of Birmingham against primary materials in terms of magnetic properties and corrosion resistance, focusing on automotive applications. Other sectors involved in benchmarking included water pumps with Grundfos (Denmark), loudspeakers with B&C Speakers (Italy) and headphones with Sennheiser Electronic (Germany).
Breakthrough
Earlier this year, SUSMAGPRO partners achieved a significant breakthrough. Magnets produced from secondary material via the patented HPMS process, by project partner University of Birmingham were evaluated in rotors produced by ZF. The results were promising, with the recycled magnets showing a remarkably similar performance compared to magnets based on virgin material. “We are delighted by the promising results and look forward to using everything we have learnt in our future projects,” concludes Moule.
The recycled magnets produced using the HPMS process required only 12 per cent of the energy compared to primary production.
According to SUSMAGPRO, the global recycling rate for rare earth metals is currently less than one percent. The goal is to reach 25 percent in Europe by 2027. The success of SUSMAGPRO’s trials brings this goal within closer reach.
Avoiding Rare Earth Elements
In addition to recycling projects, ZF is exploring solutions to avoid using REEs. Last year, ZF introduced I2SM, an enhanced, production-ready variant of a separately excited synchronous motor (SESM). Unlike other magnet-free concepts, ZF’s I2SM transmits energy for the magnetic field via an inductive exciter within the rotor shaft, reducing energy transmission losses by 15 per cent. This magnet-free motor offers extreme power and torque density while being compact and environmentally friendly. ZF claims that I2SM can reduce the production CO2 footprint by up to 50 per cent compared to classic electric motors with rare earth magnets.
Mark Philips Editor