Impact of sensor technologies on the e-vehicle powertrain performance
The resolution and accuracy of the rotor position sensor has an influence on the performance of an electric drive.
All over the world, new electric motors are currently being developed for the future drive-train of electric vehicles. The electric motor and its components will undergo various levels of maturity similar to combustion engines in recent decades. The goal of all developers is increasing the efficiency of the drive system with respect to the greatest possible range of one battery charge.
An important component in this context is the motor sensor system.
The measurement of the current of the 3 phases Iu, Iv Iw and the angular position θ of the rotor are of crucial importance.
The following diagram shows the mathematics behind a field-oriented control of a synchronous machine.
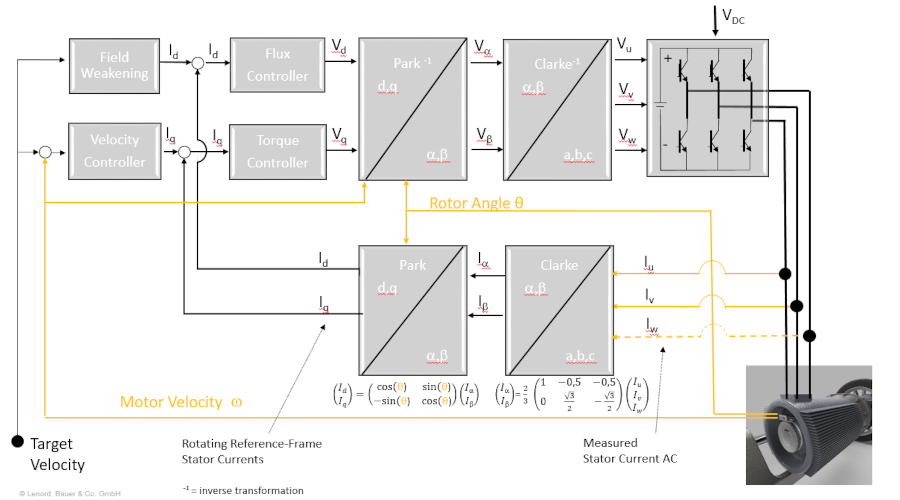
This article points out the impact of the parameters resolution and accuracy of rotor position and rotor speed on the performance of a drive.
Lenord + Bauer and Altair have added a configurable rotor position sensor to the already existing and validated simulation of a typical IPM machine of a mid-range vehicle.
The image below shows the components of the simulation. The element Position Sensor is new.
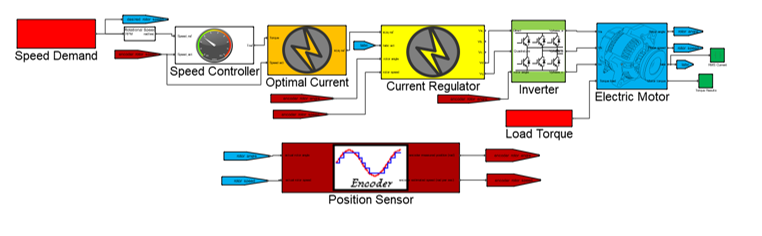
Influence of the resolution on performance
Especially when a vehicle has to accelerate under a high-torque condition avoiding sliding wheels and vibration and thus material-friendly, the resolution of the speed-sensor is of decisive importance.
The following graph clearly shows that, for example, a sensor resolution of 8 bit and a typical inverter switching frequency of 10kHz leads to a resolution of the speed of 2344 RPM. During run-up at very low speed the speed controller does not measure the real gradient of speed and therefore the torque controller overdrives. This inevitably leads to vibrations in the drive and ultimately to noises when starting up. That’s what we know from trams or other railways where this does not play a major role due to the few starting phases and the very stable mechanical design of the engines. In electric vehicles with many stop and go phases vibrations and noises are undesirable.
A typical situation in a passenger vehicle is, for example, driving over a curb or a fully occupied bus, which has to start on an ascending road.
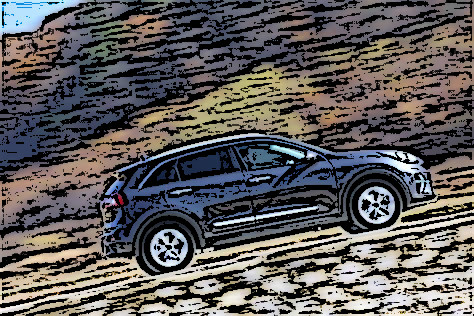
Evaluations of the torque curve show, as expected, a low-resolution leads to higher torque fluctuations in the starting phase.
Diagram Below
Blue line: 8-bit resolution high torque ripple causes high vibrations and loud noises
Nm

red line: 10-bit resolution lower torque ripple causes lower vibrations and less noises
Diagram Below
Comparison of the power consumption shows in the start-up area that a higher resolution (red line) contributes to a gain in efficiency )
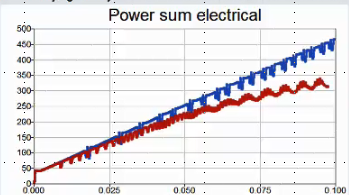
time (s)
Influence of the accuracy on performance
The second important parameter is the accuracy of the system.
For this we simulated various load scenarios for an electric vehicle.
One of the best-known scenarios is certainly the acceleration of a car from 0 to 100 km/h.
This scenario was simulated 3 times. The individual simulations only differed in the accuracy of the rotor position sensor used.
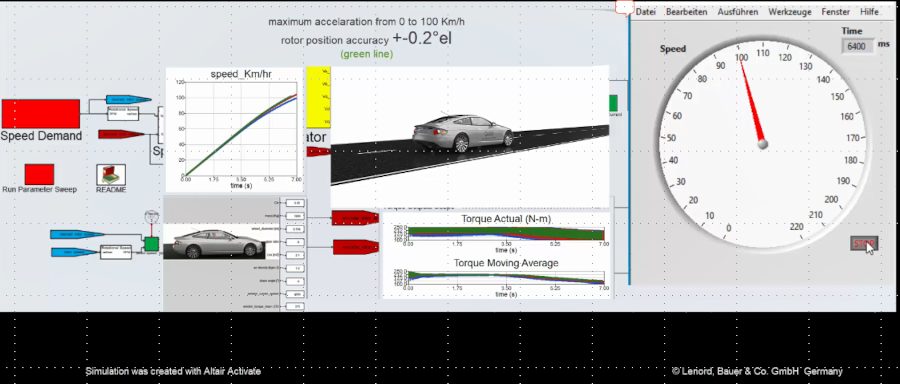
The results in the following table show that the accuracy of the rotor position sensors is crucial for the performance of the powertrain. With the same engine power, same controller and inverter it is possible to accelerate faster while consuming the same or less power.a
Rotor position accuracy | Time 100km/h 0 – 62,4 m/h | Torque ripples |
+- 2° el. | 7,04 s | High |
+-1° el. | 6,64 s | Middle to high |
+-0,2° el. | 6,44 s | Low to middle |
Summary and Conclusion
We have proved in various simulations of electric drive trains, that the resolution and accuracy of the rotor position sensor has an influence on the performance of an electric drive.
Therefore, developers of new drive systems should consider not only possible variations of the rotor and stator design or faster inverter switching times, but also the sensor technology in their test stands as part of the statistical design of experiments. Crucial parameters of the rotor position sensor are resolution and accuracy.
“Our sensors have been playing an important role in electric drives for more than 30 years. We are passionately driving the development of electro mobility in order to increase comfort of driving and contributing to an eco-friendly environment.” concluded Dr. Matthias Lenord, Founder, Lenord, Bauer & Co. GmbH
Dipl.-Ing Ulrich Marl In 2009 he became the head of production at Lenord + Bauer, followed by the position of general manager of production for 8 years. In 2018 he decided to face a new business challenge and changed the position into sales department to conquer the worldwide market for upcoming electrical vehicles. Based on fundamental technical experience and excellent knowledge of production and quality management method he is an excellent point of contact for many engineers in the automotive R&D departments around the world.