Overcoming the safety and lifetime cost challenges that come with EVs requires reliable, innovative and serviceable materials from a dedicated partner. The effective use of thermal interface materials (TIMs), adhesives and sealants is fundamental.
Dr. Pradyumna Goli, Business Development Manager Battery Systems North America & Holger Schuh, Global Technology LeadThermal, Henkel Adhesive Technologies
Electric vehicles (EVs) are a major driver for innovation within the automotive sector, but their commercial success will depend on whether they can achieve true mass market appeal. The key factors governing whether mainstream consumers will opt for an EV over an internal combustion engine (ICE) vehicle relate to safety, efficiency, and affordability, as well as the presence of innovative features such as autonomous driving. All the while, OEMs must ensure that EV parts remain compliant with the evolving safety standards.
The key components powering EVs are the power storage, power conversion and e-drive systems. Choosing and optimizing materials for these units that deliver on affordability, reliability and regulatory compliance, in terms of design and assembly, is therefore essential. As the industry and the regulations governing EVs continue to evolve, formulating materials that meet these objectives is becoming challenging, but with the right dedicated partner, not impossible.

Protection against thermal propagation
The safety requirements for a compliant EV are completely different from those required from a conventional ICE vehicle. Since batteries are the key component in an EV, lithium-ion (Li-Ion) technology is the primary technology used when designing battery packs. Current Li-Ion technology delivers many advantages over other systems, including higher energy density and charge retaining capacity, as well as longer operating life. However, one of the major limitations for this technology is operating temperature. When Li-Ion cells are exposed to elevated temperatures of over 80˚C, they become explosive in nature due to the limitations of electrolyte chemistry. This phenomenon is called “thermal runaway” and poses a major limitation on the optimal design for EV battery packs.
Manufacturers must comply with varying regulations in different countries around the world, in order to ensure that their battery pack designs to be approved for local use. In China, for example, EV systems must be designed in such a way that passengers will have a minimal 5 minute window for escape1. In order to meet these requirements, thermal management is critical and the effective use of thermal interface materials (TIMs) is fundamental.
The role of TIMs in thermal management
TIMs are fundamental to thermal management, since they optimize heat transfer from components such as batteries in power storage systems, insulated-gate bipolar transistor (IGBT) modules, MOSFETS, and transformers in power conversion systems, to heat sinks. Power density is what defines the amount of heat that these components dissipate, and in particular for power electronics these numbers can be quite substantial (image 1). For example, IGBT’s typically used in power conversion systems have power densities that can range anywhere from 10KW/module to 350KW/module, implying they require very high performance TIMs.
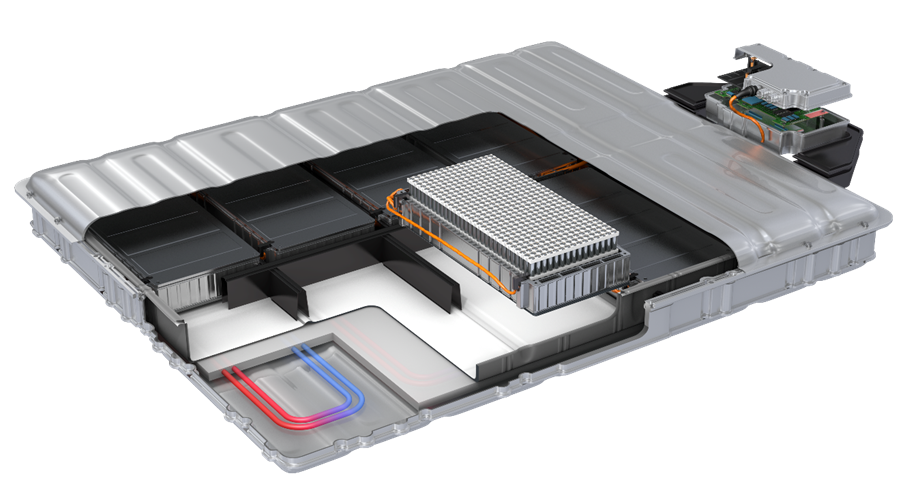
As the name suggests, high performance TIMs require high thermal conductivity. This is an increasingly important issue, as these power electronics devices are being miniaturized and at the same time becoming more powerful than ever before. Higher thermal conductivity will lead to higher TIM density and thus slower dispense performance, since more filler is required. This is where materials innovation such as Henkel’s new BERGQUIST GAP FILLER TGF 7000 can be used to address a real market need for high thermal transfer without compromising on dispense rates. This material offers the best in its class thermal performance (7 W/mK), as well allows for achieving a maximum possible tested dispense rate of up to 18g/second. Henkel also offers gap pads of up to 12W/mK to address thermal management issues for devices that demand high thermal performance.

For the power storage systems , the requirements are completely different. A typical 4-in-1 IGBT module has a surface area of 14 in2, whereas a typical battery pack has a footprint of 5000 in2). Furthermore, batteries have low power densities (6 watts/cell-600 watts/cell), as well as a limited operating temperature. As a result, the thermal management requirements for battery systems are driven by factors such as conformability, lightweighting, fast flow rates for high throughput and cost. Henkel APS series products are engineered specifically for power storage applications to give flow rates up to 80cc/second. Furthermore, the solutions succeed in terms of thermally conductivity and density, while still offering a silicon-free advantage.
The overall implication is that no single TIM can solve every thermal management issue, and that materials supplier should have a broad portfolio to give maximum flexibility to their customers.
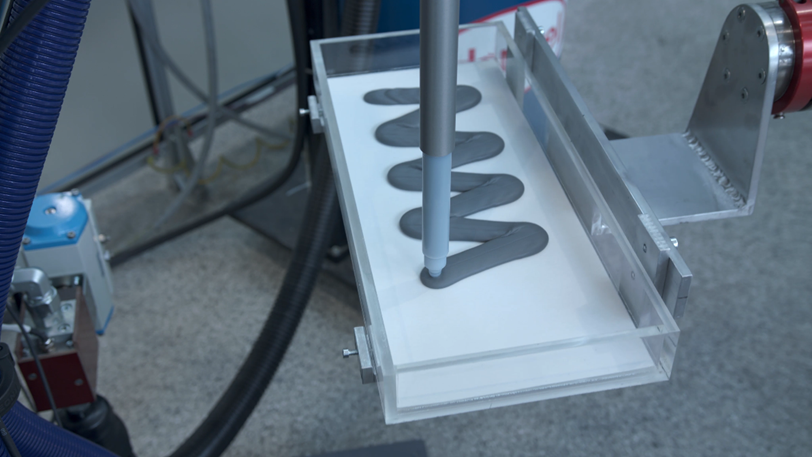
Further critical factors to EV safety
While the thermal conductivity coefficient for heat transfer efficiency still remains the primary requirement, there are other factors that should be considered critical for optimizing EV safety. Treatment of the battery pack surface is required to protect it against corrosion, which can amongst others damage the battery pack gasket. As a result, external influences such as dust and moisture could interfere with the components inside the pack, leading to reliability and failure risks.
Furthermore, adhesives provide structural integrity for ensuring strength during the robust operation of the battery pack. EV batteries go through the harshest of environmental and operational conditions, e.g. temperature and humidity could vary from anywhere between -40˚C to 49˚C and 0 to 85%. All of these aspects will place a vast amount of stress on the structural strength, meaning that any adhesive designed for this application will have to perform flawlessly under these extreme conditions.
As the TIMs should be compatible with the chosen adhesive & sealant solutions, significant complexity comes into play in terms of design. Given these hurdles, it’s essential that OEMs work together with their materials suppliers from the very beginning of the design phase, in order to achieve the best possible result. Success demands the reliance on a supplier with a broad available technology portfolio in order to ensure maximum flexibility. Henkel is the ideal partner for component design, with dedicated customer support in place, as well as the broadest TIM, adhesive and sealant portfolio available on the market.
Total lifetime cost reduction
Battery efficiency and economics is what will differentiate one EV automotive manufacturer over another, as the technology moves further mainstream. Battery costs have come down from US$1000/KWH in 2010 to just US$156/KWH today. The projections are that these costs will drop even further to US$73/KWH by 20302.
One key factor influencing the total lifetime cost of EV battery packs concerns assembly speed. In general, to optimize throughput, material solutions should have high flow rates, allow for fast curing and be compatible with large-scale manufacturing. In particular battery cell architecture can create a bottleneck in the assembly process: around 4,000 cylindrical cells are required to make a typical 80KW battery pack. Since some OEMs are already producing over 0.5 million cars a year in North America alone, simple math dictates that over 2 trillion cells will have to be manufactured and assembled to meet this demand. In order to allow for the superfast assembly of EV battery cells, Henkel collaborated with Covestro on the development of a total system solution. Hereby cells can be fixated in a UV-translucent carrier within 5 seconds, through the use of a Loctite AA 3963 cure-on-demand adhesive .
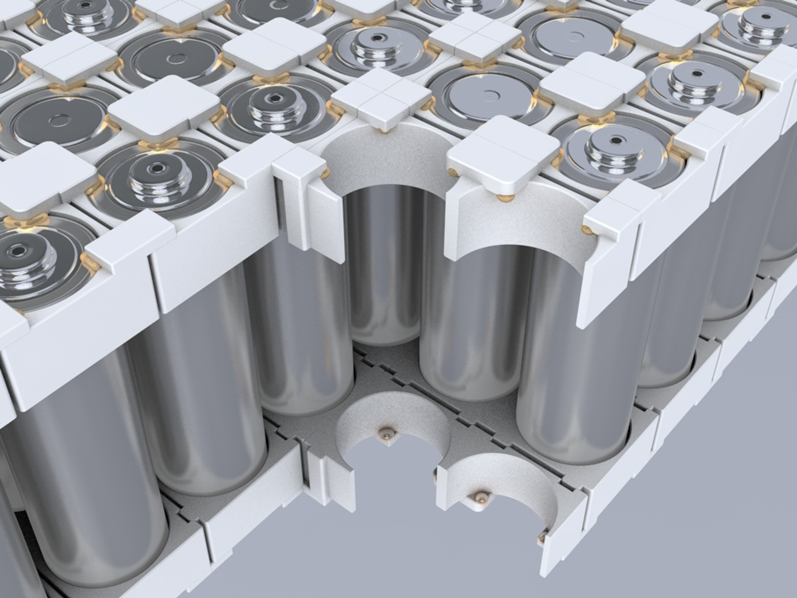
The total cost of an EV will also depend on how easily serviceable the design of the battery system is, which is influenced by whether the gasket used to seal the battery is reopenable or not. Since the battery is the most expensive part of the EV, having the ability to rework it easily without having to take the battery out of the car body can reduce these costs significantly, which is where advanced gasketing technologies come into play . Sustainability is another key consideration to bear in mind. Ultimately all materials that have been scraped off after the battery has been repaired or serviced will need to be disposed of with minimal environmental impact. This is again where an innovative materials supplier has a role to play.
It’s clear that TIMs, adhesives and sealants are of substantial importance for the assembly and operation battery packs. All materials should be manufacture friendly, economical, compatible and compliant when used together in line with relevant local regulations. Henkel’s broad portfolio as such is helping to drive change so that EVs can go even further into the mainstream.
Sources