Bonding, sealing and potting as key technologies for battery production
Carolin Gachstetter, Andreas Olkus, Markus Rieger, Frank Vercruysse, Wim Dexters
Adhesive bonding is a proven joining technology in the automotive industry. The added value of bonded joints is immense because they not only perform the function of joining, but also protect against external influences and ensure safety. Properties that are in particular demand for battery production.
Bonding and potting battery cells
Battery cells come in a variety of formats. Currently the most used battery cell formats are the cylindrical, the prismatic and the thin pouch format. What they all have in common is that they must be connected by electrically insulating adhesives. Two component polyurethane thermal conductive adhesives with high thermal conductivity are often used.
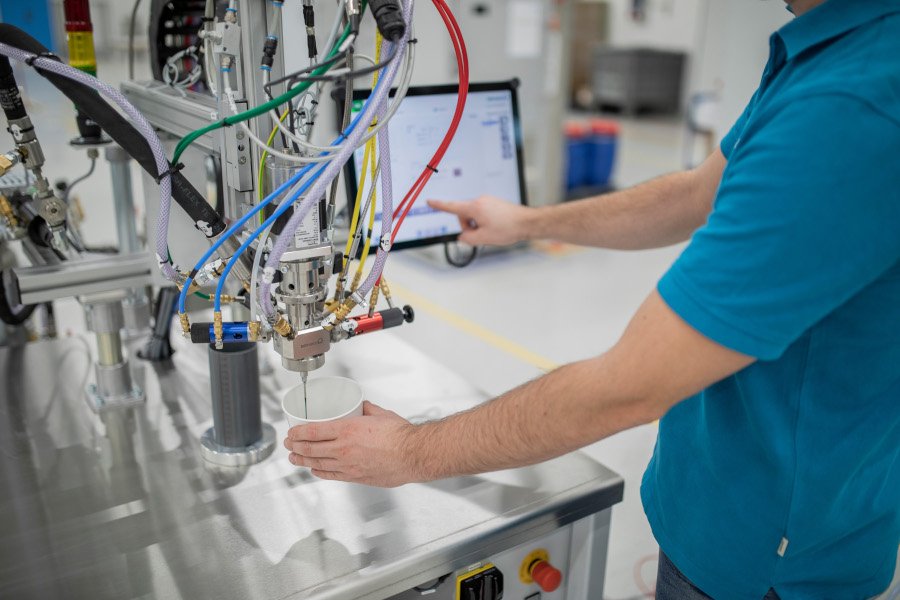
The greatest challenge with these materials is a high viscosity A component and a very low viscosity B component, as well as mixing ratios of up to 100:5. Accurate and consistent mixing is essential for the material to be able to reach its optimal properties. In addition, the A component is usually processed from 55gln (200l) drums due to high material consumption. Optimizing material extraction from the drum and the lowest possible loss of material when changing are essential here.
Cylindrical cells, also called round cells, are often encapsulated due to their geometry. On the one hand, this serves to fix the cells in place; on the other hand, self-levelling adhesives offer excellent heat dissipation, shock absorption and increased crash stability. In addition, air pockets between the individual cells can reliably be excluded. The potting resin is filled directly into the product by a dispensing head (1C, 2C static, 2C dynamic). Subsequently, curing takes place via time, temperature, UV or humidity. Since battery cells cannot be potted under vacuum, it is important to have a dispensing process that is optimally developed for the component and the potting material used. Ideally, this is determined in advance in lab trials at the Technology Center before it is applied to the series production machine.

The advantage of lab trails is that information on component optimization and practical experience can be provided during the product development phase. Within the scope of process development, sample parts can also be manufactured, which can be subjected to comprehensive testing processes by the customer.
Speed-dependent metering for demanding component geometries
The individual battery cells are tightly arranged to form a so-called module. Frames are often used to attach and stabilize the cylindrical battery cells. The process that needs to be solved is how to connect the individual battery cells to the frame. The complex component geometry entails a dispensing line with numerous corners and changes of direction. The challenge for the dispensing system is to apply the same amount of adhesive at every point, even if the dispensing speed varies. This can be solved by the bdtronic in-house developed speed-dependent dispensing called speedUP, which intelligently links and controls the speed of the axis movements and the dispensing rate.
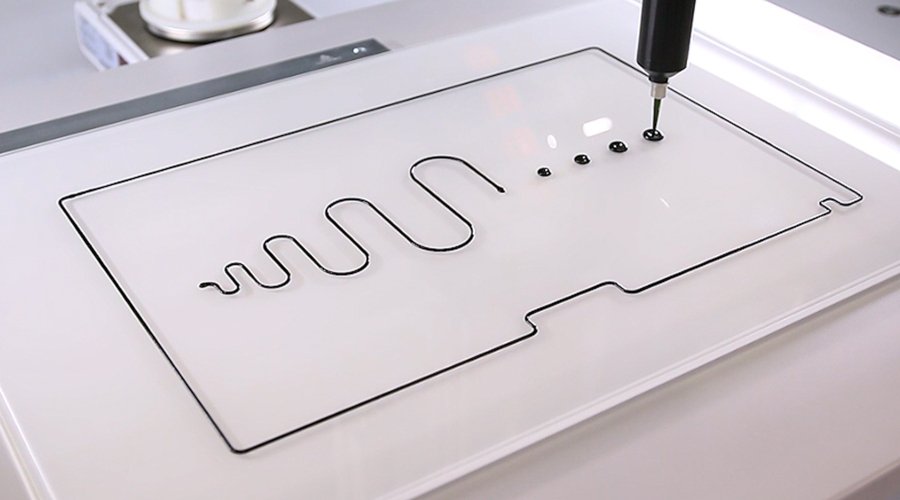
Long straight sections are dispensed at high speed and critical curves at low speed. The result is a significant reduction in overall cycle time. This technology is also used for bonding and sealing of housings or casings with polyurethane, epoxy or silicone materials with fast curing times.
Effective heat dissipation with gap filler application or injection
The battery modules generate energy in the form of heat during operation. This is dissipated by applying thermally conductive materials between the battery module and the aluminium heat sink to prevent overheating. Thermally conductive liquid gap fillers are designed for automatic dispensing in high-volume production. They offer excellent thermal and mechanical properties and place virtually no stress on components during assembly. Because these materials are liquid, they can be freely dispensed in almost any desired pattern or shape, allowing extreme flexibility in manufacturing and design. To achieve the thermally conductivity needed in these applications, these pastes contain a large amount of abrasive thermally conductive fillers. This requires low-wear metering systems, via which a permanently precise metering application can take place. The material must be conveyed with as little pressure as possible, so that separation of the thermally conductive paste is prevented. Compared to other pump systems, eccentric screw pumps offer several advantages due to their robust and low-wear technology: due to the continuous and volumetric pumping, pressure fluctuations are avoided so as not to stress the material. This prevents sedimentation and separation, a common problem especially with silicone-based heat transfer materials.
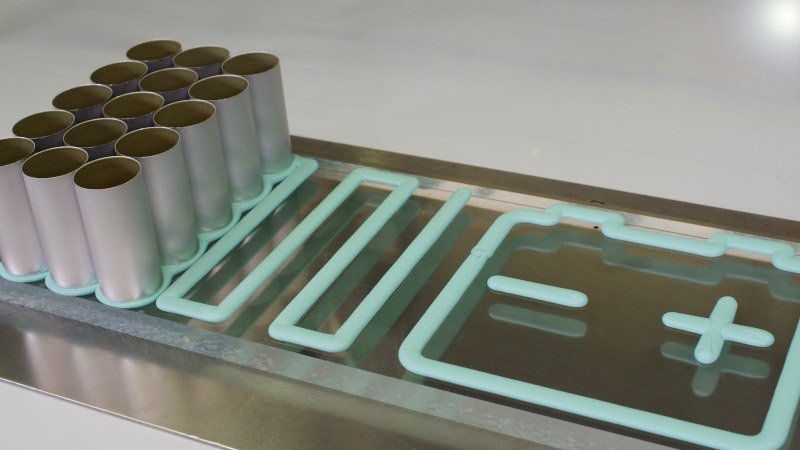
Another factor that should not be underestimated when defining the process parameters is inertia: if you set materials with a high density in motion and stop them again, thread formation often occurs. Here, the perfect interaction of precise servo-controlled metering pumps, robotics and the metering contour is crucial. In this case, too, a speed-dependent metering system can help minimize process times while maintaining consistently high quality. Special attention should also be paid to the material preparation system. On the one hand, air pockets must be reliably prevented during pail or drum changeover. On the other hand, material extraction from the pail or drum must be maximal. Thermally conductive materials are applied in large quantities and acquisition and waste removal costs are high. A close look at the total cost of ownership (TCO) shows that investing in reliable material preparation leads to high savings in running costs in a short time.
Thermally conductive materials are usually applied in a contour and then pressed between the joining partners, but they can also be processed using an injection process. A process was developed by bdtronic in which the highly abrasive gap filler is injected at low pressure into the housing of a battery module so as not to damage the sensitive pouch cells. The gap between the battery and the housing base is filled completely and without air bubbles.
Housing bonding and sealing
The battery housings are typically installed in the vehicle floor. To protect this housing from dirt, dust, and moisture, they are closed with a liquid seal. Sealing is an effective dispensing method for protecting components from external influences by creating a barrier.
A usually highly viscous and thixotropic sealant is applied to the components according to a predetermined two- or three-dimensional contour. The rheology of liquid sealants, combined with the built- in adhesion promoter, helps ensure that the cured sealant bead stays in place and maintains its predetermined profile and size.

Compared to conventional die-cut gaskets, liquid gasketing allows flexibility in part design and significantly reduces waste. If there are variations in the design of the mating surfaces of the parts, different gaskets would have to be produced, increasing the number of parts and inventory to manage. With a robotic dispensing cell, a large number of gasket patterns can be applied. In addition, the error rate in sealing can be reduced due to the automatic and precise positioning of the seals.
Conclusion
Numerous dispensing applications are needed for the production of new components for the production of electric motors and batteries. For all those products in the battery there are high requirements regarding their performance over lifetime. Hence, the process technologies and machines used to manufacture such products have to perform with highest possible Overall Equipment Effectiveness (OEE) at lowest possible total costs. Close cooperation between the customer, material producer and dispensing technology manufacturer is the key to success.
Carolin Gachstetter, Andreas Olkus, Markus Rieger, Frank Vercruysse, Wim Dexters.
are all from bdtronic GmbH