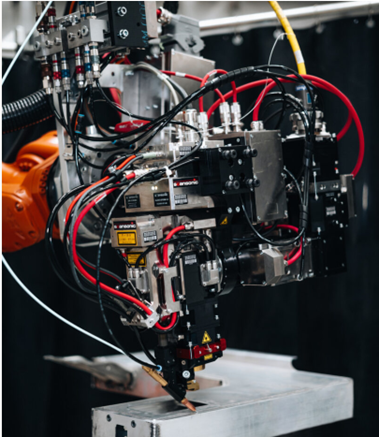
The Right Laser Optic for Every Weld
Philip Marben The battery enclosure is a central component of a battery-electric vehicle. Welding its various parts presents specific challenges
Philip Marben The battery enclosure is a central component of a battery-electric vehicle. Welding its various parts presents specific challenges
Integrating energy metering and legal metrology into EV fast charging stations is essential to deliver accuracy, transparency and trust Charles
Ignazio Dentici The automotive industry, having spent over a century perfecting internal combustion engine manufacturing, must now rapidly adapt to
Battery Design: The Epicentre of the EV Ecosystem Brian Whitaker Transitioning from gas-powered internal combustion engines (ICE) to clean energy
Leak Testing for Battery Systems in Electromobility: Challenges and Solutions Raphael Nold In recent years, electromobility has experienced remarkable growth,
Project SUSMAGPRO Sustainable Recovery, Reprocessing and Reuse of Rare-Earth Magnets in a European Circular Economy Editor As electrification continues to
The role of universities in the development of sustainable battery supply chains The University of Warwick highlights the breadth of
AI holds the key to making cleaner, greener and safer EV batteries a reality Krzysztof Slosarczyk The acceleration of Electric
Wireless Power Transmission: A game changer for Electric Vehicles Mark Philips Wireless Power Transmission (WPT), as the name suggests, transfers
Ultrasonic Welding: Green Manufacturing Technology for Battery Cell Production Axel Schneider In the dynamic world of electric vehicles, the efficient
E-Mobility Technology International has solidified its position as the premier global platform, shining a spotlight on the newest innovations, industry developments, and breaking news within the electric vehicle (EV) domain. By tracking technological progress from major players in the electric automotive sector, it serves as a dynamic hub for dialogue and knowledge sharing, offering fresh perspectives on tomorrow's technologies.
If you have a new innovative solution/ technology, or an exclusive technical article that is relevant to this industry that you’d like us to consider publishing, please email
info@e-motec.net.
E-Mobility Technology International the premier global platform, shining a spotlight on the newest innovations, industry developments, and breaking news within the electric vehicle (EV) domain.