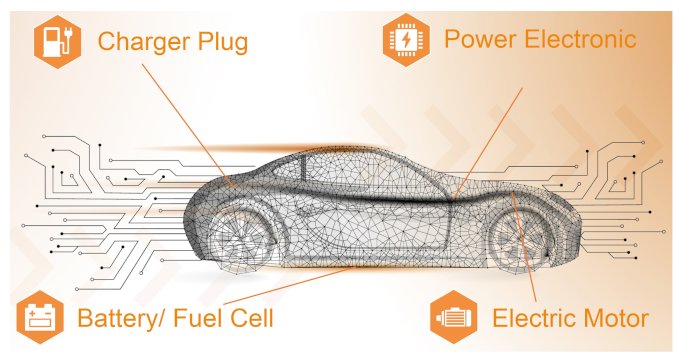
Efficiency is the motor of electromobility and pushing electric vehicle components as close to their performance limit as possible is the key. Platinum thin-film sensors make this possible.
Sensor technology has become a key component in supporting the revolution in electric mobility. Precise sensors, accurate data and reliable controls are essential for the rapid development and testing of powerful and reliable products. The demands in the electromobility industry are very high. In contrast to many other areas of electronics, vehicle components have to withstand higher loads for a much longer period of time. Automobile manufacturers require the automotive-supplier industry to ensure at least 10 years or 250,000 km of service life for their products. This makes it all the more important to stay close to the specification limits of the parts without exceeding these limits. This is where the highest performance is achieved, but loads beyond this often lead to irreparable damage to the sensitive components. Precise measurements are therefore crucial. Commonly used NTC sensors are an increasingly obvious weak point of many electric cars. Due to diffusion processes in the bulk material, the temperature coefficient curve shifts after some time and the precision of the measurement decreases. As a result, temperature limits can no longer be reached and necessary safety margins reduce the performance of the electronics.
Platinum thin-film sensors are the solution. A platinum layer on an aluminum substrate ensures an almost linear temperature coefficient and thus permits continually precise measurements. Heraeus already has years of experience with these sensors in other application areas and is now applying this knowledge to advances in electromobility. This expertise is specifically used in four application areas:
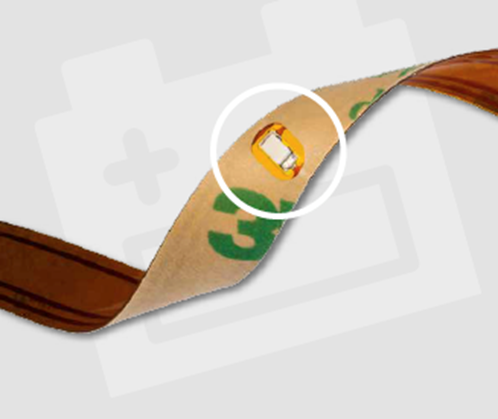
Charging plugs: Safe transfer of energy
Particularly from the safety point of view, the primary objective of optimizing loading times has reached its limits. The quality and reliability of the charging plugs must be guaranteed over a long time. At the same time, the charging performance should remain unchanged over the long term. However, the heat generated by the high energy transfer can damage both the plug and the connection in the car. To avoid this, precise, drift-free measurements over the entire service life are required. In addition, elevated temperatures must be detected quickly in order to reliably protect the user and the devices.
Platinum thin-film sensors have proven to provide long-term stability and offer the necessary measurement precision for the expected service life. The characteristics of platinum sensors in terms of drift stability, response behavior and precision enable them to meet stringent safety requirements for people and material and open the door for progressive developments and performance enhancements. The SMD version of the platinum sensor is pre-applied on a PCB and, due to the potential-free reverse side, simply positioned on the existing pin design using heat shrink tubing or metal springs. This flexible connection opens up new, advantageous design and thermal connection options. Placement directly on the metal pin guarantees the best response time for optimal protection.
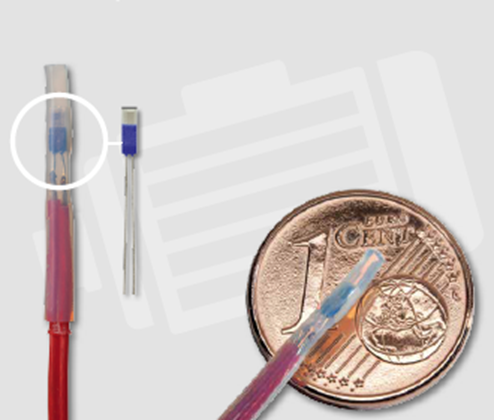
Battery: Long-lasting energy storage
Imperfections in battery temperature measurement require larger safety buffers, which in turn reduces range and power efficiency. However, the goal of operating batteries close to the limits requires a high level of measurement precision over a long period of time. In addition, the automotive environment demands the highest degree of reliability. Temperature information for charge and discharge must be provided without significant time delay. At the same time, measurements are made directly at the cell.
Platinum thin-film sensors are characterized by extremely high stability / low drift, allowing the entire working potential of the battery to be used risk-free for the long term. Temperature sensors are positioned and connected on flex boards. The elements can be positioned directly at the hot spots using self-adhesive film in order to achieve excellent response behavior. Plug-and-play assembly is made possible by the use of AEC Q200 compliant SMD chips in combination with standard connectors. The precision of the platinum sensors and their optimized combination with the ideal housing selection ensure greater safety, better performance and a longer service life in the long term.
Power electronics: More efficient control
Power electronic modules are responsible for power distribution and energy management in electric vehicles. The automotive industry poses a particular challenge for power electronics when it comes to long-term stability and reliability. The long service life and high precision of platinum sensors in the measurement range over 200 °C enable operation close to the load limits of the power chip. This results in significantly higher performance with lower energy consumption. At the same time, the higher application temperature opens up new possibilities for the use of future-oriented material systems based on SiC and GaN. In addition, specially developed sinterable temperature sensors in SMD format support innovative production methods and more compact designs.
Platinum temperature sensors can be positioned directly on the substrate of power electronics compactly and potential-free using soldering, adhesive or sintering processes. Temperature is measured at the precise critical location, with a fast response time. The insulated functional layer eliminates the need for additional structuring and insulation steps, resulting in maximum design freedom. Long-term stability and precision of the platinum sensor support the performance of the overall system. In addition to more compact designs, further development goals include more efficient production processes that make it possible, for example, to assemble all components in one process step. This calls for innovative assembly and connection technology, as well as temperature sensors for operating conditions above 200 °C.

Electric motor: The driving force
The electric motor is a critical component, and not only because it is very expensive. Motors with permanent magnets, as well as inductive machines, require a high level of protection, especially under full load. Temperature overloads must be reliably prevented throughout the entire service life, especially during exposure to mechanical stresses such as vibrations that occur during driving. A sensitive weak point is the enamel insulation of the copper connecting wires, which melt at high temperatures, leading to power losses and lasting damage to the electric motor. The large measurement range, the linear characteristic and the stability against drift in typical e motor temperature working ranges make it possible to optimally protect them over their entire life cycle without artificially reducing their performance for precision reasons. A “semi-flexible” housing technology offers the sensor element optimal mechanical protection. The platinum thin-film sensor technology used has proven to be highly stable and maintains the necessary measuring precision throughout the entire service life of the electric motor. A variety of available assembly options provide design freedom, including the ability to position the sensor within the motor housing adjacent to the coil, resulting in faster response times.
Summary
The most important factor for the development of electromobility is efficiency. However, this is not achieved by using the cheapest possible components, but by using high quality components that are constantly working at their performance limits. Platinum thin-film sensors are the best solution for persistently guaranteeing this performance thanks to precise temperature measurements. And demand is growing steadily – as can be seen from the example of China: A quota for electric cars and plug-in hybrids has already been introduced there, which states that domestic and foreign car manufacturers must meet minimum targets for the percentage of alternative drive units in production and sales. In Europe, too, the expansion of electromobility continues to accelerate. The use of efficient sensor technology thus represents an important success factor in competition on the global market. To be able to serve this demand, platinum thin-film sensors are indispensable and the technology of the future. The product solutions, development expertise, and industry experience of Heraeus Nexensos contribute to ensuring the favorable framework conditions and quality assurance for successful market development. With sensor products and development expertise, Heraeus helps its partners to drive progress in electric mobility forward – continually pushing the limits of what is technically possible – while adding new opportunities and value.
Martin Bleifuss Dipl.-Ing.(FH)