At the heart of every plug-in, hybrid, or pure electric vehicle (EV) is a power source: a rechargeable battery pack, based on lithium-ion (li-ion) technology. And, whatever the battery technology — cylindrical, prismatic, pouch, even solid-state — it is, the evolution of this power source that will determine the future of the EV industry. Critical to the assembly of all these battery designs is a metal-joining technology — ultrasonic metal welding.
Since the 1990s, ultrasonic metal welding has been widely used by battery and EV makers because it is able to bond very thin materials — down to 5 µm foils — and can do so in assemblies of 100 layers or more. This capability is essential to successful assembly of high-power lithium batteries and super capacitors. At the same time, the process can also handle the assembly and splicing of thicker battery foils and the much larger connections essential to power distribution throughout the vehicle. These larger connections include copper or aluminum plate busbars as well as wire harnesses and terminals.
Understanding the Ultrasonic Metal Welding Process
Unlike resistance or laser welding, ultrasonic welds and splices never melt the materials that are being joined. Such melting is essential to joining high-strength ferrous metals, but melting is a problem for softer, nonferrous metals for two reasons. First, melting can form intermetallic compounds or galvanic corrosion that cause premature material, connection and battery failure. Second, a melt-bonding process involving multiple, thin nonferrous foils would greatly complicate successful assembly, due to the fragility of the foils.
Ultrasonic welds and splices are accomplished by applying high-frequency vibration to two metal parts that are held between a “horn” above and an “anvil” below. The lower metal component is placed on the anvil, where it is gripped by a knurl pattern and held stationary for welding. Before welding, the upper component is placed on top. The welder’s actuator moves into position, contacting the upper component and compressing the assembly.
Welding takes place when the horn vibrates horizontally at high frequency. The initial oscillations “scrub” away surface oxides, contaminants, and special material coatings at the interface(s) of the metal components to create a clean bonding surface. As the oscillation continues, the frictional heat breaks down surface asperities until a continuous weld area is produced. Weld bonds are characterized by atomic diffusion across the interface of the joined parts, which then recrystallize into finely-grained structures, similar in structure to cold-worked metals. The entire process is completed in a fraction of a second.

Figure 1. Close-up of the ultrasonic metal welding process, showing the position of the horn, anvil and metal parts. Downward pressure and horizontal oscillating motion (amplitude) create friction that results in a metal-to-metal bond in the weld zone. Image courtesy of Emerson.
Different variations of the process are gentle enough to join multiple thin, relatively fragile layers, such as the thin foils and tabs that connect the many individual cells that form a lithium-ion battery. Yet, with different parameters, the weld process is rugged enough to create strong bonds between larger metal components and conductors.
Whether individual batteries are li-ion cylindrical or prismatic types, or newer li-polymer pouch or solid-state designs, ultrasonic welds provide the most proven and reliable solution for interconnecting the nickel and copper tabs and foils that are typically used as anode current collectors as well as the aluminum foils and tabs used in many cathode current collector structures. Welding of these or other small battery structures is typically done at a frequency of 40 kHz with low amplitude, due to the low number of very thin foil structures being joined. In prismatic cells, 40 kHz ultrasonic welding can join up to 20 thin copper or aluminum foils, depending on the size/area of the weld. This high-frequency, low-amplitude approach simplifies the assembly of multilayer battery designs.
When multiple batteries are joined into larger battery modules and modules are joined into a pack, the ultrasonic process handles welds involving busbars, harnesses and cables. For these larger welds, a lower frequency of 20 kHz with a higher amplitude is often used. At this frequency, the welding process can use up to 5500 W of available power and up to 80 microns of horizontal motion, or amplitude.
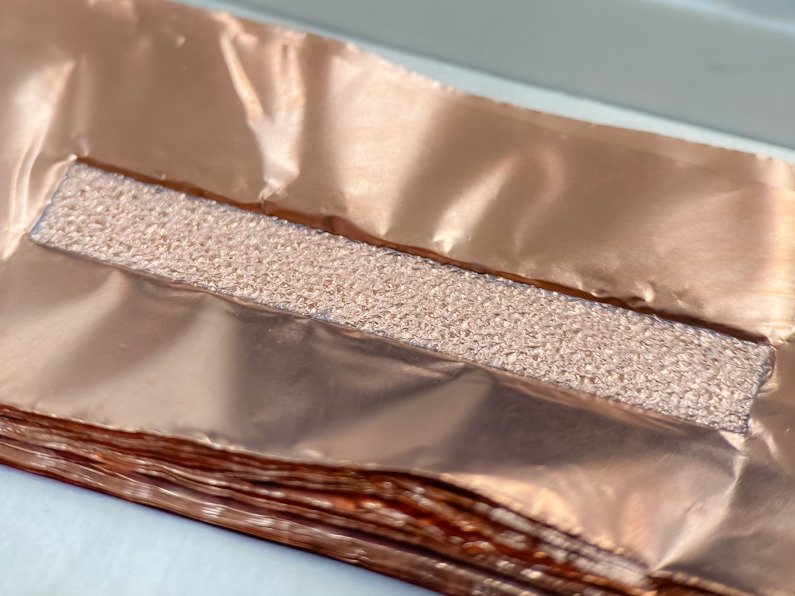
Ultrasonic welds provide the most proven and reliable solution for interconnecting the thin tabs and foils that are typically used as anode current collectors as well as the aluminum foils and tabs used in many cathode current collector structures.
Ultrasonic metal welding with a 20 kHz frequency is also typically used on large battery packs for electric cars and battery packs for special vehicles (specialized mining vehicles, large drones, etc.). Applications like these might use prismatic batteries that, depending on weld size and area, can join foils from 100 or more layers onto a single tab.
In all cases, the friction generated by the ultrasonic weld process creates heat as the metal parts oscillate against each other, but not enough heat to melt the metals. Typically, the heat generated equals about one-third to one-half of the absolute melting point of each material. This solid-state process creates a strong welded bond, yet avoids burning through thin or fragile foils or melting the materials and forming intermetallic compounds.
CHART: Ultrasonic metal welding and splicing: Process benefits
- Works with a wide range of nonferrous materials
- Creates permanent, metallurgical bond between dissimilar metals
- No melting required — no change to chemistry or metallurgy of materials
- Ideal for joining highly conductive alloys; reactivity of materials doesn’t matter
- Creates no intermetallic compounds, particulates or corrosion-causing reactions
- Ideal for bonding thin, fragile metal films and structures
- Multiple methods of control enable process customization, repeatability and SPC
- Low energy input (30x lower energy use than fusion or resistance welding); no consumables
- Lowest total cost per weld of any welding technology
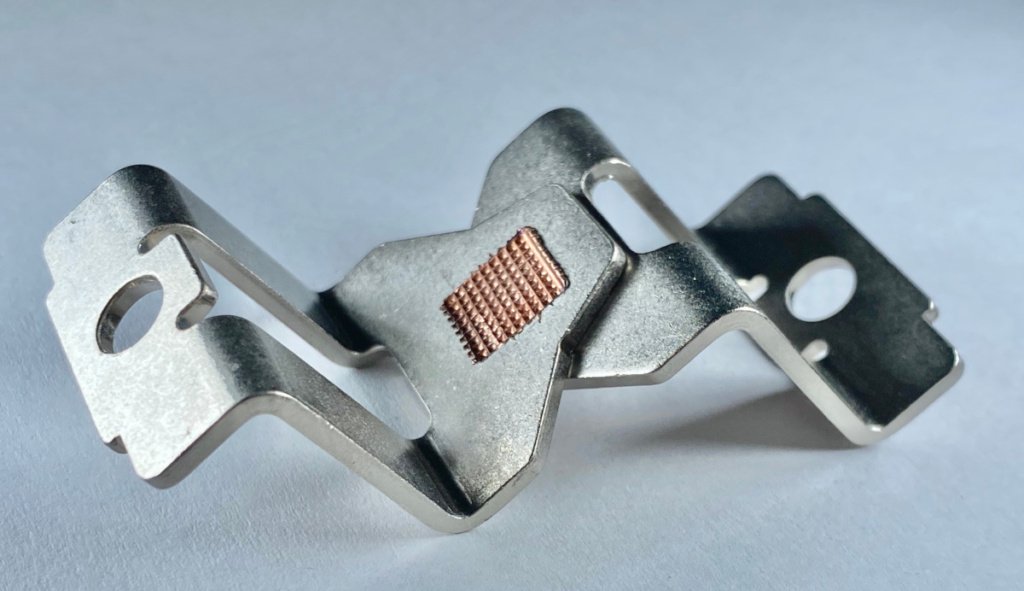
: Ultrasonic metal welds or splices can bond relatively thick cables, busbars and terminations. Because the process joins conductive metals without melting them, the integrity and characteristics of the metals are unaffected.
Success is in the details
Ultrasonic metal welding is a specialized process that demands very precise control over several critical factors: weld energy control, weld amplitude control and weld tooling quality. Success is in the details.
Weld energy control. Ultrasonic metal welding systems offer multiple modes of control over weld quality. They can weld for a fixed length of time (time mode) or weld to a particular finished weld height (height mode); however, welding in energy mode generally provides the best results. This mode, which ensures that each weld receives an identical amount of joining energy, is calculated as follows:
E = P × T
where E equals energy in joules, P equals power in watts, and T equals time in seconds. The watts of power (P) that are consumed in the weld are further broken down as:
P = F × A
where F equals the downward force exerted on the weld (typically by a pneumatic actuator) and A equals the amplitude of the vibrating shear force directed into the weld.
Thus, when welding in energy mode, an ultrasonic metal welder automatically compensates (using time) for commonly occurring differences in the surface conditions of the metals being joined. Put another way, adjoining metal surfaces that have a greater degree of oxidation or contamination will require a longer initial period of “scrubbing” before conductivity is established and effective metal-to-metal joining takes place. Energy mode welding readily compensates for these differences.
Weld amplitude control. In an ultrasonic metal weld, amplitude refers to the length of the oscillation delivered to the weld zone by the upper moving metal part. Successful and repeatable ultrasonic metal weld production demands that this amplitude be carefully calculated based on the materials being assembled and then precisely controlled throughout the production process using the capabilities of the weld power supply, converter and sonotrode/horn assembly.
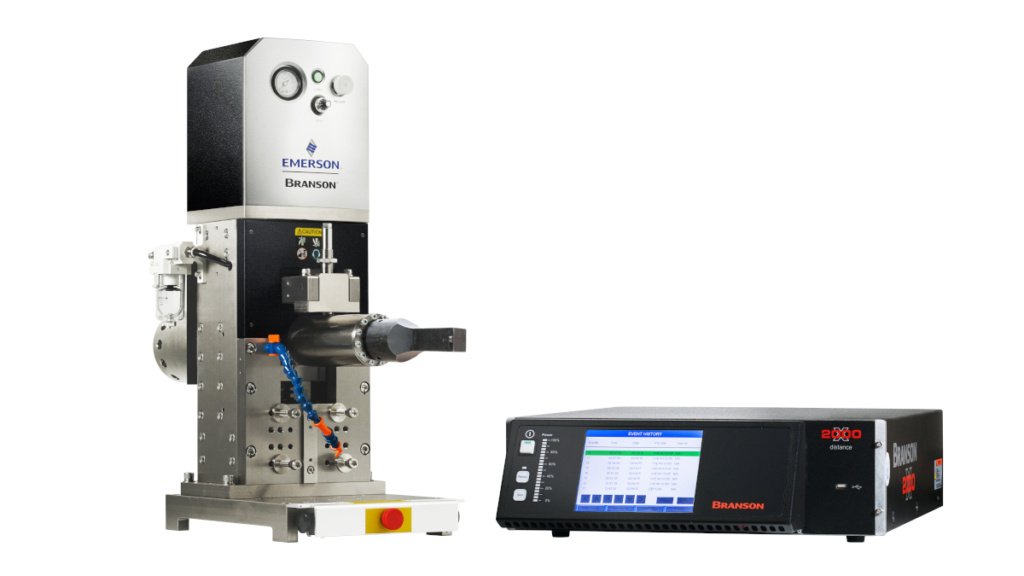
Weld tooling. Another major contributing factor in ultrasonic metal welding success is the design and material composition of weld tooling, particularly the anvil and the sonotrode or horn. The anvil is essential for holding the stationary metal part firmly in place, while the horn must effectively “grip” the moving metal part, precisely delivering the oscillating shear forces through it that will establish the bond. The ability of the horn to grip the upper part is created through a specialized machining process that produces a pattern of spherical, diamond or serrated knurls on the tip of the horn. These knurls, together with the overall design of the horn, are another essential factor in the ultrasonic metal welding process.
Weld process documentation. In a growing number of industries, device assembly and manufacturing data may be needed to document and validate product quality, meet regulatory requirements, or support product warranty or service operations. High-quality ultrasonic welding equipment has the capability to record weld parameters and process data as needed to comply with diverse global requirements.
Conclusion
Though ultrasonic metal welding and splicing are relatively simple to describe in theory — a formula of amplitude and energy that creates surface-level friction, heat and bonding between metal parts — the process can be difficult to replicate with repeatability, reliability and productivity on an industrial scale. Every element of the process — equipment quality, weld mode controls, tooling precision and durability, data collection and communications, immediate and global technical support — factors into a manufacturer’s ability to develop and build the advanced batteries that power the EVs of today and tomorrow.
About the Author
Alex Yeung is the global business development manager, Branson Welding and Assembly at Emerson, leading sales, application development and business development for BransonTM metal welding technology. Yeung holds a B.E. in mechanical engineering from Hong Kong Polytechnic University.