As the EV market continues to evolve, with the demand for both Hybrid and Battery Electric Vehicles growing year on year, the technologies used to produce the many components required for these clean and increasingly efficient vehicles are also developing to support the transition away from conventional internal combustion engines.
Although volumes are increasing, there is still some way to go before production of electric vehicles, in all of their forms, and the batteries needed to power them, reach their peak. This means that currently, flexibility in productions systems is an essential attribute if component manufacturers are to produce different component types in the required batch sizes. Some of the key components that fall into this category include HV cables, battery connections and cell connectors, each of which require to be welded in a diverse selection of sizes and designs.
(Aluminium bus bar and aluminium cable in tubular lug)
High-voltage cable with 35 mm2 and 95 mm2 welded to electrical connectors
Just as todays EV’s incorporate the latest generation technologies, so too must the systems and processes used to manufacture the individual components, if they are to be capable of achieving the rigorous consistency and quality standards required of the sector.
Following a comprehensive consultation process to identify the specific needs of the sector, Telsonic AG have developed the Telso®Terminal TT7 metal welding system. This self-contained system encompasses multiple latest generation technologies which together are transforming ultrasonic metal welding applications on EV components. The high-performance system is capable of welding a wide range of products such as HV cables, battery connections and cell connectors that require welding in a diverse selection of configurations. A key feature of the TT7 is its modular structure which enables quick re-configuration between applications.
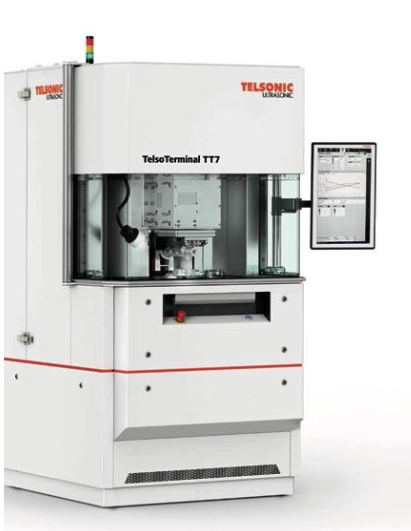
Based upon a compact and modern design, this modular system delivers a host of advantages for users including outstanding process control, through the use of digital technology, standard interfaces for digital networking, and easy integration into factory automation systems. The new system also incorporates the latest version of the proven PowerWheel® welding technology as a standard feature, ensuring maximum reliability and optimum process control for welding metal cable cross sections up to 200mm2.
PowerWheel® welding technology uses an innovative concept to vibrate the sonotrode, which is excited in a torsional manner. With scalable welding power of between 7.2kW and 14.4kW, the optimum welding power can be tailored exactly to suit to each application.
(The new Telso®Terminal TT7 features a modern, innovative system design and multiple features which guarantee the highest levels of quality and performance for metal welding applications)
Compact Welds Plus Increased Flexibility
As space for components and sub-assemblies is always at a premium in any vehicle, any opportunity to save space, however little, by manufacturing more compact components is always welcomed. The Telso®Terminal TT7 metal welding system, with its PowerWheel® technology, makes it possible to produce welds that are up to 30% narrower and higher compared to those produced by a linear ultrasonic welding system. This can often also result in considerable savings in material.
A further benefit is that thicker terminal connections can be welded with increased strength. The welding takes place in a swaying and rolling motion directly above the weld area. As a result, the maximum amplitude is always in the centre of the welding area and the energy is directed and focused within the welding zone. The PowerWheel® standardised sonotrodes are optimised for copper and aluminium wires, meet the requirements of OEM’s and harness makers, as well as the USCAR 38 standard (Performance specification for ultrasonically welded cable terminations). As with conventional ultrasonic welding, the PowerWheel® system can weld all non-ferrous metals.
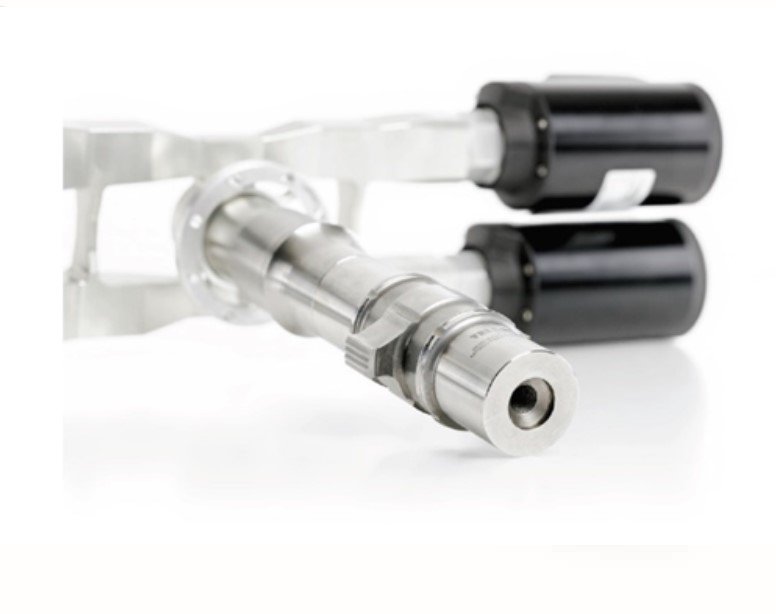
in metal-welding applications)
The ability to exchange tools on the TT7 in less than five minutes maximises productive time and flexibility. In addition, self-centring and positioning (Poka Yoke) of the PowerWheel® sonotrode eliminates the possibility of error during set up and greatly reduces any adjustments which may be required. Welding amplitude can, if required, be optimised for individual applications by means of a booster.
Delivering Quality And Consistency Through Process Monitoring
Telso®Flex is used to monitor and log each application and operation. Within a flexible production environment, it is likely that there will be multiple changes in the part types being produced. Telso®Flex reduces the potential for errors during changeover through the use of a comprehensive application changeover checklist which provides clear step by step instructions for the operator. Each step is described using a combination of text and images and the instructions fall into two categories – either a simple task or question or verification of application specific information. For example, the part number of the sonotrode being used must be scanned and gets checked. Production can only begin upon successful completion of all changeover steps. If any steps are overlooked, the operator will be prompted to revisit and complete that step. Unauthorised changes are prevented with user and rights management for three user groups.
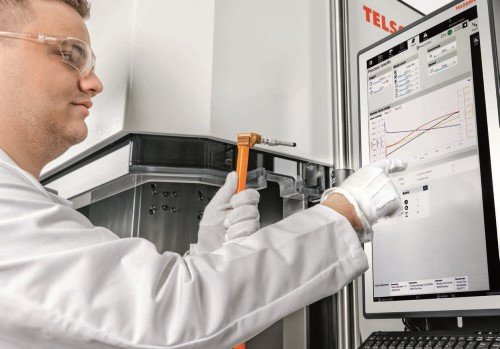
During production, Telso®Flex offers various functions that ensure the highest levels of quality and productivity through continuous quality monitoring. These quality checks begin at the outset when the terminal and wire are being clamped. If the clamp detects a difference in height, for example due to thickness variations or the clamp operating on just one side, the operator will be alerted to the error, and it will not be possible to initiate the welding process. The same is true should the wrong diameter of wire be detected during the clamping
The system detects trends that can be used to quickly highlight and prevent possible production errors. Weld limits and results are shown both as numerical values and graphically as coloured bars, with blue representing values within limits, yellow as close to limit and red as outside of specified limits. The welding curves for power and distance are also displayed. All welding results, machine events, parameters and data are saved for traceability and analysis purposes. This data can then be exported from the controller via USB and Ethernet. In addition, the software presents operators with valuable information and topic-related assistance which reduces unproductive time during maintenance and service procedures.
The intuitive 21.5” capacitive touchscreen interface ensures that operators have all relevant information available to them at a glance, and with the Equipment Manager feature looking after acoustics and wear parts, which clarifies which components are on the machine, operation is made even simpler. In addition to the comprehensive standard specification of the new TT7, a range of options are available to suit individual customer requirements. These include wire stop with position detection, wire clamping for single or multiple cables and a bad part cutter to destroy parts where welds are deemed out of specification.
Liquid cooling and heating is used to adjust the temperature of the tools, keeping them within the optimum temperature range. The system software continually monitors the temperature and can stop production, protecting the system from overheating as a result of incorrect parameter setting etc. This feature, unique to Telsonic, not only minimises any variations between welds but also shortens the weld cycle, improving overall efficiency.
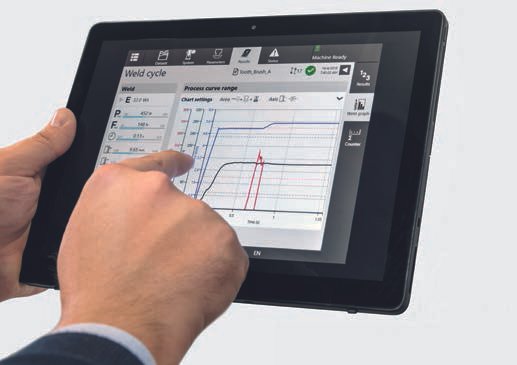
Simple connection to customer’s MES (Manufacturing Execution Systems) is achieved through the Telso®Con interface which provides a flexible solution via OPC-UA. This allows production orders and technical parameters to be transferred and shared over the network.
“Telsonic remain committed to working within the industry at all levels to not only address the needs of today but continue to develop the products which will be a mainstay of the EV sector as volumes increase and the technology within the vehicles matures”.
Dirk Schnur Chief Marketing Officer Telsonic