Advantages of material processing with thermoplastics in the EV industry
Lea Kroth, Denis Wittmaier & George Tank
Particle-free, safe, environmentally friendly, fast and consistent. Laser plastic welding offers flexible solutions to joining challenges in the EV industry.
High-performance polymers are increasingly replacing assemblies made of metal and conventional engineering plastics thanks to their superior properties, such as high heat and chemical resistance, low weight and dimensional stability. This trend is particularly favored in the automotive industry by the increasing system complexity and integration of functionalities with simultaneous demand for a reduction in installation space and weight. Typical areas of use for high-performance plastics are applications with high thermal and mechanical loads along the entire engine and drive train, assemblies and media lines for thermal management, but also components specifically for EV industry, such as battery trays, fluid systems, actuators or electrical and electronic systems in general.
In addition to the material properties, joining technologies such as laser plastic welding also meet all the needed requirements for assembly. The connection technology used should not restrict design freedom, ensure a particle-free, media-tight and robust connection and expose sensitive electronic assemblies to as little mechanical and thermal stress as possible during the joining process. From this point of view, laser transmission welding of plastics has already established itself as an ideal and often alternative-free process. The possibilities of inline process monitoring, the high achievable weld seam strength and the fact that no filler materials are required also speak for the use of laser technology. Furthermore, there is no vibration input and no flash formation. The most frequently used variant is the laser transmission welding, where two joining partners are welded in an overlapping arrangement. The upper joining partner is laser-transparent, so that the laser beam passes through this part and is converted into heat at the contact point in the lower, absorbent component, thus heating it directly. Both parts plasticize at the point of contact, creating a material bond.
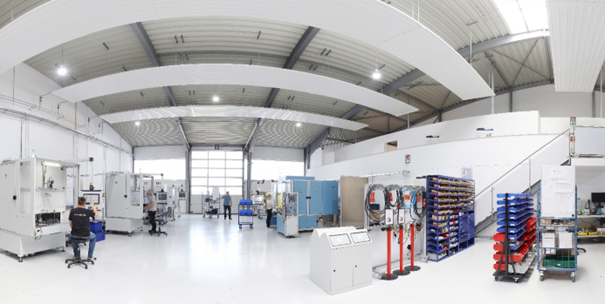
Figure 1: Main production site in Erlangen, Germany
Different parts and requirements utilize different welding principles. In quasi-simultaneous welding, the laser beam travels along the specified welding contour several times at a feed rate of up to several thousand millimeters per second. This ensures a targeted and uniform energy input into the joining partners and heats the joining zone up to the molten temperature range. At the same time, a constant force is exerted on the joining assembly to ensure heat conduction between the two joining partners. The combination of the joining force and the laser beam, which scans the contour several times at high speed, results in a relative setting movement between the two joining partners, which is precisely recorded by an integrated displacement measuring system. The welding process is usually set so that a welding collapse is created that is greater than the flatness tolerance of the two joining partners. The position measuring system is an integrated and cycle time-neutral process monitoring system during the welding process. In practice, this method has proven to be robust; it is state of the art in industry and ensures a consistently high-quality weld seam. This is why quasi-simultaneous welding is the preferred process variant for most applications. In addition, a pyrometer can be used for inline quality assurance. The pyrometer detects the heat radiation emitted in the welding zone and can be used as a control variable for the quasi-simultaneous welding process along with the welding collapse. A target value for the time-temperature curve can be saved and provided with practicable tolerances as an envelope curve (Figure 2)
Another tool for non-destructive component testing that is often integrated is an. With the help of IR cameras, it is possible to control the weld seam quality even if the parts are not transparent for the human eye. The technology can either be integrated in the machine for inline measurement or be used as a stand-alone system for offline inspections

Figure 2: Process cockpit of the user interface with pyrometer signal

Figure 3: Visible weld seam (left) with the use of EvoInspect Vision in comparison to a welded part with a black colored laser-transmissive cover (normal camera image, right)
For radially symmetrical applications like cooling pipes in the thermal management of EV, the radial welding, a special form of contour welding is used. During the contour welding process, the laser spot is moved slowly along the welding contour one or more times. This allows the material to cool down and solidify between each pass over a point of the weld. One major difference between this special form and the other process variants of laser plastic welding is the introduction of the joining pressure into the joining zone. The radially symmetrical structure of the assembly in the welding area allows for a press fit, which achieves the necessary joining pressure for heat conduction. This often eliminates the need for clamping technology in contact with the component. The economic system designs and short overall process times are positive results. For this process, as well as for quasi-simultaneous welding, a pyrometer can be used for inline quality assurance and closed-loop control.
ARaymond automation teams’ fluid components (PA) can be seen as an example for these parts (Figure 4). One of their machines, a customized EVO 8800, includes 4 laser sources, multiple part fixtures and can weld tubular components up to 2000 mm in length with 24 inlets. For inline non-destructive quality assurance, the system utilizes Vision Inspection systems and pyrometers. Through the flexibility of the system, different pipe applications varying in length and shape can be welded on this machine in a repeatable and reliable process.

Figure 4: ARaymonds ‘laser welded fluid systems
Prominent examples of quasi-simultaneous or contour welding of automotive parts include lighting (often made of PC, PMMA, or ABS, Figure 6), sensor housing (such as PPS), or the emblem rear actuation with integrated camera shown in Figure 5, made out of PA6 and PA66 (GF). These parts have high requirements regarding aesthetics and hermetic sealing.


Figure 5: emblem rear actuation with integrated camera Figure 6: lighting for Mercedes
Evosys is always developing new and innovative solutions to meet the challenges of the material and the increasing demands in the rapidly changing field of electro mobility. Demanding material like PPS, often used in EV because of its stability to thermal degradation, chemicals and hot water can be welded better with high process reliability and quality using special designed process setup, Next Generation Optics (NGO). Advanced Quasi-Simultaneous Welding (AQW), an innovative and patented technique, is deployed to decrease welding time of parts by over 40 % while increasing the burst pressure by more than 20 % compared to conventionally welded parts. Technology like direct laser joining of metals and polymers open up new areas of application with metal-plastic composites and hybrid structures.
The large number and special features of the individual processes in the field of EV’s make it necessary to develop customized and innovative solutions. This is why here at Evosys, we consider ourselves the market leader, for developing the optimal tailored machine for every task in a customer-oriented matter.We like to build our customer machine around their applications to fit their production needs.
Lea Kroth, Denis Wittmaier & George Tank from Evosys