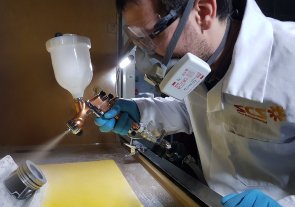
Jörg Feist, Silvia Araguas Rodriguez, Jim Hickey, Ahmed Zaid
Sophisticated temperature detection is needed in traditional combustion engines, but how can the latest thermal mapping technology drive development in cleaner automotive propulsion systems?
High temperatures are common in combustion engines. Some automotive pistons and turbochargers operate between 400 °C – 700 °C, with some high-performance turbochargers reaching beyond 800 °C. To drive higher thermodynamic efficiencies, operating temperatures in gas turbines now approach 1600 °C. Amongst other challenges, such high temperatures can shorten component life-time, requiring accurate and precise temperature characterisation.
Many temperature measurement technologies have been developed over time, including pyrometry, infrared cameras and thermocouples. The latest in an engineer’s temperature measurement toolbox are Thermal History Coatings (THC) and Thermal History Paints (THPs).
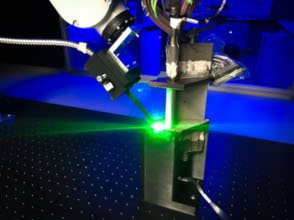
THCs and THPs have been developed for automotive and gas turbine applications, covering temperatures between 150 °C and 1600 °C. The coating or paint can ‘remember’ their highest exposure temperatures. When applied to a component, these memorised temperatures can be read from the THC/THP post-operation using a bespoke laser scanning system, providing high-resolution temperature maps. The data is plotted on a CAD file, mapping hot-spots or in-built cooling effectiveness as examples.
The phosphorescence temperature sensor
Temperature, as a manifestation of thermal energy, is not directly empirically measured. Instead, engineers measure analogous parameters to deduce temperature: for mercury thermometers, this is the liquid volume; for thermocouples, the voltage between two wires. For THPs and THCs, the analogous parameter is phosphorescence, the phenomenon behind glow-in-the-dark stickers, road markings, and watch handles.
THPs are comprised of a ceramic pigment doped with a rare-earth ion. The pigment is mixed with a water-based binder. Through careful design, these materials undergo a gradual structural change when exposed to increasing temperatures. Known as the amorphous-to-crystalline transition, the THP molecules continuously rearrange towards a crystalline structure[ie1] . This change is non-reversible: the partially arranged structure is memorised even when cooled. The degree of crystallinity (and hence temperature history) is monitored by measuring the changes in the phosphorescence of the rare-earth dopant ions.
To measure component temperatures practically, the THPs are deposited as a thin 30 µm functional coating on the component. During component testing (e.g. an engine or rig test), the THP locally changes with exposure temperatures. These changes are measured afterwards using SCS’s bespoke optical instrumentation. A laser-pulse is delivered to a pre-determined THP location, triggering paint phosphorescence. Post-pulse, the phosphorescence signal intensity decays with time. Known as an afterglow, as seen in Fig.1 (left), the signal decays as a single exponential, with the magnitude of the decay time (τ, or lifetime decay) increasing proportionally to the degree of crystallinity, and therefore temperature. Through calibration of lifetime decay measured at known temperatures, the lifetime decay measured on the components is related to the past maximum exposure temperature (Fig. 1 (right)).
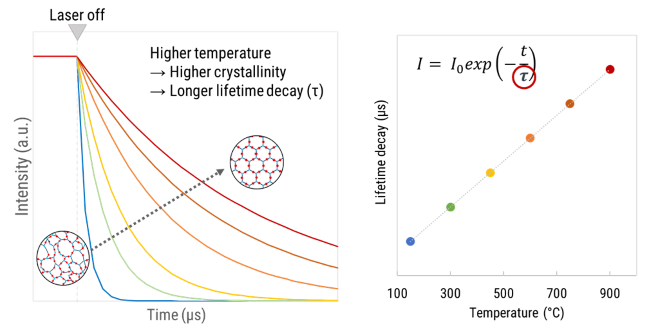
Figure 1: (left) The phosphorescence lifetime decay plots plotted[ie2] against time for several exposure temperatures. Plots of lifetime decay with known temperature are used to calibrate unknown component temperatures (right).
Temperature detection needs for EV Hot Fuel-cells
Efficient, fuel-flexible and now with specific energy densities that compete with internal combustion engines, fuel-cells are promising power sources for auto-applications.
Proton Exchange Membrane Fuel-Cells (PEMFCs) and Solid Oxide Fuel-Cells (SOFCs) are the two main fuel-cell technologies used or in development for auto-applications. Momentum in fuel-cells is gathering with Hyundai, Toyota and Honda already offering passenger hydrogen-fuelled PEMFC vehicles. Hyundai, BMW, Mercedes and Volvo Trucks are also renewing R&D into fuel-cells for passenger and haulage vehicles.
SOFCs will make their way into auto-applications, but challenges to their widespread adoption as a low-carbon power source remain. Carefully characterising fuel-cell operating temperatures is key to their deployment.
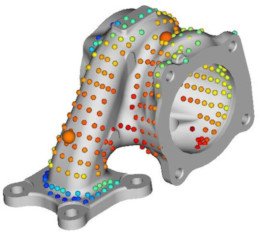
SCS’s technology has been implemented on fuel-cells, successfully mapping temperature history profiles of SOFCs operating at ~600 °C in cell areas inaccessible to other techniques like thermocouples or pyrometers. Through its application on ceramic thermal barrier coatings used on turbine components, SCS’s technology has also been proven to be fully compatible with the fuel-cell materials, especially SOFCs.
Key to the good operation of a fuel-cell in a vehicle is to carefully manage its operating temperature, requiring well-engineered onboard thermal management in the form of advanced heat-exchangers, condensers and distributed heat-sources as examples. SCS is well positioned to characterise these types of systems, with experience in applying its technology to compressor turbine wheels and heat exchangers.
Electric motors
Contrary to combustion engines, the efficiency of electric motors falls with temperature. Good motor thermal management is therefore essential since overheating not only reduces efficiency but also motor-component lifetime.
Helping to drive the auto-sector’s transition to carbon-free propulsion systems, motor developers are reducing motor size, weight, and cost as well as improving torque/power control and efficiency. Trade-offs exist between these parameters however and good thermal management is a key bottleneck: pushing more current through motor windings will boost torque, but the increase in Joule heating will need to be accounted for.
Motor thermal management is complex; even reliably measuring temperatures in the inaccessible interior of an operating motor is challenging. Conventional temperature measurement tools used to this end have downsides. Pyrometers for example require optical access, therefore potentially missing hotspots. Thermocouples are sensitive to a motor’s magnetic field. Thermal modelling is a credible approach, but model qualification and accuracy depend on the supplied conditions of a real-experiment, such as thermal coefficients and loss distribution.
THPs and THCs developed by SCS are promising technologies that offer an elegant path around these limitations. THP technology has been demonstrated for temperatures between 150 °C – 900 °C, well above the highest temperatures typical in electric motors (<300 °C). Offline temperature measurement (i.e. post-operation) means component visibility is not necessary during operation, thereby allowing for different thermal management designs to be tested and their effectiveness assessed. In short, thermal surface maps with a spatial-resolution of 1 mm in inaccessible interiors of a motor are possible and interference from a motor’s magnetic field does not need to be accounted for.
An alternative to clean EVs: Hydrogen Internal Combustion Engines
Over 50% of the UK electricity demand is still supplied with fossil-fuels. Hence EVs will not be completely carbon neutral when getting their power through the national grid. Coupled with a projected uptick in green hydrogen production, there is therefore renewed interest in re-engineering internal combustion engines (ICEs) to combust hydrogen. ICEs still enjoy significant cost and supply-chain maturity advantages over fuel-cells. ICEs also still edge fuel-cells when it comes to power-density, meaning they could be particularly useful for vehicles requiring high-power-bursts, such as those used in mining or heavy lifting.
Technical challenges to hydrogen-fuelled ICEs remain however. Whilst CO2 free, high-temperature, stoichiometric combustion of hydrogen with air produces NOx. Leaner fuel dramatically reduces NOx emissions and makes a hydrogen ICE run more efficiently, but this erodes ICE’s power advantage over fuel-cells, meaning power-boosting technologies like turbochargers would be required. Leaner fuelling also generally increases the operating temperature of the engine. This coupled with the presence of engine hotspots and hydrogen’s low autoignition temperature can lead to unplanned ignition, which can ultimately destroy an engine. Carefully characterising hydrogen ICE temperatures to identify and mitigate against hot-spots would therefore aid their commercial deployment. To this end, SCS’s technology has been used to measure temperatures in hard-to-access regions of ICEs, like pistons and valves. Applications in hydrogen engines would be a logical next-step.
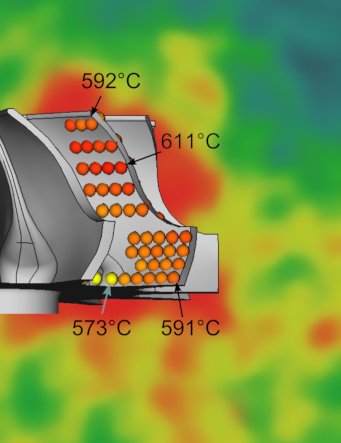
Outlook
Future automotive propulsion systems will be net-zero. However, this will not be possible with electric cars alone, likely requiring complementary propulsion technologies like thermal engines. A quick change to electric propulsion or hydrogen-powered cars requires a bedrock of enabling technologies to be developed and deployed. The need to analyse and validate thermally loaded parts in this sector will not disappear, and will require existing technologies to adopt. In the future THP and THC could be ‘hot’ candidates to support validation and durability testing to accelerate the development of cleaner cars.
[/et_pb_text][/et_pb_column][/et_pb_row][/et_pb_section]