
Cooling solutions secure performance and longevity in e-vehicles.
Li-ion battery operating temperature plays a decisive role in functionality and especially lifespan in high-performance batteries. Keeping to a constant temperature profile is essential in ensuring long-term performance in EV batteries and stationary energy storage modules.
Like people, Li-ion batteries have a definite comfort zone when it comes to temperature – they feel at their best in temperatures between 20 and 30°C, and achieve their maximum electrical performance and durability in this temperature range. Temperatures that are too low or too high will affect performance. The liquid inside the battery (electrolyte, acid or conductive paste) becomes viscous and carries less charge when temperatures drop. Apart from that, sub-zero temperatures cause issues in the electrochemical reaction at the electrodes, which are usually made of graphite and transition metals. The result is a significant drop in performance and range. Cell oxidation rates increase at temperatures above 30°C, leading to more rapid battery deterioration – and on to declining performance and diminishing capacity. Operation at over 40°C may even cause permanent damage.
EV manufacturers usually install liquid cooling systems to keep operating temperatures constant within the optimum range. The advantage of liquid cooling systems is that they carry off relatively large amounts of heat at uniform rates. Systems of this type are closely matched to the batteries. Li-ion batteries in electric vehicles are often equipped with cylindrical, prismatic or pouch cells surrounded by channels for the cooling fluid to circulate from the cooling system. Hardly any auxiliary power is required in contrast to air cooling; this makes the process highly energy-efficient. Each battery cell is usually equipped with a sensor to measure voltage, capacity and temperature within the cell for monitoring using a battery management system. This battery management system communicates with the cooling system, which then adjusts to situational requirements.
Pioneer in customised liquid cooling
Based in Sassenberg near Münster, Germany, Technotrans was one of the first manufacturers of liquid-based battery and charging cable cooling systems on the market. Together with Siemens, the company launched a prestigious project in Qatar towards integrating a bespoke cooling solution in e-trams without overhead lines as early as in 2011. The company also developed a system to ensure constant operating temperatures in hybrid energy storage systems consisting of capacitors (supercaps) and Li-Ion batteries even under extremely challenging ambient temperatures of above 50°C in some cases as well as high humidity and sand ingress. In addition, it developed an especially lightweight system to keep the total weight of the tram down.
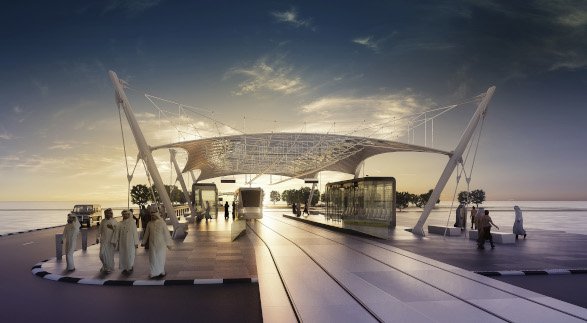
Energy storage cooling systems from Technotrans ride along in trams and regional trains in Europe Asia and the Americas, and cool inverter stations for rail and bus projects worldwide. Other fields of application include electric buses, trucks and vehicles in seaports and airports. Demands may have increased with time, but the development process has remained largely the same for the system manufacturer – designing batteries and the corresponding cooling system is a very precise process highly dependent on customer specifications, in which a variety of factors play a key role. For example, battery power and cooling requirements are based on regular fixed routes that e-buses run in public transport. Not only distances, but also gradients need to be included in these specific route profiles. An e-bus that has to deal with heavy gradients such as while crossing bridges needs more power at this point – and therefore also more cooling power – than on a route that remains flat. Problems arise when battery performance and capacity begin to diminish early due to temperature. Operators can no longer run the intended routes with the issue eventually being passed onto the battery manufacturer, which cannot fulfill its guarantee of usually five years and has to provide a replacement.
High-power charging – advanced fast-charging stations

Not only high-performance batteries but expansion in the charging infrastructure will be essential if electric vehicles are to develop into the transportation of choice in the long term. Many vehicle manufacturers have been investing in high-power charging (HPC) to allow a full charge in a matter of minutes. Charging cables need to transfer large amounts of power at around 300 to 400 kW in an extremely short time for HPC to work. This causes significant heating from electrical resistance within the cable depending on cable length, cross-section area and conductivity in the wire cores. The copper cores are surrounded by liquid-bearing tubes for cooling. The cooling unit is usually integrated into the charging station and uses active and passive cooled charge cable cooling modules, which means either a compressor or ambient air, depending on requirements. Manufacturers attach great importance to sleek, space-saving designs in modern charging stations, which also poses a challenge when developing the components. Cooling system manufacturers are often left out of the loop in this part of the design process, only to be involved much later when installation space and requirements have already been specified; Technotrans has to dimension its cooling systems accordingly. The company will sometimes use a split design to overcome physical boundaries. Apart from that, the company’s experts develop decentralised cooling systems for entire charging centres with centralised cooling systems serving a number of charging stations.

E-mobility still a major growth market
E-mobility is set to form the heart of a resource-efficient urban infrastructure, especially in Europe. Many cities are investing in e-buses, so their share in public transport is increasing accordingly. The same applies to regional railways that need to cover long distances in contrast to trams. This reflects in an increased requirement for efficient cooling systems at Technotrans, which means increased technical challenges as virtually every project comes with its own peculiarities. As an example, the company develops cooling systems for automated guided vehicles (AGVs) to be used in harbours. These AGVs are not only subjected to extreme environmental conditions such as sea air and saltwater, but also heavy pressure and vibration from loaded freight, such as containers. The company integrated a cooling system for a series of fuel cells underneath the vehicle between the wheels, where it could be vulnerable to attack such as stone impact.
Apart from that, lightness and power density also played a major role. Scientists and companies are intensively researching ways towards continuously reducing vehicle weight. The aim is not only to make increasingly lighter batteries, but also to develop more advanced concepts such as plastic casings for electric motors. These developments also affect cooling systems that need to concentrate ever increasing power into more compact dimensions. EV and charging station manufacturers also demand systems that work with as little noise and vibration as possible, and Technotrans has gathered years of expertise to meet these challenges. After all, there will be no e-mobility without efficient cooling in the future either.