Hybrid and Electrical Vehicle Powertrain Testing

The Key to Reaping Efficiency Benefits By Randal Beattie, SAKOR Technologies Inc. Over the past decade, most transportation markets, from automotive, to military, aircraft, and even space systems have seen a tremendous surge of interest in hybrid and electric vehicle technology. To gain the promised efficiency benefits and green profile of these vehicles, it is important to conduct driveline and component testing during design and manufacturing that is specially adapted to the particular nature of hybrid and electric vehicles. Hybrid and electric drivetrains have several features that make testing them very different from the standard testing conducted on internal combustion (IC) only systems. Hybrid and electric systems use regenerative braking (where braking actually generates power that is returned to and stored in the vehicle’s battery for later use). This typically requires addition of fairly complex AC inverter technology, and often more complex transmissions. In addition, these vehicles often have several module control units (MCU’s), essentially small onboard computers, which control the functions of such major subsystems as the engine, transmission, and charging system, among others. To properly test these components, the test system needs to be able to communicate with one or more of these units via a high speed in-vehicle networks. This changing technology and increased complexity requires a testing system very different, and more complex, than those used in IC-only systems. The technology is out there to ensure proper testing and realization of the energy efficiency benefits promised by hybrid and electric vehicles. What’s more, the testing technology is itself energy efficient, reducing operations and maintenance costs and contributing to the vehicle’s overall environmental performance. Types of Hybrid/EV driveline testing Hybrid or electric driveline testing is conducted at several stages during the development of a vehicle, and each has an important role to play. Engineering testing – design engineers need precise measurements Accurate measurements are critical so design engineers can extract every bit of efficiency from their designs. Otherwise they will lose much of the advantage of using hybrid/electric technology. Most vehicles use 3-phase AC motors driven by inverter technology, so sophisticated power analyzers are needed to properly measure 3-phase AC power with a large amount of harmonic content. These test systems tend to be rather complex and are usually the most sophisticated, with many elements to be tested and coordinated. In-process and end-of-line testing – manufacturers verify performance and safety Manufacturing end-of-line testing is usually performed to verify that no defects were introduced in the manufacturing process, and that the components will perform to specifications. Typical tests include operational validation, quick performance testing, as well as rigorous testing to validate that high-voltage electrical systems are properly isolated, and are therefore safe to use in vehicles. In-process testing may also be conducted to test partial assemblies along the production line. This improves manufacturing efficiency and significantly reduces the chance that faulty components will find their way into the finished product. Quality control testing – motor users look for defects in incoming product Quality control (QC) testing is usually done on a percentage of the components to verify that that they perform over the specified range, and are relatively free of defects. For example, a fork lift company may conduct QC testing on a shipment of imported electric motors that are scheduled to be placed inside their forklifts. They would use QC testing to verify that the shipment coming from their supplier performs as specified and will not experience high failure rates in the field. This type of test system is typically less complex, because it does not have to measure as many items, nor to the degree of accuracy, as those tested in engineering systems. Regenerative braking is the basis of improvement in fuel economy Hybrid or electric vehicles use 4-quadrant motor/inverter technology to either assist the engine (hybrid) or as the prime mover (electric vehicle). Four quadrant means that the electric motor can control velocity or torque in either direction − the motor can accelerate, run, and decelerate forward or backward. During deceleration, the system uses regenerative braking, so the electric motor is used to slow the vehicle, and in the process becomes a generator, partially recapturing the energy of motion in the vehicle and restoring it to the battery. In hybrid systems, when stopping, slowing down, or idling, the engine is typically shut off and not burning fuel. At the same time, the electric motor again becomes a generator, partially recouping energy and storing it back in the battery. The engine is switched back on when needed to keep the vehicle moving, or to accelerate. During this time, the electric motor assists in accelerating the vehicle, using some of the recaptured electrical energy to reduce the load on the engine, and therefore reduce fuel consumption. Using this recaptured power is the reason we can go longer between fillups and/or charges, leading to the improvements in fuel economy we are seeking. It is essential that the testing program used in designing and manufacturing the vehicles ensure that the powertrain is running efficiently and making the best use of this regenerative power. Testing systems for hybrid or electric vehicles Testing hybrid and electric vehicles is worlds apart from traditional internal combustion engine testing, which typically measures speed, torque, and a few temperatures, pressures, and flows. Very precise control of speed and torque is typically not required in testing internal combustion engines, so dynamometers used for standard combustion engine testing (for example, water brake and eddy current) were never designed to handle the types of precision required by hybrid or electric powertrains, nor can they test the regenerative (motoring) modes of operation. Modern hybrid/EV test systems must provide all of the functionality of traditional systems, with the added ability to test high-power regenerative electrical drives, high voltage battery and charging systems, and communicating with any number of smart control modules (MCU’s). Electrical system testing For many larger hybrid/electric drivetrains, there is a strong trend toward using higher voltage, higher efficiency drive systems. Going from the traditional 12/24-volt DC
Minimal Resistance
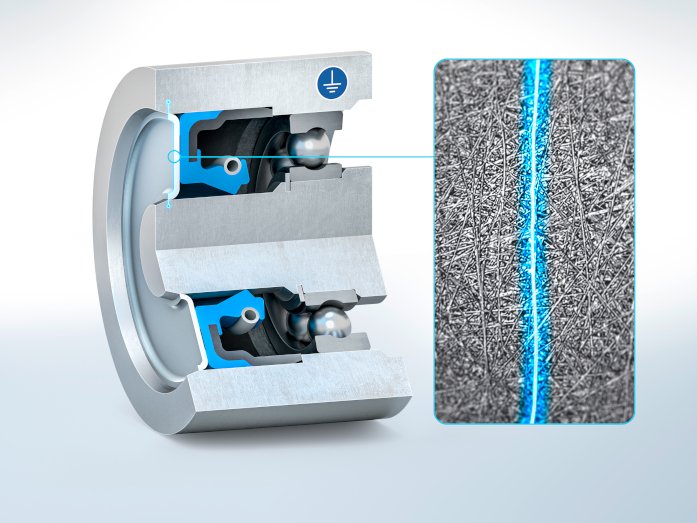
Conductive Seals Promote High Power Density in Electric Powertrains Weinheim (Germany), September 19, 2019. Freudenberg Sealing Technologies is developing a new generation of conductive seals designed to ensure a durable electrical connection between housings and shafts while preventing bearing damage caused by electricity and electromagnetic radiation. In many operating conditions, the shafts used in electric powertrains are electrically insulated from their housings. The insulation is created by the lubricating films in the contact zones for the bearing and the shaft seals. Lubrication is necessary to promote long-term system functionality. Alternating current and its electromagnetic fields produce changes in the electric potential between the rotor and the stator and the rotor becomes charged. The current can only be drained off through a grounded system that allows the electricity to travel from the shaft to the housing. If there is no grounded pathway, the current flows to the area of least resistance – the bearing – and produces an abrupt discharge when electricity flows from the inner ring to the outer ring across the bearing. Discharge flashes cause surface burns and material compromises that permanently damage the system. The result: The contact surfaces in the rolling bearing are steadily and systematically destroyed. The mounting becomes noisy and the bearing must be replaced to prevent powertrain failure. Damage from electric current must absolutely be avoided. The simple solution is to develop a lasting, reliable electrical contact between the shaft and the housing that facilitates a continuous flow of electricity and prevents excessive build up and sudden discharges. The more difficult challenge is to find a system element that can conduct the current via ongoing contact with both the housing and the shaft. As a rule, seals are made of insulating materials and are not suited for this purpose. For several years, Freudenberg Sealing Technologies has been producing an electrically-conductive nonwoven disk as a series- production system element. The advantage: It is firmly connected to the shaft seal ring and requires almost no additional installation space. The conductivity of the nonwoven is achieved with special fibers that are embedded in a matrix. The system has been used in regular-production electric vehicles for years and reliably prevents bearing damage. The electric resistance in this approach is already at a very low level, but the sealing specialists at Freudenberg Sealing Technologies continue to develop the solution further. Power densities continue to grow in upcoming electric powertrains, increasing current, voltage and disruptive electromagnetic fields. To offer a robust solution for these situations, the company is now developing a new generation of conductive seals. The first validated, functional models in this category will be available within a few months. “Our goal is to achieve constant resistance values over a long period of operation – even in adverse conditions,” said Dr. Tim Leichner, who is responsible for Strategic Product Advance Development at Freudenberg Sealing Technologies. To fulfill the new requirements for seals in electric powertrains, Freudenberg Sealing Technologies has developed the appropriate test procedure to evaluate and compare the functioning of current dissipation elements. Test stand trials have shown that static measurements of the elements’ electrical resistance are not adequate to predict electrical conductivity during actual dynamic use. So development engineers in Germany developed a dynamic testing procedure that delivers alternating-current flows in the frequencies found in automobiles. “There is the possibility of doing even more with conductive seals,” said Francois Colineau, who is in charge of the development of this product line at Freudenberg Sealing Technologies. “High electrical conductivity lends itself to possible shielding of disruptive electromagnetic radiation.” The exit point of the shaft from the housing, in particular, is normally a location where “impermeability” is only achieved with difficulty. At this location on every electric motor, there is a shaft seal that could help handle the shielding. It would be possible to combine the sealing of oil and other media with impermeability to electromagnetic radiation – without necessarily adding another nonwoven layer. “Perhaps we will even find an entirely new electrically conductive sealing material. We’re working on it,” Colineau said.