GKN Automotive launches strategy to make electric propulsion more affordable
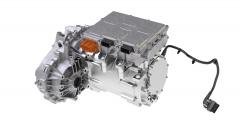
Standardised electric drive systems with highly integrated inverters and motors aim to make electrification affordable for automakers and consumers Three new families of modular, scalable eDrive systems will provide affordable electrification options in all torque classes Full details in GKN Automotive’s newly released technology strategy report, Making Electric Propulsion More Competitive: https://www.gknautomotive.com/en/whitepapers/electric-propulsion London, UK, 11 December 2019: GKN Automotive has today launched the next phase in its electrification strategy. The leading supplier of all-wheel drive and electric driveline technology and systems is standardising a range of intelligent highly integrated “3-in-1” systems for pure electric and plug-in hybrid vehicles, in a move to decrease cost and increase efficiency. The 3-in-1 systems effectively integrate an electric motor, inverter together with the single-speed transmission module that scales up the torque. The inverter retains its own separate housing for maximum serviceability. The company’s Automotive SPICE® Level 2- and 3-certified software engineering processes enable it to manage the system’s complete integration. GKN Automotive’s intelligent standardisation strategy enables three families of electric drive to cover all mass-market torque requirements. The systems distil the company’s substantial experience in industrialising electric axle and driveline systems, and harnesses data and system integration knowledge accumulated from 17 years of eDrive development and production of over a million eDrive units. Hannes Prenn, COO of GKN Automotive ePowertrain, said: “GKN Automotive is the world’s leading supplier of P4 electric drive systems. This next phase of our electrification strategy will produce the highly integrated, modular, scalable architectures required for high volume vehicle applications. Standardising these systems will make electrification more affordable and will enable OEMs to offer consumers highly optimised e-mobility at the right price.” GKN Automotive’s Family 2 eDrive system is already production-proven with a number of premium automotive brands. It provides peak torque of 1,800 – 2,700 Nm and is suitable for A-, B- and C-segment applications. The Family 3 eDrive system covers C- and D-segment applications with peak axle torque of 2,700 – 4,100 Nm. The Family 4 eDrive system provides 4,100 – 5,800Nm for D-segment and large vehicle applications. Intelligent standardisation of the company’s own electric motor and inverter modules will further reduce system costs. Industry forecasts indicate that by 2026, one in every 10 vehicles sold worldwide will be a battery electric vehicle. The high efficiency of “P4” electric axle drive architectures will make them central to most pure electric and plug-in hybrid strategies. To provide the best balance of cost and performance, single-speed systems are expected to account for 94% of P4 eDrive volumes. P4 electric drive architectures connect the motor directly to the vehicle’s axle, making it more efficient and cost-effective than “P2” and “P3” systems that hybridise the main transmission. P4 systems send torque directly to the wheels and recover energy directly from the wheel when braking. P4 electric drive systems integrate the inverter and electric motor into a compact transmission module that applies torque to the axle. GKN Automotive has become one of the industry’s most trusted and experienced tier one suppliers of P4 electric drive systems. The company was the first to market with eAxle technology in 2002, and, in 2019, was the first to produce one million units. It has served as a tier one system integrator on programs for Fiat Chrysler Automobiles, Jaguar Land Rover, BMW Group, Volvo Cars, PSA Peugeot Citroen and Geely. Full details of GKN Automotive’s EV and PHEV technology strategy are available in a newly released report, Making Electric Propulsion More Competitive, available from:https://www.gknautomotive.com/en/whitepapers/electric-propulsion ENDS ABOUT GKN AUTOMOTIVE GKN Automotive is the world’s leading supplier of automotive driveline technology and components. As a global company serving more than 90% of the world’s vehicle manufacturers, it operates through 53 locations in 27 countries, employing over 29,000 people. GKN Automotive develops, builds and supplies an extensive range of automotive driveline technologies – for use in the smallest ultra-low cost cars to the most sophisticated premium vehicles showcasing advanced driving dynamics. GKN Automotive’s driveline technologies – including constant velocity joint, sideshaft and propshaft systems – have already featured on more than nine billion vehicles around the world. Its proven software development and vehicle integration expertise, and a complete range of scalable solutions, also make GKN Automotive the industry’s number one partner for AWD, transaxle and eDrive systems. Its rapidly growing eDrive activities employ 5,000 people across eight manufacturing and R&D sites in six countries, and have delivered more than 1,000,000 eDrive units to date. GKN in Formula E In 2017, GKN agreed a multi-year partnership with Panasonic Jaguar Racing, which will see it provide design, manufacturing and consultancy services to the Formula E team. Experts from both GKN Automotive provide technical consultancy and new technology, from driveshafts and differentials to the use of additive manufacturing, for the Jaguar I-TYPE. GKN’s considerable experience in delivering state-of-the-art electric vehicle systems means it will also advise on the development of the I-TYPE’s all-electric powertrain.
Minimal Resistance
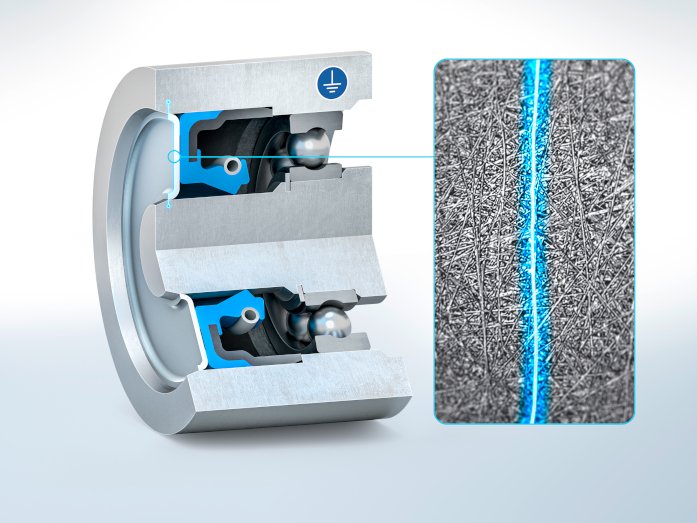
Conductive Seals Promote High Power Density in Electric Powertrains Weinheim (Germany), September 19, 2019. Freudenberg Sealing Technologies is developing a new generation of conductive seals designed to ensure a durable electrical connection between housings and shafts while preventing bearing damage caused by electricity and electromagnetic radiation. In many operating conditions, the shafts used in electric powertrains are electrically insulated from their housings. The insulation is created by the lubricating films in the contact zones for the bearing and the shaft seals. Lubrication is necessary to promote long-term system functionality. Alternating current and its electromagnetic fields produce changes in the electric potential between the rotor and the stator and the rotor becomes charged. The current can only be drained off through a grounded system that allows the electricity to travel from the shaft to the housing. If there is no grounded pathway, the current flows to the area of least resistance – the bearing – and produces an abrupt discharge when electricity flows from the inner ring to the outer ring across the bearing. Discharge flashes cause surface burns and material compromises that permanently damage the system. The result: The contact surfaces in the rolling bearing are steadily and systematically destroyed. The mounting becomes noisy and the bearing must be replaced to prevent powertrain failure. Damage from electric current must absolutely be avoided. The simple solution is to develop a lasting, reliable electrical contact between the shaft and the housing that facilitates a continuous flow of electricity and prevents excessive build up and sudden discharges. The more difficult challenge is to find a system element that can conduct the current via ongoing contact with both the housing and the shaft. As a rule, seals are made of insulating materials and are not suited for this purpose. For several years, Freudenberg Sealing Technologies has been producing an electrically-conductive nonwoven disk as a series- production system element. The advantage: It is firmly connected to the shaft seal ring and requires almost no additional installation space. The conductivity of the nonwoven is achieved with special fibers that are embedded in a matrix. The system has been used in regular-production electric vehicles for years and reliably prevents bearing damage. The electric resistance in this approach is already at a very low level, but the sealing specialists at Freudenberg Sealing Technologies continue to develop the solution further. Power densities continue to grow in upcoming electric powertrains, increasing current, voltage and disruptive electromagnetic fields. To offer a robust solution for these situations, the company is now developing a new generation of conductive seals. The first validated, functional models in this category will be available within a few months. “Our goal is to achieve constant resistance values over a long period of operation – even in adverse conditions,” said Dr. Tim Leichner, who is responsible for Strategic Product Advance Development at Freudenberg Sealing Technologies. To fulfill the new requirements for seals in electric powertrains, Freudenberg Sealing Technologies has developed the appropriate test procedure to evaluate and compare the functioning of current dissipation elements. Test stand trials have shown that static measurements of the elements’ electrical resistance are not adequate to predict electrical conductivity during actual dynamic use. So development engineers in Germany developed a dynamic testing procedure that delivers alternating-current flows in the frequencies found in automobiles. “There is the possibility of doing even more with conductive seals,” said Francois Colineau, who is in charge of the development of this product line at Freudenberg Sealing Technologies. “High electrical conductivity lends itself to possible shielding of disruptive electromagnetic radiation.” The exit point of the shaft from the housing, in particular, is normally a location where “impermeability” is only achieved with difficulty. At this location on every electric motor, there is a shaft seal that could help handle the shielding. It would be possible to combine the sealing of oil and other media with impermeability to electromagnetic radiation – without necessarily adding another nonwoven layer. “Perhaps we will even find an entirely new electrically conductive sealing material. We’re working on it,” Colineau said.