The benefits of independent wheel torque control in non-performance applications
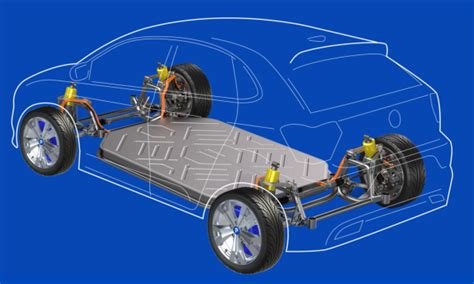
In-wheel motors can be used to deliver the ‘torque vectoring’ strategies present in many high performance vehicles. In this article we discuss many other potential areas where independent wheel torque can improve the value proposition of non-performance market segments Dr Richard Ford, Vehicle Engineering and Controls Manager, Protean Electric Introduction Torque vectoring, or perhaps more accurately termed, torque biasing, is becoming more common on high performance vehicles as a way to deliver improved cornering performance. This is achieved by adding yaw moment onto the vehicle via active differential, brakes or other mechanical solutions. The flexibility of independent wheel torque control via in-wheel motors means that standard torque vectoring strategies are simple to implement using software only. However the benefits of true high bandwidth independent wheel torque control go far beyond simple torque vectoring and can bring efficiency, safety, dynamics, cost and time-to-market benefits to all market segments. In order to achieve maximum benefit the platform concept and design process must be optimised to make best use of the unique characteristics of in-wheel motors. Efficiency benefits Traditional vehicles and electric vehicles powered by conventional eAxles incur rolling losses as a result of inefficient suspension and steering kinematics. Traditional vehicles are setup with a slight toe in on each of the four wheels to provide driving stability (the wheels are not parallel but instead are slightly ‘pigeon toed’); this approach increases wear on tyres and incurs energy losses. For 100km travelled, each tyre can be dragged the equivalent of up to 500m in the lateral direction. In contrast, a vehicle driven by IWMs can be configured for minimum rolling resistance with stability delivered by the high bandwidth individual wheel torque dynamics. Vehicle manufacturers have opted for a trail and caster set-up on their vehicles to deliver desired handling characteristics. These characteristics have become ingrained in many steering system designs as manufacturers chase the driving feel that will differentiate them from the other brands. Unfortunately, while this set-up delivers good steering feel, increasing mechanical trail also leads to increased losses in the power steering system as steering loads are increased. Removing these mechanical characteristics and replacing them with software controlled systems can reduce some of these steering system inefficiencies. Safety benefits In-wheel motors provide greater control of vehicle dynamics – especially with a motor at each wheel. Reduced stopping distances, better obstacle avoidance, the ability to run on low-friction surfaces, and bi-directionality all bring a host of safety advantages. Stopping distances on vehicles with IWMs can be significantly reduced through torque modulation, while the performance of an ABS system on a conventional vehicle is limited by the response of the hydraulic actuators and speed sensors. The speed sensing requirements of an in-wheel motor and the speed of response of the torque delivery (only the tyre dynamics remain) naturally lead to a significantly improved slip control potential. To recover the full potential on varying grip surfaces, coordination with the steering system is required, and this is achievable thanks to the highly deterministic nature of the torque delivery from an IWM. A car’s tendency to understeer, allowing the driver to safely manage the car at the limit of grip, is an important consideration for vehicle manufacturers and providers. But this comes at the cost of the front suspension set-up on a standard passenger car, which is often detuned to deliver the ideal characteristics – the front wheels meeting the limit of grip before the rear wheels. in-wheel motors fulfil requirements from manufacturers eager to meet the demands and needs of changing vehicle ownership and usage models. If we use the in-wheel motors to give the desired understeer characteristics then there is no need to detune the suspension. Thus the vehicle naturally has improved ultimate grip in critical situations. In modern steering systems there is a high degree of electronic control, and this is set to increase as the mechanical link from wheels to driver is phased out. The safety implications of this are very challenging and manufacturers are working hard to find acceptable solutions. At a vehicle level, one potential option is to have completely separate systems on the vehicle that can deliver yaw moment on the car to direct the car safely to the side of the road in the event of loss of primary steering control. This is entirely within the scope of an in-wheel motor equipped vehicle and means that the level of design effort and validation on the primary steering system is more manageable. The same redundant functionality is also naturally available for the braking system, where a high level of retardation is available from the IWM. Driving dynamics benefits Even at low speeds, the driving feel of a vehicle can be significantly changed and enhanced using independent torque control. Steering is more responsive both in transient steering movements, like lane changes, and in steady state cornering. Since this behaviour is entirely software controlled, the agility of a vehicle can be enhanced at low speed, while sensitivity reduced (hence the feel of stability improved) at higher speeds. In a similar way to the suspension design, this capability removes one of the traditional trade-offs faced when designing a steering system and allows further improvements to the vehicle’s appeal, via reduced cost or enhanced functionality. Vehicle time to market benefits Since a number of the suspension/steering characteristics can now be achieved via software control of the IWM, there is potential to simplify the mechanical design of these systems, reducing the cost of these subsystems and leading to increased commonality between vehicle platforms. Increased reusability of these subsystems will give cost and time-to-market benefits. This may well lead to ‘skateboard’ chassis being applied to numerous quite different vehicles with very different exterior designs and interior layouts that share compact corner modules. Further time-savings are realised due to reduced need to tune the chassis hardware for each specific application. Moving vehicle functions from hardware to software not only delivers enhanced functionality, but each iteration is quicker and the whole process is more suited to
GKN Automotive launches strategy to make electric propulsion more affordable
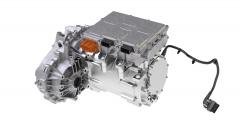
Standardised electric drive systems with highly integrated inverters and motors aim to make electrification affordable for automakers and consumers Three new families of modular, scalable eDrive systems will provide affordable electrification options in all torque classes Full details in GKN Automotive’s newly released technology strategy report, Making Electric Propulsion More Competitive: https://www.gknautomotive.com/en/whitepapers/electric-propulsion London, UK, 11 December 2019: GKN Automotive has today launched the next phase in its electrification strategy. The leading supplier of all-wheel drive and electric driveline technology and systems is standardising a range of intelligent highly integrated “3-in-1” systems for pure electric and plug-in hybrid vehicles, in a move to decrease cost and increase efficiency. The 3-in-1 systems effectively integrate an electric motor, inverter together with the single-speed transmission module that scales up the torque. The inverter retains its own separate housing for maximum serviceability. The company’s Automotive SPICE® Level 2- and 3-certified software engineering processes enable it to manage the system’s complete integration. GKN Automotive’s intelligent standardisation strategy enables three families of electric drive to cover all mass-market torque requirements. The systems distil the company’s substantial experience in industrialising electric axle and driveline systems, and harnesses data and system integration knowledge accumulated from 17 years of eDrive development and production of over a million eDrive units. Hannes Prenn, COO of GKN Automotive ePowertrain, said: “GKN Automotive is the world’s leading supplier of P4 electric drive systems. This next phase of our electrification strategy will produce the highly integrated, modular, scalable architectures required for high volume vehicle applications. Standardising these systems will make electrification more affordable and will enable OEMs to offer consumers highly optimised e-mobility at the right price.” GKN Automotive’s Family 2 eDrive system is already production-proven with a number of premium automotive brands. It provides peak torque of 1,800 – 2,700 Nm and is suitable for A-, B- and C-segment applications. The Family 3 eDrive system covers C- and D-segment applications with peak axle torque of 2,700 – 4,100 Nm. The Family 4 eDrive system provides 4,100 – 5,800Nm for D-segment and large vehicle applications. Intelligent standardisation of the company’s own electric motor and inverter modules will further reduce system costs. Industry forecasts indicate that by 2026, one in every 10 vehicles sold worldwide will be a battery electric vehicle. The high efficiency of “P4” electric axle drive architectures will make them central to most pure electric and plug-in hybrid strategies. To provide the best balance of cost and performance, single-speed systems are expected to account for 94% of P4 eDrive volumes. P4 electric drive architectures connect the motor directly to the vehicle’s axle, making it more efficient and cost-effective than “P2” and “P3” systems that hybridise the main transmission. P4 systems send torque directly to the wheels and recover energy directly from the wheel when braking. P4 electric drive systems integrate the inverter and electric motor into a compact transmission module that applies torque to the axle. GKN Automotive has become one of the industry’s most trusted and experienced tier one suppliers of P4 electric drive systems. The company was the first to market with eAxle technology in 2002, and, in 2019, was the first to produce one million units. It has served as a tier one system integrator on programs for Fiat Chrysler Automobiles, Jaguar Land Rover, BMW Group, Volvo Cars, PSA Peugeot Citroen and Geely. Full details of GKN Automotive’s EV and PHEV technology strategy are available in a newly released report, Making Electric Propulsion More Competitive, available from:https://www.gknautomotive.com/en/whitepapers/electric-propulsion ENDS ABOUT GKN AUTOMOTIVE GKN Automotive is the world’s leading supplier of automotive driveline technology and components. As a global company serving more than 90% of the world’s vehicle manufacturers, it operates through 53 locations in 27 countries, employing over 29,000 people. GKN Automotive develops, builds and supplies an extensive range of automotive driveline technologies – for use in the smallest ultra-low cost cars to the most sophisticated premium vehicles showcasing advanced driving dynamics. GKN Automotive’s driveline technologies – including constant velocity joint, sideshaft and propshaft systems – have already featured on more than nine billion vehicles around the world. Its proven software development and vehicle integration expertise, and a complete range of scalable solutions, also make GKN Automotive the industry’s number one partner for AWD, transaxle and eDrive systems. Its rapidly growing eDrive activities employ 5,000 people across eight manufacturing and R&D sites in six countries, and have delivered more than 1,000,000 eDrive units to date. GKN in Formula E In 2017, GKN agreed a multi-year partnership with Panasonic Jaguar Racing, which will see it provide design, manufacturing and consultancy services to the Formula E team. Experts from both GKN Automotive provide technical consultancy and new technology, from driveshafts and differentials to the use of additive manufacturing, for the Jaguar I-TYPE. GKN’s considerable experience in delivering state-of-the-art electric vehicle systems means it will also advise on the development of the I-TYPE’s all-electric powertrain.
After more than a century, in-wheel technology is ready to help transform mobility as we know it

For more than a hundred years, the internal combustion engine (ICE) – in all its shapes and forms – has been propelling us across land, sea and air. Now, its long-term future appears bleak given the ever-growing concerns of fossil fuels affecting the environment, more so given their supply is finite. Enter e-Mobility – a simple term until you scratch the surface deep enough to reveal a multitude of new or different technologies that all need to come together to keep future generations on the move. The playing field of the automotive industry has significantly changed with the arrival of electric vehicles in the mainstream market. Today, electric vehicle design and production is not limited to only traditional players, but has become an open playing field. There is a vast number of competing powertrain architectures and technologies, some being simple adaptations of the traditional 100-year-old ICE concept, and others more advanced, which bring more radical changes to the vehicle as we know it. Since a lot of different technologies are possible and the development of mass-production compatible electric powertrains is practically in its infancy, vehicle makers are scrambling to find the right formula for the future user. Currently, electric vehicles are competing on acceleration performance and range. In the future, the discussion will be less about cars and more about mobility. Vehicle makers will bring cars to the streets that are connected, have autonomous driving capabilities, and are made to be shared between multiple users. Needless to say, these vehicles will mostly be built on electrified platforms. As battery technology, cost, and production capacity improve, the priorities for the powertrain are shifting. Some of the traditionally most important development drivers will become less important. As an example, one could postulate that the electric powertrain reached a level of efficiency where additional investments will bring only limited overall benefit compared to other possible improvements. And since some electric city cars currently exceed the performance of many ICE sports cars, there is not much need for performance improvement either. This thinking translates into the conclusion that the mechanical actuation of the next generation of vehicles will be much less in the spotlight, while function, safety and comfort, along with a high-level of autonomy and connectivity will become main drivers for vehicle design. E-Mobility activists and electric vehicle technology companies like Elaphe Propulsion Technologies, are creating innovative solutions for designers of current and future vehicles. They lend a much-needed helping hand to EV developers to meet passenger comfort, safety and road security objectives: advancing state of the art on batteries, fuel-cells, motors, drive trains (or lack of drive trains), electro-mechanical control, on-board electronics, sensors, mechanics, thermal- and power management, all packaged in lightweight but durable, minimal maintenance structures. For example, in-wheel electric propulsion can eliminate the entire conventional drivetrain, drastically simplifying and shortening the whole vehicle engineering process from concept to series production. Transmissions, gearboxes, drive shafts, and the associated space constraints are now becoming obsolete. Figure 1 – An in-wheel motor has only a single rotating part – the wheel bearing. The assembly fits in existing design space within the wheel, and is built around the (still, for now) required friction brake, making all the transmission and gearing found in traditional cars, unnecessary. Although the idea of an in-wheel motor platform was already proposed by Ferdinand Porsche at the turn of the 19th century, the underlying technology and the whole ecosystem at that time was in its infancy. A development of in-wheel propulsion over the past two decades has brought the technology to a mature, production-ready state where it now enables a fundamental shift in design for mobility. In-wheel motor platforms now have the potential to reshape the EV industry and support the shift away from performance focus, making way for innovation in packaging, user-experience, driving automation, new safety features, and optimization of the electric vehicle supply chain. The in-wheel concept plays a significant role in the development of compact, transmission-free drive systems. Increased safety, improved handling and unparalleled traction control are just some of the benefits of the decentralized in-wheel architecture. Having a lower overall powertrain weight, a lower center of gravity and optimized balance, the dynamic behavior of the vehicle changes dramatically. The drive architecture, with its weight distribution and contact pressure at precisely the point of traction, allows greater control over the vehicle’s behavior in comparison to standard drives. More so when we consider the possibilities for integration of advanced systems, such as: i) brake blending, which can greatly improve safety on different-adhesion surfaces, ii) active traction control that is constantly optimizing the grip between the wheel and the road and iii) torque vectoring, improving vehicle stability and keeping control over the vehicle’s dynamic behavior in unstable, critical situations, just to name a few. From early innovations to becoming an essential part of the future advances of electrified vehicles. In the late 1980s Elaphe’s co-founder imagined his ultimate powertrain concept by drawing inspiration from nature, in particular, the anatomy and mechanical energy generation of animals. He had good technical reasons to believe his research could be applied to cars and other vehicles in the future. The availability of more robust, new materials not available in the past and the advent of computer simulation methods, combined with a strong belief in the need for a simple, clean and highly efficient powertrain architecture with very few moving parts, drove further innovations. Most importantly, the envisioned potential to change how a vehicle looks like, how it is used and how to lower its environmental impact, spurred Elaphe’s commitment to technological innovation. The initial designs proved the conceptual feasibility, so the team set up a company to support the development of this great technology for the benefit of our green planet. Challenges along the way included how to deal with the influence of temperature and temperature variation. People rarely realize the effort that goes into designing a car component that works in conditions from -40°C to +85°C. Figure 2 – Housed entirely