Safety for Electric Cars
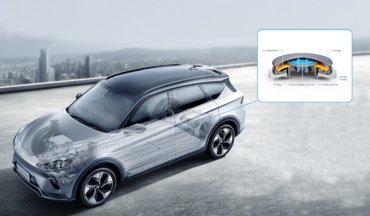
Freudenberg Sealing Technologies starts series production of DIAvent pressure equalization element for Chinese passenger cars Weinheim (Germany), November 24, 2020: The innovative DIAvent pressure compensation element from Freudenberg Sealing Technologies provides pressure equalization in batteries for electric cars both during normal driving and for emergency venting in the event of damage or accidents. It is therefore an important safety feature for battery-powered vehicles. Freudenberg Sealing Technologies is now starting high-volume production of the component for the first time for use in a Chinese passenger car: DIAvent will help to ensure battery safety in the new ARCFOX α-T electric car from the Chinese manufacturer Beijing Electric Vehicles (BJEV). In 2017, Freudenberg Sealing Technologies introduced its innovative pressure compensation element DIAvent to the public: In batteries for electric vehicles, a valve consisting of two nonwovens with different properties takes over pressure equalization during normal operation. Excess pressure reduction during emergency degassing is handled by a reversible umbrella valve. As simple as it sounds, the solution is very technically sophisticated. While only a few liters of air per minute are exchanged in both directions during normal operation, in an emergency the entire quantity of gas emitted from a defective cell must be removed in a few seconds. Otherwise, the strong internal pressure – many times higher than the ambient pressure – could cause the housing to burst.The trend towards battery systems with even higher energy density is another challenge. This is because it also increases the amount of gas that has to be quickly removed in case of an emergency, as well as the amount of air exchanged during normal operations. Freudenberg’s patented DIAvent valve replaces typically used microporous film like PTFE with a combination of two nonwovens with different properties. The water-repellent nonwoven fabric on the outside allows air exchange of approximately eight liters per minute at a low pressure difference. And it is watertight up to 100 millimeters of water column. If the water pressure rises above this, a second inner layer of nonwovens is activated so that no water can enter the housing. Degassing in an emergency is made possible by a umbrella valve that is arranged in a ring around the nonwoven fabric. It opens reliably as soon as the pressure in the housing exceeds the atmospheric air pressure by more than 50 millibars, and can then discharge 40 liters of gas per second. A major advantage of the DIAvent: the umbrella valve closes again at the end, making it easier to safely remove a damaged battery after emergency degassing. Since it reversibly opens and closes, it can also support pressure equalization in normal operation, for example when batteries with very high energy density are exposed to rapid temperature fluctuations.Another advantage of DIAvent is that it takes over the functions that are usually performed by two separate components – a breathing element and a bursting disc. This means it is more economical and easier to install for vehicle manufacturers, since only one component has to be installed.Right after prototype production, several vehicle manufacturers expressed their interest and tested the pressure compensation element from Freudenberg Sealing Technologies. At the beginning of 2020, DIAvent went into series production for European customers for the first time. Two years ago, Freudenberg’s sealing experts launched a joint development and test project with the Chinese manufacturer BJEV, which was successfully concluded with an agreement for series production in 2020.“The cooperation with BJEV was very intensive. We are very proud that our engineering expertise helps our customer to continue its road to success.” explained Liu Zehua, Account Manager and Sales Representative at NOK-Freudenberg. “With this project, Freudenberg truly demonstrated its global footprint: The company managed a complex global customer project with local sales in China, and engineering and production in Europe.” BJEV, which has been operating successfully in the Chinese automotive market for about 30 years, now wants to establish a stronghold in the European market as well. That is why cooperation with established local suppliers was very important to the company, especially in view of the strict European safety standards for passenger cars. “We are delighted that DIAvent is now going into series production for the first time at a Chinese OEM,” says Matt Chapman, President, Automotive Sales & Marketing at Freudenberg Sealing Technologies. “The high demand for this product shows us that we know the needs of our automotive customers very well and that we are using our expertise precisely for innovations to support our customers in the difficult transition to electric mobility. And in doing so, we are also pointing the way to emission-free mobility in general.”Freudenberg Sealing Technologies also works with other OEMs on development projects for the DIAvent and expects further series orders by the end of this year. About Freudenberg Sealing TechnologiesFreudenberg Sealing Technologies is a longstanding technology expert and market leader for sophisticated and novel applications in sealing technology and electric mobility solutions worldwide. With its unique materials and technology expertise, the company is a proven supplier for demanding products and applications, as well as a development and service partner to customers in the automotive industries and in general industries. In 2019, Freudenberg Sealing Technologies generated sales of about €2.2 billion and employed approximately 14,000 people. More information at www.fst.com The company is part of the global Freudenberg Group which has four business areas: Seals and Vibration Control Technology, Nonwovens and Filtration, Household Products as well as Specialties and Others. In 2019, the Group generated sales of approximately 9.5 billion and employed more than 50,000 associates in around 60 countries. More information is available at www.freudenberg.com. Media ContactFreudenberg Sealing TechnologiesUlrike Reich, Head of Media RelationsOffice: +49 (0)6201 80 5713Email: ulrike.reich@fst.com ulrike.reich@fst.com / www.fst.com / www.youtube.com/FreudenbergSealing
A supplier on his way to a new mobility era

Freudenberg Sealing Technologies is using the transformation in the automotive industry to technologically and structurally advance the company Fundamental technological change in the automotive industry also requires suppliers to have the courage to make far-reaching changes. If they don’t have the courage to do so, they will not succeed in the long term. Freudenberg Sealing Technologies, one of the world’s leading suppliers of sealing solutions for the automotive industry, is using this disruptive upheaval as an opportunity. Strategic initiatives, technological partnerships, targeted investments and innovative developments point the way into the automotive future. “The question is not when new drive technologies will burden our own product portfolio, but to what degree,” says Claus Möhlenkamp, CEO of Freudenberg Sealing Technologies. “This is why we want to take advantage of opportunities early on and align ourselves accordingly.” So far, Freudenberg Sealing Technologies generates almost 70 percent of its sales in the automotive industry with solutions for internal combustion engines. All the company’s products installed in a passenger car would have a total value of around 70 euros. In view of global car production of almost 85 million cars at present, this represents a market potential of almost six billion euros. The downside of this calculation: 45 of the 70 euros are currently accounted for by the combustion engine, the transmission and the fuel system. This is currently benefiting the company: due to stricter CO2 regulations, all manufacturers are revising their combustion engines to reduce energy consumption and emissions. “This is where we help our customers with our LESS (Low Emission Sealing Solutions) products, which reduce friction, emissions, installation space and weight,” says Möhlenkamp. The best known example of this is Levitex, the almost completely friction-free crankshaft seal that will soon be installed in series production at one of the world’s largest automobile manufacturers. However, without far-reaching changes in the product portfolio, the strong dependence on internal combustion engine drives would have a negative impact in the long term. “With our current portfolio, we would only be able to sell components worth around 25 euros per vehicle in a fully electric vehicle,” explains Möhlenkamp. “In other words: Two thirds of our sales are subject to risk.” In the meanwhile, many manufacturers are investing heavily in electric cars: the Volkswagen Group plans to launch more than 80 new electric models by 2025, including around 50 purely battery-operated vehicles. In the middle of the coming decade, electric cars are expected to have a share of a quarter of total production. Daimler is investing ten billion euros in electric mobility, which includes vehicle development, converted production plants and a complete ecosystem for customers. Toyota, previously known primarily for hybrid vehicles, plans to launch ten purely battery-powered electric vehicles by the beginning of the next decade. By 2030, half of all passenger cars and light commercial vehicles produced will be equipped with an electrified drive system. So, the electric car is on its way to the mass market. “We see the change in drive technology as an opportunity to further develop, strengthen and realign our company,” explains Möhlenkamp. The company is relying on three success factors to achieve this: Battery-powered electric drives and the fuel cell are the future of mobility. Assuming a complete conversion of traffic to non-fossil energy sources, the energy chain always starts with electricity from renewable sources, above all solar and wind energy. If this electricity can be used directly in the vehicle via suitable storage devices, the battery-powered electric drive has the best overall efficiency. With the current state of technology, storage densities and charging times are not sufficient to convert all passenger and freight traffic to electric vehicles. For long distances in particular, an alternative in the form of chemically bound energy is needed. The combination of hydrogen and fuel cells offers the best overall efficiency in the non-fossil supply of such an energy carrier. The company’s many years of expertise in materials and products are being transferred to the new world of mobility, the new expertise necessary is being developed. Freudenberg Sealing Technologies core competencies in sealing and materials technology are also needed in the new world of mobility. For example, an 800-volt battery that stores energy for 500 kilometers and is located in the underbody of a vehicle is exposed to strong vibrations and splashing water and must be sealed very well. “We are developing new expertise in battery and fuel cell technology, both through our own research and development and through targeted strategic acquisitions,” says Möhlenkamp. At the beginning of 2019, Freudenberg Sealing Technologies acquired a majority interest in the US company XALT Energy. Based in Midland, Michigan, the company produces large-format lithium-ion battery cells, modules and systems for use in heavy commercial vehicles, city and transit buses, the marine industry and other industrial applications. “With the increasing trend towards lithium-ion battery and fuel cell powertrains, this investment will enable us to provide our customers with the right materials, products and system solutions to meet new and complex technical challenges. We are very proud of this strategic decision,” explains Möhlenkamp. The transformation of the company is being supported by organizational changes In order to give the new business segments in battery technology and fuel cells sufficient scope, these activities were already concentrated in a new division in early 2018, solely dedicated to battery and fuel cell business. The company intends to use this opportunity to gain the long-term breath needed to develop new business areas. This strategy is working and showing first results: Since the beginning of the transformation, the company has developed a number of innovative new products for the electrified powertrain, such as the DIAvent pressure compensation element for traction batteries, to build electric vehicles more safely and more economically, or gas diffusion layers and gaskets for fuel cells, flat gaskets and two-component plug & seals. In electric vehicles, they reduce the weight of the system and enable complex sealing geometries as well as a chemical combination of the hard and soft materials of the