Silicone! Taking the Heat off of Battery Engineers and H&EV Manufacturers
Thermal Management is a term identified as the ability to control the entire temperature system of a battery array. Design engineers must consider insulation, heat and power transfer, conduction and convection, in order to maintain the battery pack temperature within a tight tolerance to prevent thermal runaway.
While temperature, a primary indicator of battery energy level, is the main variable when analyzing the state of the Thermal Management System (TMS), each system has a given ability to store or dissipate energy. This ability is referred to as its heat capacity and can be calculated by measuring the mass and the specific heat capacity of all materials in the system. Heat capacity is the connection between energy and temperature.

When energy is transferred into the system or energy is created by an internal source, the energy level of the system can rise. Higher energy levels of the materials in the system cause the temperature of these materials to rise. The specific heat capacity defines the connection between absorbed or dissolved energy and the change of temperature.
Material versatility can support holistic design thinking, performance and productivity
Thermal management of batteries in H&EVs is essential for the effective operation of motors in all climates and environments and is the main focus in the design of battery modules and packs for pre-production prototypes or serial production. Design thinking and technologies are constantly evolving to address these various issues. Design and material engineers are addressing the trade-offs between performance, functionality, volume, mass, cost, maintenance, and safety issues.
Thermal and materials management challenges for batteries in H&EVs include:
- Maintaining temperatures within an optimal range, with very few variations
- Reducing weight and volume
- Aligning power sources in efficient arrays that can be easily recharged and/or changed
- Ensuring safety and reliability
- Facilitating ease of processing
Elkem’s silicones can simplify complexity and create optionality
Thermal performance and management are essential for the effective operation of all types of motor vehicles in all climates and environments. Batteries tend to heat quickly at different times in their operating cycle, including when they are running at full capacity or in the charging (or fast charging) process. This is particularly true for fast-speed recharging systems, where research is focusing on offsetting damage to Lithium-ion batteries at certain temperatures through efficient insulation. There is also the problem of producing a rise in ambient temperature in the battery housing, further reducing charging capacities and potentially damaging electronic components. Silicones can offer low thermal conductivity, which means that it transfers heat at a low rate compared to other materials and also has the ability to maintain its properties and structure over a wide temperature range.
Silicones are a single class of materials that can be customized to provide required functions and find the right balance between conductivity, and insulation for each specific stage in battery operations. For example, foams are efficient in insulation, while adhesives and gap fillers are thermally conductive (see below Figure 1).
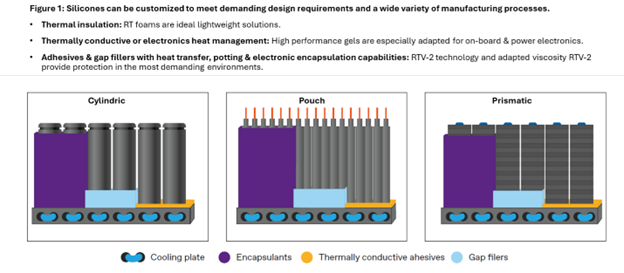
Silicones are customizable and versatile
While the advantages of lightweight silicone foams for insulation and the coating efficiency of silicone gels for encapsulation and potting spring to mind quite readily for battery designers, their adhesion features are equally compelling. In advanced Thermal Management Systems (TMS), many components come into play and, often, they must be bonded with efficient adhesives. For example, to ensure thermal conduction in batteries, designers use a metal cooling plate as an interface. These plates must be secured to the battery, usually with an adhesive.
Ideally, there are two requirements to be fulfilled for this undertaking: the process must be simplified, and the bond must be dependable and long lasting. Specially designed silicone self-adhesive bonds are therefore widely used to achieve these two goals. These silicone adhesives do not require priming either of the surfaces beforehand, they are stable, and they resist ageing across a wide range of temperatures. Silicones can also be purposefully designed to provide the right mix of adhesion characteristics, as well as to offer greater safety because they are not combustible and function as fire retardants.
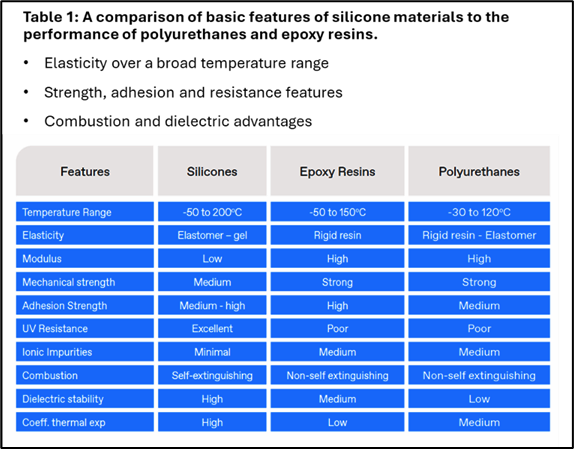
Processability/manufacturing benefits
Silicones flowability is a major advantage in automated processing compared to other materials, in particular polyurethanes (Table 1). Also, silicones can be formulated in a wide range of forms (liquids, gels, foams, etc.) and can be customized to variable potting times (pre-installation) and curing times (final reticulation or hardening) at given temperatures, to fit into existing or future processing systems. This flexibility and capacity to adapt is a major advantage for processing specialists in traditional automotive assembly, which is further heightened in H&EV manufacturing.
Laila Bonilla, Business Development Manager, Elkem
Laure Bertrand, Technical Service Manager, Elkem