Secure & Safe on the Road or Underwater
Dr. André Daubner, Volker Buchmann
Electric vehicles primarily use batteries as an energy source, which are “filled up” with electricity at charging stations. Electric driving offers us a whole new driving pleasure, but not only that – we’re also doing something for the environment, the climate, CO2 and NOX emissions. Safety innovations from the world of the internal combustion engine, such as brakes, airbags, distance warning systems and other modern achievements are taken for granted as the tried and tested standard. The fuel tank has been partially or completely replaced. Sure, but with what, exactly? In most cases by Li-ion batteries – but what about safety or the environment?
Safety is a number-one priority in Li-ion batteries. This safety that is not visible at first glance, and involves elements such as an emergency devices built into the outer shell of the battery housing, combining one, two or more functions. Here, it is important to note that these emergency devices do not prevent the battery cells from being thermally excited. They do however prevent pressure waves from causing sudden deformation of the housing.
What functions need to be covered?
- Bursting, for example if things get critical when a degassing unit opens
- Pressure compensation to equalize internal and external pressure differences during uphill and downhill drives, descents etc.
- Closing of the degassing hole so that no oxygen enters the internal combustion source
- Re-opening the hole again to relieve pressure for another event
Against the backdrop of recent flooding disasters, batteries should survive undamaged under water for a long period of time. In addition, there are requirements for regulating the temperature of the battery: active-regulation by a heat exchanger or immersion cooling. What’s more, the issues of recyclability should not be ignored.
Now, the statements above address many different aspects and questions. The state of the art is now that all these questions can be answered positively. Let’s take a look at this in detail.
Burst functions when it gets critical: A distinction must be made here as to whether you only want to open and close or also integrate pressure compensation. If you only want to open and close, you can use a mechanically constructed rupture disc or a movable cylinder. Better to use a gas-tight film that is suitable for bursting. The latter has several advantages: It is easy to bond with plastic, it can be adapted to different pressures and even reproduce asymmetric pressure conditions. If one wants to integrate pressure equalisation, membranes that are semi-permeable are necessary. This then implements both functions. For IPx9k (strong water jet) resistance, additional protection is required. That’s not much of a hassle, though.
Pressure equalisation is always necessary, no matter what battery chemistry is used. Differences in temperature alone causes pressure differences between the inside and outside. The same applies to ascents and descents. Pressure compensation elements are always important so that the seals of the battery housing are not subjected to too much stress. A semi-permeable membrane is an advantage here. In contrast to the previously mentioned membranes, these membranes are laminated with an additional fibre structure and are therefore also not burstable. It is particularly practical to adjust the membrane to the air flow rate while maintaining the same diameter; not the hole diameter to the air flow rate. This is achieved with a membrane portfolio that ranges from a few millilitres to several litres in relation to the air throughput.
If the emergency device closes again after the event, this is a further advantage, as the oxygen supply to the inside of the battery is interrupted, preventing fire from being additionally kindled. In addition, extinguishing water does not penetrate into the interior of the battery, which can also lead to unpleasant side effects. But what happens if the neighbouring cell or module has now been excited and another event is ignited? Here the degassing unit should open again and close after the event. Designs in this direction must not neglect the aspect of weight. Products made of steel are not light. whereas products made of temperature-resistant materials such as thermoset or thermoplastic are much lighter. After all, every gram costs valuable energy and range.

This year’s flood disaster also raises the question: What actually happens when my electric vehicle sits in a flooded underground garage for days? Or generally remains underwater for several days? We’re not only talking about a water column of a few centimetres, a few metres are needed to calm nerves. WEP (water entry pressure) of over 10 meters are quite possible. A water submersion time of many days can also be achieved with the right choice of materials. Here the tensile strength and the creep behaviour are important. A comparison of PTFE membranes with PET membranes shows that the tensile strength of PET is considerably higher than that of PTFE. PET has a tensile strength of over 20 N/mm² at room temperature, whereas PTFE is permanently deformed at 3 N/mm² (Fig. 1). This also allows conclusions to be drawn about the tolerances for temperature ranges. PET membranes, for example, have a much narrower tolerance. At this point I would also like to take a look at the pulsation capacity; due to the higher tensile strength PET membranes are much more resistant than other membranes.
In the past, a heat exchanger with tube plates was used for the air conditioning of the battery. Meanwhile, immersivly cooled batteries are en vogue. With this type of cooling, the battery is in liquid, filled with negative pressure. Usually this negative pressure is above the burst pressure of the battery system, which creates an asymmetry. Mechanical systems can cushion this well, but are difficult to adjust to an individual burst pressure. Gas-tight films, which also burst, are much more flexible and are available in different thicknesses for additional derivatives.
If you drive an environmentally friendly vehicle, you naturally also expect the individual components to be recyclable. Sure, we’re talking about safety-related products. But does a non-recyclable material have to be used? PFOA-certified materials are also state of the art here.
The type of membrane alone does not, of course, provide any safety – this has yet to be adapted. This is because a membrane alone cannot adapt to the required conditions – the bursting pressure in relation to the diameter. An individual disruptor from outside is still needed. You can easily imagine: one design requires pressures below 200 mbar, while other designs with the same membrane require 1.5 bar – and this with similar diameters.
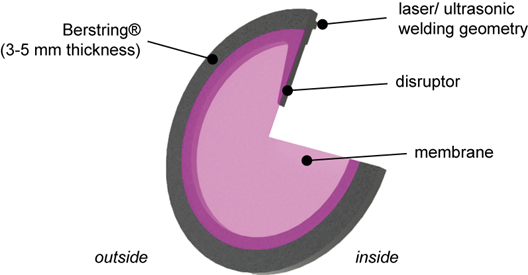
Figure 2: Berstring®
The term disruptor quickly comes up, but what should it look like?
Many influencing variables determine the character of the disruptor: material, thickness, shape, length and other parameters. At the best it’s just a prism (Fig.2). Through the interaction of structure and flow simulation with testing, product developments are possible in the shortest possible time. We use so-called ROBB test specimens (Rupture, Opening, Bursting and Breathing) for the prediction and validation of the functions. The tests are compared with the simulation results and adapted to the customer-specific product. This approach reduces the pre-development time to a few days by defining the function and creating the basis for product realisation.
Milko Konzelmann (CEO Konzelmann GmbH) welcomes this systematic approach: “Now we still need the interface definition and the connection to the housing. With this, the customer-specific product is completely developed”. Screwed, lasered, clipped, welded or other ideas are then adapted to the requirements. This is followed by the design of the injection moulds with the customer-specific geometry and the inhouse production of prototypes. These prototypes are already close to series production and can be used for initial tests. Especially tightness, burst, pressure and high-pressure cleaning tests are elementary, as well as tests over the required temperature range and media resistance.
Tests are then carried out to determine that the product selection has been optimally adapted to the requirements. Our studies have shown that there are indeed materials that combine all the desired advantages. The membrane is called Ventikon® and the product Berstring®.
Dipl.-Ing. ET (univ) Volker Buchmann business unit developer for eMobility at Konzelmann GmbH in Löchgau
Dr. André Daubner Head of the eMobility business unit at Konzelmann GmbH