Efficiency and CO2 emissions have driven the Electric Vehicle (EV) market development however customers will drive the market adoption. EVs are about to provide features that go beyond efficiency, with enhanced driving experiences and fast charging capabilities to promote added autonomy. To support this evolution and enable EV performance, OEM battery assembly manufacturers and designers are proposing new concepts and leading-edge manufacturing technologies with the goal of reducing assembly weight wherever possible, and to provide a robust and safe product with fast and cost-efficient manufacturing process.
As e-mobility and battery energy storage applications grow in number and power density, designers seek to achieve the best of both worlds with high design efficiency and high design flexibility, Current battery cells technologies like cylindrical, prismatic or pouch types run the risk of electrical failure or thermal runaway. Electrical connection to these battery cells is commonly done through a so-called bus bar system. Bus bars being a conductive plate generally made of copper or aluminum insulated with layers of electrical insulation films. Nowadays, bus bars have become the preferred method of connection, as they provide an error- free and robust method of power connection and are set in a precise configuration.
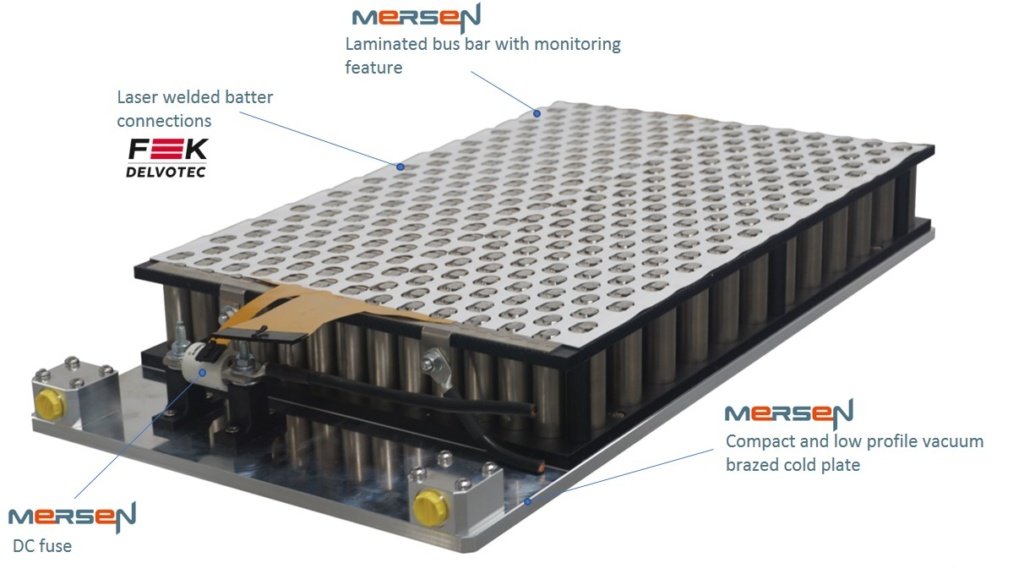
In earlier battery generation module designs, the connection between the bus bar and the cell is made by either a laser welded wire / ribbon or by ultrasonic welding. These connection methods are relatively time consuming and add to overall production cost.
To reduce cell welding process time and manufacturing cost, Mersen has developed a new and dedicated laminated bus bar design especially developed for battery application and laser welding process: the Infini-cell® bus bar.
The lightweight single layer Infini-cell bus bar solution is a combination of laminated insulation and thin conductive materials. Thanks to the thin conductive layer between 0,2 and 0,5 mm, battery cells can be easily welded to the bus bar connections using laser welding. The Infini-cell® bus bar design has two conductive layers: one for conducing power to the cells and the other layer used to monitor the status of battery cells.
The power conducting layer provides the flexibility for the OEM to design their battery cells in either series or parallel configuration, in order to efficiently reach the required voltage and power level required for their power module.
The monitoring layer of the bus bar in turn provides an embedded conductive path for temperature and voltage monitoring in specific areas of the assembly. The monitoring layer component will then typically feed the module Battery Management System (BMS). The BMS has the function to monitor voltage and temperature of selected cells not to ensure safe operation of the cells and to reduce risk of heat runaway issues, but also monitors the status of charge and current balancing the current during the charging cycle. The integration of voltage and temperature sensors onto the bus bar as close as possible to the cells can lead to a better management of the complete battery assembly as well as its safer operation.
Traditional cells interconnexion solutions that include monitoring, are mainly non-laminated busbars that are quite heavy, bulky, and poorly integrated in the module box. The newest design Infini-cell® bus bar is a lighter alternative and reduces the overall weight of the battery assembly. Infini-cell® welding process eliminates the need for wire or ribbon connections between bus bars and battery cells and so drastically reduces assembly time as well as downtime in cases of wire breakage or ribbon spool jams.
This new welding process is more than four times faster than the conventional combination of wire / ribbon insertion and welding method, and can provide a process time reduction of up to 60%. Such features greatly benefit high demand production runs typical to EV and EES applications, according to Dr. Jean-Francois de Palma Head of R&D and Innovation for Mersen
Other electrical safety concerns such as battery cell short circuits can occur during the module assembly and during the battery’s lifetime. To prevent short circuits in battery cells, a surge protection system is added within the module assembly. Here at Mersen we have introduced a new line of DC Over-Current protection (O.C.P.) developed to address specific needs in Battery Systems application. Typical requirements for module protection are within 100VDC and an RMS current within 200A.., he concludes
As battery technologies and price improve to better serve the E-mobility segment, so does the need to increase the reliability of battery connections and safeguarding battery cells against electrical faults. Infini-cell laser welding process can provide an efficient and more durable battery cell-to-bus bar connection platform at much lower price than existing solutions. Mersen over current protective devices are specifically designed to protect people and equipment in battery related applications.
About the author Dr. Jean-Francois de Palma is Leading R&D and Innovation for Mersen, SPM business Unit. He has PhD in power electronics. He is been working with Mersen for the last 30 years in fuse, bus bar, cooling and recently capacitors product development. He is current chairman of the SC32B LV fuse committee. He is author and co-author of many technical papers and patents
Visit ep.mersen.com to learn more.
ABOUT MERSEN
Global expert in electrical power and advanced materials, Mersen designs innovative solutions to address its clients’ specific needs to enable them to optimize their manufacturing process in sectors such as energy, transportation, electronics, chemical, pharmaceutical and process industries. Mersen Electrical Power provides a comprehensive line of current-limiting fuses (low voltage, general purpose, medium voltage, semiconductor, miniature and glass, and special purpose) and accessories, fuse blocks and holders, power distribution blocks, low voltage disconnect switches, surge protective devices, high power switches, heatsinks, laminated bus bars, and more.