Battery systems and their performance.
Continuous progress in battery technologies leads to higher energy densities that, in turn, require greater protection. Battery system design is critical, and errors in the field can be detrimental to both machines and humans. In order to mitigate such risk and increase reliability, designers must ensure that components (e.g., cells, cooling mechanisms, bus systems and associated battery management systems) are isolated from each other and protected against external environments.
High performance coatings provide protection.
Conformal coatings have been used for decades to protect automotive components and designs. Liquid coatings, for example, have been used as potting and conformal coating materials throughout the transportation industry. The thickness associated with these coatings, however, can add unwanted weight to components; in addition, their moisture and dielectric barrier properties – as a total package – are often insufficient for the increasingly harsh environments in which electric and hybrid vehicles must operate.
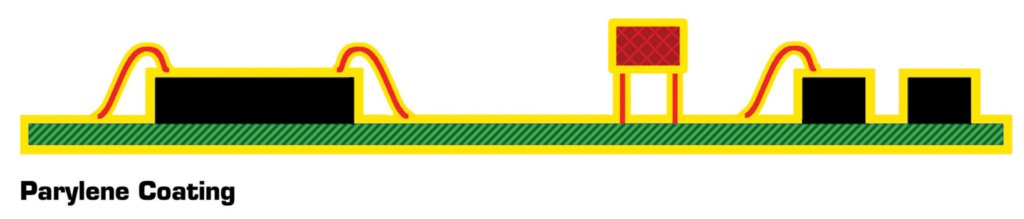
Fig. 1: Schematics of a Parylene-coated PCB
Today’s electronic systems require solutions that are lightweight, provide excellent barrier properties and have little to no influence on heat dissipation. Deposited as a gas, Parylene coatings meet these needs by providing thin film protection to a host of automotive sensors, circuit boards, MEMS and other components, including battery management systems.
Parylenes offer reliability and stability.
Parylene is the collective term for organic polymer coating materials that are applied as thin, uniform, optically-clear films. As inert materials with very low moisture absorption, Parylenes offer protection against chemical and moisture vapours and fluids.
Parylene films are deposited as a gas at room temperature; as such, the molecules actively penetrate into crevices and gaps, providing uniform protection in, around and under components (Figure 1). Parylene coating thicknesses are generally measured in microns (0.5 – 25 microns, for example), much thinner than traditional liquid coatings that tend to be measured in mils. Commonly described as ultra-thin and nano-scale in nature, Parylenes do not add significant weight or mass to the components that they protect. Finally, due to their elasticity, Parylene coatings do not become brittle with exposure to frequent and/or extreme temperature cycling.

The coating process.
Parylene coatings are applied in specialized vacuum deposition systems using a vapour deposition polymerization (VDP) process (Figure 2). The VDP process uses a powdered raw material known as dimer and an evacuated, room temperature deposition chamber. There is no liquid phase during deposition, and no solvents, catalysts or environmentally-restricted materials are involved. With proper processing, the resulting film conforms precisely to the underlying surface and is free of imperfections, forming an ultra-thin, transparent film. The result is a very high degree of coating conformability, with uniform coating thickness (controlled thickness down to mere angstroms) deposited simultaneously on surfaces – over inside and outside corners and into deep crevices. Areas that are not to receive coating (e.g., connectors) must be masked prior to the deposition process. Due to their molecular-level deposition, Parylene coatings can easily be applied on nano devices, nanoelectronics and other nano parts for high performance and reliability.

For ease of reference, a comparison of conformal coatings properties is provided in Figure 3.
Electrical properties.
As a family, Parylenes have extremely low dielectric constants and dissipation factors, enabling the coatings to provide small, tight packages with dielectric insulation via a thin coating. Parylene layers of 25µm, for example, withstand voltages between 5,400 to 7,000V, depending on the Parylene type, and it has been demonstrated that the voltage breakdown per unit thickness increases with decreasing Parylene film thickness. In addition, in high-frequency applications, both the dielectric constant and the attenuation on the signal are almost negligible.
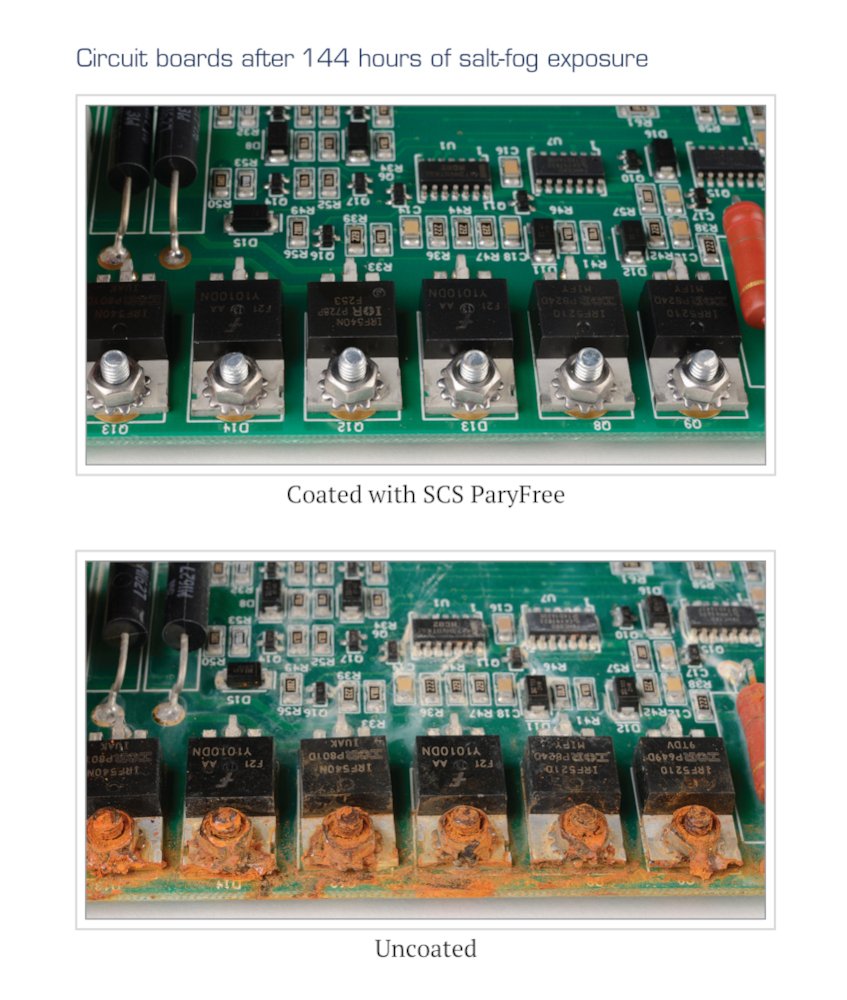
Chemical and moisture barrier properties.
Parylenes are known for their excellent resistance to moisture and chemicals and are insoluble in all organic solvents up to 150°C. Parylene HT® has specifically been tested against a wide array of automotive chemical and fluids, including antifreeze, engine oil, transmission fluid and nitric and sulfuric acids. Figure 4 shows that the Parylene films minimally swelled with exposure; it should be noted, however, that the swelling completely reversed after the solvents were removed by vacuum drying, and no changes were observed to the films’ physical or chemical properties.
ParyFree®, one of the newest commercially-available variants of Parylene, also provides excellent moisture and chemical barrier protection – similar to that of Parylene C – in a halogen-free coating (Figure 5). As international environmental initiatives increase, ParyFree conformal coating proves to be a viable halogen-free protection option.
Thermal and UV stability.
While all of the Parylene variants provide similar properties and benefits to each other, each has their own unique capabilities. Thermal stability is one property where their unique properties are evident. Due to its molecular composition, Parylene HT is thermally stable in harsh environments up to 350°C long-term; it can also withstand exposures up to 450°C short-term. Additionally, Parylene HT offers the highest UV stability of the Parylenes, exhibiting stability after more than 2,000 hours of UV exposure (ASTM G154).
Conclusion.

Driven largely by concerns about the environment and passenger safety, the transformation of the automotive market toward an electric vehicle (EV)-dominated future is well underway and is being further incentivized globally by government regulations and initiatives. The reliability and performance of vehicle electronics and sensors, including battery management and related systems, are of critical importance. As such, in order to avoid costly failures, it is important that manufacturers provide protection for these vital components. Parylene conformal coatings have provided such protection for 5 decades while also meeting the ever-evolving global environmental standards and initiatives.
Brent Frizzell, Electronics & Transportation Market Manager