In the discussion about European giga factories for battery cells, the supply of electrode powder (cathode and anode) is often ignored. In this context, market analysts expect the demand (production capacities) for cathode active material (CAM) to multiply worldwide from the current 500 kTpa to 1,250 kTpa in the next ten years (source: Avicenne Energy 01/2020, Cathode Active Material Forecasts 2000-2030).
A battery for all-electric drive electric vehicles contains about 80 to 100 kg of CAM material with a cost share of about 40 percent of the total battery cost. For batteries in this application area, NCM compounds (N = nickel, C = cobalt and M = manganese) in particular have become established as CAM materials with higher nickel contents (high nickel) (see the text box “CAM for electromobility”).
The problem is: By building European battery giga factories, the dependence on Asian manufacturers has not been resolved. Almost exclusively, the market and technology leadership for the complex manufacturing process of CAM is held by Japan and South Korea.
Cathode Active Material (CAM) – Production in Europe?
European automotive OEMs and battery cell manufacturers expect to have production of critical battery components in and from Europe. However, CAM production in Europe is a major challenge for at least four reasons:
Lack of know-how
Up to now, CAM powder development and production has been largely unknown territory for European manufacturers. There are no established players with know-how and experience yet. For this reason, cooperation and joint ventures with established Japanese and Korean companies are being sought and have already been implemented.
Higher level of automation as well as quality standards
The 1:1 transfer of plant technology from South Korea or Japan alone is not sufficient to set up a production plant in Europe. In Europe, a higher degree of automation and an overall higher general quality standard of plant technology are required.
Higher safety and environmental standards
The CAM systems currently used in Asia do not meet the significantly higher legal requirements for machines and processes in Europe. This includes the EU Machinery Directive (CE conformity) in particular. CAM based on NCM or NCA contains e.g., cobalt, which is classified as potentially highly toxic and carcinogenic, which requires extensive safety and personal protection concepts for production plants, which are not required in Asia.
Higher CAPEX and OPEX
In addition to the higher investment costs resulting from the reasons listed above, the increased operating costs (personnel and energy) are also relevant when costs are calculated for CAM plants for Europe.
Trends in CAM production plants
Calcining kiln as the centerpiece of a CAM production plant
CAM materials are continuously being developed further, with energy density, capacity, service life and fast-charging capability being decisive factors, without neglecting safety and environmental compatibility. In addition, efforts are being made to optimize the manufacturing process. Today, modern calcination processes are usually divided into two to three different thermal process steps. However, as a result of these further developments, the demands on kiln technology are becoming more and more demanding.
High-nickel CAM process
The high-nickel CAM process requires LiOH as the lithium source due to its higher reactivity, which results in increased water vapor formation and increased as well as more aggressive emissions in the kiln compared to the use of Li2CO3. In addition, pure O2 is required as process gas, which should ideally be fed to the process preheated. Controlled process gas supply and exhaust gas discharge (gas flow control) are of particular importance here and are even more important than the equally significant temperature homogeneity of the powder. This is where process knowledge and kiln construction know-how are required.
Higher quality requirements and process know-how
The above-mentioned process changes and optimizations lead to significantly higher quality requirements for the kiln technology with, among other things, gas tightness of the kiln, drainage systems, avoidance of condensation areas, gas flow control (see above), a generally high manufacturing quality or the use of high-quality key components, such as high-quality ceramic rollers or the correct selection and use of refractory materials. If the plant does not meet the quality requirements, the susceptibility to failure increases disproportionately for CAM high-nickel processes compared to calcining processes of CAM with lower nickel contents (e.g., NCM111, NCM523). It should be kept in mind that the quality-related susceptibility to failure can become apparent after a certain operating time of 0.5 to 1.0 years.
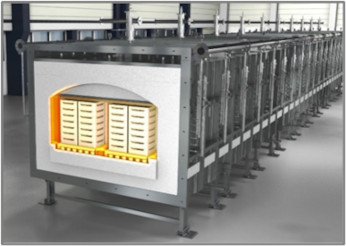
Pusher-Kiln-CAM calcining kiln PK 4×7 achieves a 2-3 times increase in throughput compared to the RHK 4×2.
Example: Pusher Kiln simulation and validation
Up to threefold increase in throughput thanks to pusher kiln technology
RHK (Roller Hearth Kiln) is the state-of-the-art technology in calcining kilns. However, it has reached its limits in terms of the throughput that can be achieved and is also at its limits in terms of development and process technology (see picture cross-sections kiln types RHK 4×2, 4×3, 6×2 and PK 4×7).
RHK 4×2
RHK 4×2 (loading with 4 saggars side by side and 2 saggars on top of each other) with a length of 50 to 55 m is the current state of the art (VoC) for the relatively demanding main calcination.
RHK 4×3 or RHK 6×2
Throughput can be increased by using RHK 4×3 or RHK 6×2, but this can have a negative impact on operational reliability. The main problem here is the gas flow control (especially with RHK 6×2) and the more demanding visualization of temperature homogeneity compared to RHK 4×2.
Kiln extension
Another way to increase throughput is to extend the kiln. However, this involves the risk of the saggar running on the rolls (meandering). Faults of this type must be avoided in gas-tight systems and when O2 is used as process gas, because this usually necessitates lengthy cooling and reheating of the kiln system which leads to a reduction in productivity due to the loss of operating time.
Pusher kiln technology
Innovative pusher kiln CAM calcining kilns
After more than three years of development, the first six pusher kilns will go into operation in the CAM industry in December 2021. With the new concept, for the first time 28 saggars are transported through the kiln simultaneously in one row (see picture cross-sections kiln types “PK 4×7”), which decisively increases throughput. The CAM pusher kiln was extensively tested and validated by ONEJOON GmbH (Germany) using CFD simulation, bench tests to derive and validate the simulation models, and a test kiln. The development process was supported by continuous knowledge sharing with CAM producers (VoC). The main advantages of this new technology compared to RHK 4×2 (main calcination):
- 2 to 3 times increase in throughput.
- CAPEX reduction of up to 30 to 50 percent
- OPEX reduction (power consumption, process gas consumption, CO2 footprint, maintenance effort) by up to 30 to 40 percent
- Reduced plant footprint to the extent of 60 percent.
- Improved product quality and homogeneity due to more controllable process conditions, identical process conditions for all saggars, better temperature uniformity (especially during the heating phase), and the possibility of preheating the process gas to close to the zone temperature level.
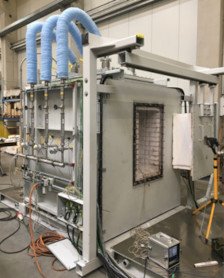
Kiln construction bottleneck for production capacities in Europe
The further improvements of calcining kilns for CAM with a high nickel content require a very high level of process knowledge and many years of process experience. Typical kiln builders who still successfully marketed kiln for NCM111 or NCM523 will no longer be able to cope with the technological (quantum) leap, because CAM calcining kiln builders are changing into “technology providers”. Ultimately, only a few kiln manufacturers will still be able to supply process-compliant, marketable calcining kilns for high-nickel CAMs.
The simultaneous massive increase in CAM production capacities worldwide and in Europe will lead to a kiln construction bottleneck with extended delivery times. The same applies to high quality kiln equipment and kiln materials (e.g., ceramic rollers, refractory materials, etc.).
It is expected that alliances and partnerships between CAM producers and CAM technology providers will emerge over the next few years to expand CAM production facilities. This cooperation will create special process and kiln construction knowledge, which the CAM producer wants to keep in the partnership. In addition, the projects will be so large that probably a kiln builder will only be able to support two partnerships.
Process know-how from South Korea and plant know-how from Germany
An alternative to the 1 to 1 transfer of know-how from East Asia is to combine CAM process knowledge from South Korea with know-how for large-scale plant projects from Germany. This is the approach of the Korean-German company ONEJOON.
CAM market leader in South Korea
ONEJOON Co. Ltd. from South Korea has more than 15 years of product and process know-how in the CAM sector and is the market leader for calcining kilns in South Korea, with production facilities in South Korea, Germany and China. Having already supplied more than 70 CAM Roller Hearth Kilns (RHK). Most of them for NCM622/811, NCA and high-nickel applications (see text box “CAM for electromobility”).
Complete CAM powder process lines
In addition, the company has launched complete CAM powder process lines with a total production capacity of over 100 kTpa of NCM622, NCM811 and NCA.
Technology provider for European CAM projects
By combining Korean process know-how with the experience and knowledge of handling large projects in Europe, the firm is optimally positioned to support the development of the CAM market in Europe. In addition, it is the only kiln manufacturer in the world who has mastered powder process technology and can supply complete CAM powder process lines. This allows innovative complete CAM plants with optimum integration of CAM kiln technology into the overall plant to be realized from a single source, meeting European regulatory framework conditions.
Cathode Active Material (CAM) for electro-mobility (electric vehicles)
Different types of CAM are used depending on the battery type and application:
NCM materials for electro-mobility (electric vehicles): NCM materials (N = nickel, C = cobalt, M = manganese), some with aluminum content (so-called NCMA) and NCA materials (N = nickel, C = cobalt, A = aluminum) have become established in the electric vehicle sector. The more cost-effective NCM/NCMA have a significantly higher market share compared to NCA. In order to increase battery performance (e.g., range) and reduce costs, efforts are being made to increase the nickel content and reduce the cobalt content.
NCM622 systems are state-of-the-art: In batteries of future electric vehicle generations, especially in more powerful vehicles, NCM622 (60 % Ni, 20 % Co, 20 % Mn) up to NCM811 (80 % Ni, 10 % Co, 10 % Mn) or systems with even higher nickel content (high-nickel systems) will be used.
NCA for first-generation electric vehicles: NCA is very powerful with a nickel content of > 90 % and is mainly used in power tools but also in electric vehicles. For example, TESLA vehicles of the first generations were equipped with them, although there are signs of a change in strategy at TESLA more in the direction of NCM systems.
i. V. Markus Lehmann
Senior Key Account Manager ONEJOON Co. Ltd.