New environmental protection guidelines and stricter emission standards are the result of a growing sense of responsibility for climate protection. In the automotive industry, rigorous emissions regulations and the aim to achieve greater efficiency are driving innovations and the development of new mobility concepts. Current trends are, for example, autonomous driving and e-mobility – a large number of hybrid and electric solutions are conquering the ever growing market.
Various drivetrain architectures are available to automobile manufacturers for the design of mild and plug-in to full hybrids, ranging from a simple P0 configuration to P1, P2, P3 and P4 to PS (power split).
The P2 architecture, which is currently receiving a lot of attention in the industry, is positioning the electric motor between the transmission and the combustion engine. To disengage the combustion engine, this configuration uses a disconnect clutch enabling pure electric driving. The technology is suitable for various types of transmissions, including manual transmissions.
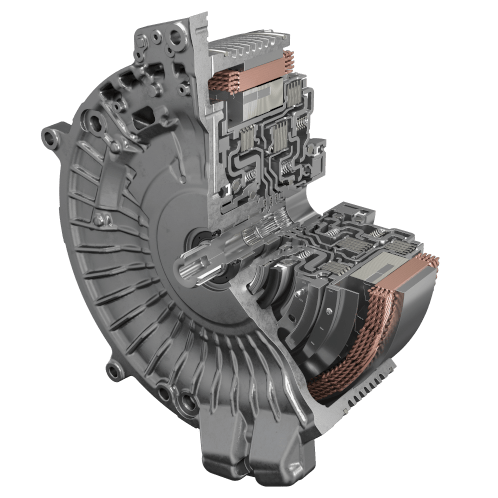
BorgWarner’s innovative technologies support manufacturers in hybridizing their vehicles by providing a wide range of functions and design options. The company’s portfolio includes two types of P2 hybrid modules (Fig. 1), which are easy to integrate into a drivetrain and can be tailored to customer requirements. An on-axis design with the electric motor integrated directly into the drive shaft or a configuration parallel to the axis can be used depending on the installation space available. The on-axis arrangement is ideal for powertrains with longitudinally mounted engines, with sufficient space for integrating the electric motor. Due to the axis-encompassing design, torque transmission can be realized easily and cost-effectively.
Configurations with transversely mounted engines and limited space often use off-axis configurations, which provide advantages in the transmission ratio and high flexibility in installation. In this solution, the rotational speed and torque are transmitted, for instance, by a chain (Fig. 2).
Both architectures can be supported with normal pressure (about 20bar system pressure) or high pressure (up to 60bar system pressure) clutch layouts. Hydraulic control modules which exactly fit to these applications are available in the BorgWarner product portfolio, too.
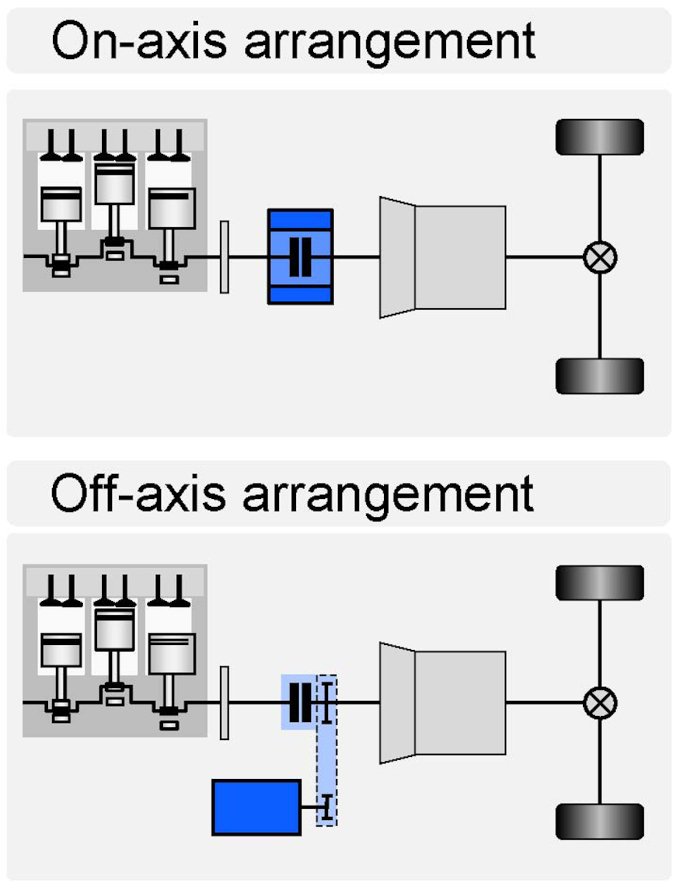
Criteria for the module configuration
When implementing various module configurations with electric engines not only space requirements but also the operating voltage, winding type and cooling system are relevant. An electric motor with a small diameter and high rotational speeds for better efficiency can be easily integrated within the off-axis solution. The on-axis design, on the other hand, is more suitable for a larger electric engine with lower rotational speeds and higher torque generation.
There are two alternatives available for the operating voltage. Low-voltage systems offer a cost-effective solution and significant CO2 reductions. Sufficient power for pure electric driving is generated by high-voltage systems providing more than 100 kW. These are also characterized by the highest power savings potential. (Fig. 3).
Not only the operating voltage, but also details such as the windings and wire shape influence the performance of the electric motor. Thanks to their low torque ripple and low cogging torque, distributed stator windings improve the Noise, Vibration, Harshness behavior (NVH) of the overall system. Ideally, a rectangular wire, which maximizes current density and improves heat transfer, acts as a conductor. When selecting the rotor design an interior permanent magnet (IPM), which is suitable for all stator designs, is preferable to an induction machine. It maintains the magnetic field without external excitation, thus increasing the overall performance and efficiency of the electric engine.
Various cooling solutions
Depending on the operating conditions and temperatures, different types of cooling can be used for the electric motor. With oil cooling, the principal thermal components and the coolant are in direct contact. This process is very effective and achieves a continuous cooling capacity for constant average temperatures and ensures an ideal heat transfer. Cooling with a water-ethylene glycol mixture represents an alternative method in which significantly lower coolant inlet temperatures can be realized , which is at an advantage for dealing with temporary temperature peaks. The overall efficiency is slightly lower since the cooling medium itself is not direcly in contact with the heat source. The so-called outer cooling jacket dissipates the heat of the electric engine to the coolant via the stator.
When both methods are combined, the water-ethylene glycol mixture flows around the stator at an inlet temperature of only 65°C. Internally injected oil, which typically has a temperature of approx. 90°C due to gearbox operation, dissipates the heat from the rotor. This approach achieves high efficiency in normal operation and very good performance at peak temperatures. However, the use of an additional cooling jacket often comes at significantly higher costs. For this reason, the cooling capacity actually required to meet the target should be carefully examined in the design phase.
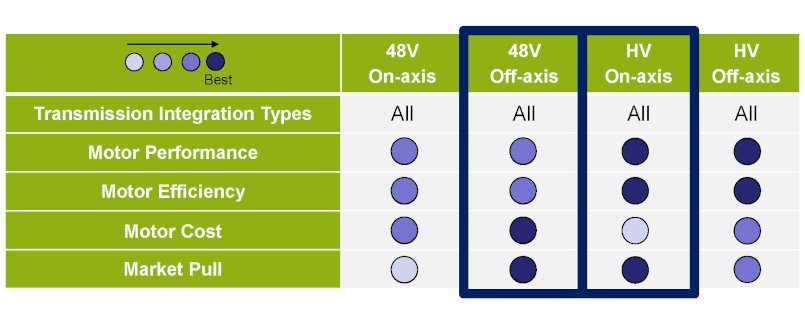
Types of coupling
In a P2 hybridization configuration, different types of couplings can be used to separate the combustion engine from the rest of the drivetrain. Due to its small size and low cost, combined with high efficiency, a freewheel is particularly suitable for applications where space is critical and applications are trimmed for maximum efficiency. Functional disadvantages can be avoided mainly by using multi-disc clutches. Especially wet friction plate clutches, which are characterized by a combination of high functionality and compactness as well as durability, are particularly suitable for this.
If the transmission architecture employs a dual clutch basic transmission, the disconnect clutch as well as the dual clutch can even be integrated into a complete module along with the electric motor, resulting in many advantages. The triple clutch thus generated leads to a further significant reduction in installation space requirements and is currently becoming the most popular configuration in this transmission segment.
Summary
The P2 configuration represents one of the most future-proof hybridization architectures that manufacturers can employ to speed up their vehicles’ readiness for the market. The bonus: It offers easy-to-use, cost-effective electrification options and can be flexibly adapted to customer specifications. It also enables hybrid functionalities such as stop-start, regenerative braking, electric motor charging and purele electric driving. Manufacturers can hybridize existing power trains at low additional costs because neither the engine nor the transmission need to be modified or even replaced on a large scale.
BorgWarner’s technology combines efficiency, flexibility in design options and durability, thus making a significant contribution to the success of hybridized vehicles.
Author
Eckart Gold Director Engineering at Borg Warner Transmission Systems in Shanghai, China.