Alena Useinovic
The move towards smarter forms of transportation is revolutionising the automotive sector, with growing consumer interest in electric and autonomous vehicles. Technological developments across all of the components that comprise electric drive systems are playing a pivotal role in creating products that are both technically advanced and sustainable, as Schaeffler’s UK vice president for automotive technologies, Alena Useinovic, explains….
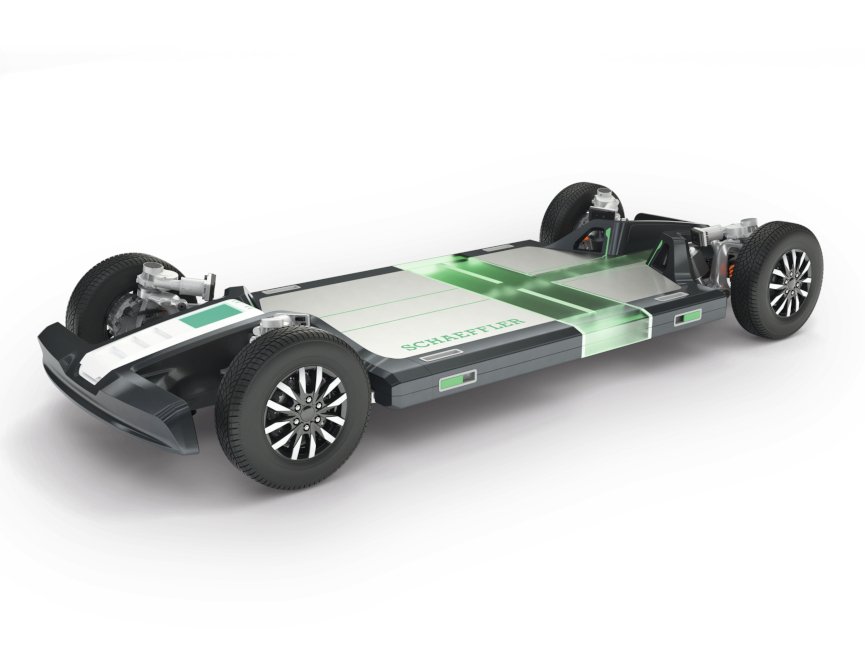
“Transportation is a major generator of CO2 emissions across the globe and contributing to a more sustainable planet is a challenge for vehicle manufacturers. However, progress is being made and, according to the International Energy Agency (IEA), transport emissions increased by less than 0.5 per cent in 2019 compared with 1.9 per cent annually since 2000. That said, transportation is still responsible for 24 per cent of direct CO2 emissions from fuel combustion – a situation that has created significant opportunities for the development of innovative transport related technologies and concepts.
Value added
As a result of the move towards more sustainable transportation, automotive technology will change considerably in the next decade with, according to Statista, one in five new car sales expected to be electric. Over that period self-driving autonomous vehicles will also be developed and added to the world’s fleet, with the rate of technological progress greatly affecting the speed at which we all move towards a more sustainable future. This allows for further segmentation in the automotive industry, particularly in regard to components, with companies under pressure to develop innovations in autonomous mobility.
Paving the way
While the use of electric vehicles continues to gain momentum, the technology that paves the way for autonomous driving is seeing significant progress. Development activities are mainly in the area of steering, focusing on the chassis side of vehicle dynamics. Drive-by-wire systems transmit driving and steering commands to the vehicle wheels purely through electronic signals. The technology has been proven in the field, with some systems having achieved more than a billion accident free kilometres so far.
Drive-by-wire systems should be triple redundant for maximum safety and meet the exacting functional safety requirements of ISO 26262. Ensuring that the components of an autonomous vehicle are able to operate correctly relies on the integration and use of robust and reliable software.
World view
Founded in 2003, AUTomotive Open System ARchitecture (AUTOSAR) is a global development partnership of vehicle manufacturers, suppliers, service providers and other companies from the automotive electronics, semiconductor and software industries. AUTOSAR interfaces directly with vehicle electronics and onboard communication and network architectures, enabling it to be integrated into existing vehicle use assistance systems, offering a system that is highly scalable and extremely flexible.
What’s more, it can record every steering parameter, which in autonomous vehicles provides feedback for an advanced driver assistance system. It also means that data about the road network can be collected, analysed and responded to in order to create a smoother ride. Being able to avoid potholes and other obstacles is a major advantage, not just in terms of comfort and reduced vehicle maintenance but also passenger health and safety. Steering technology combined with AUTOSAR means that data about road conditions can be collected with a camera and vehicle dynamics adjusted based on the held information.
Creature comforts
Autonomous mobility provides an opportunity to completely rethink the design and layout of vehicle interiors, as well as delivering enhanced safety and ride comfort. Once there is no longer a need for a driver, the experience provides more freedom to relax, work or be entertained. With a greater focus on the utility of the interior space, it becomes vital to balance design with functionality.
As the future vehicle interior is set to be more like a living room on the road, force-feedback handwheel actuator technology will facilitate greater design flexibility. A mechatronic solution that replaces the conventional steering wheel and mechanical steering column, it reduces the amount of space required for the steering system, allowing the wheel to be stowed in the centre console.
It can suppress undesirable feedback, such as vibrations from uneven road surfaces, and supports variable steering gear ratios, enabling new driving dynamic functions. Modular and scalable, it can be adapted to various applications and classes of vehicle. Combined with a drive-by-wire system and mechatronic actuators on the steering gear, it provides intelligent front wheel steering.
On a roll
Rolling chassis systems also open the way to completely new forms of autonomous mobility through a scalable vehicle platform that enables new, driverless solutions for passenger and freight transport, as well as for specialised applications such as cleaning machines. Its flexible architecture supports a broad array of steering and drive variants to suit customer requirements, and includes everything from single electric axles combined with central steering to implementations incorporating four corner modules.
Corner modules have been developed that optimise scalability with a steering angle of up to 90°. They comprise a wheel hub motor, a wheel suspension system incorporating air suspension that enables the vehicle to ‘kneel’, for greater ease of access, an actuator for electromechanical steering and a brake mechanism. Leading manufacturers are also currently developing a new, flexible platform for self-driving shuttles and other vehicle products to offer customers worldwide solutions for mobility-as-a-service (MaaS) and transportation-as-a-service (TaaS).
Efficiency drive
Electrifying powertrains to enable efficient mobility is the key to sustainable transport. Using far fewer components than a vehicle powered by an internal combustion engine, powertrain suppliers are making substantial investments in the development and production of electrified components. Power electronics make a decisive contribution, alongside the motor, to powertrain efficiency, and combining the electric motor, transmission and power electronics in one system aids functionality and operational efficiency.
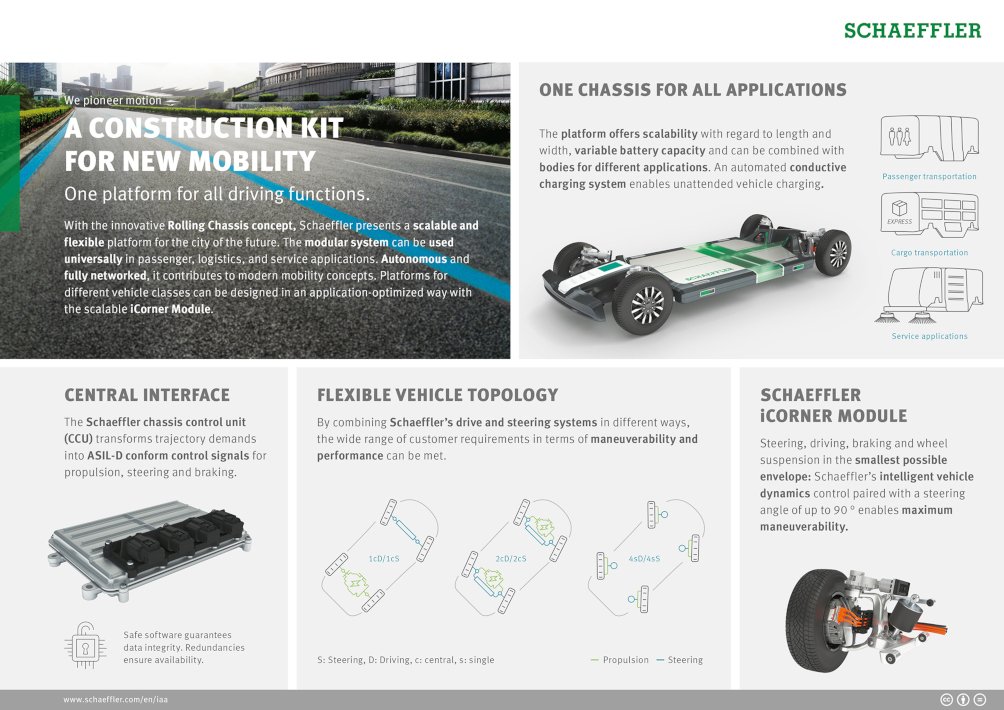
800V power electronics systems for electric axle applications in high performance vehicles are now available that enable continuous outputs of up to 330kW and short-term peak outputs of up to 500kW. The achievable power density of up to 70kW per litre includes small housing dimensions and, consequently, advantages in integration.
Cutting edge systems use silicon carbide wide bandgap technology in the 800V onboard power supply. This significantly reduces power losses compared with conventional silicon insulated gate bipolar transistor technology, enabling efficiencies of over 99 per cent in defined load ranges. As a result, the overall range of electric vehicles can be noticeably increased, with charging speeds achievable with the 800V class, considerably higher than those achieved with the 400V class that has been widely used to date. An in-house motor control solution is also used, which enables various modulation processes and variable switching frequencies.
Thermal management is a key consideration in electric vehicles and centres around the movement, as well as removal, of heat from a system. To achieve a high level of efficiency, a thermal management system should continuously regulate temperature – particularly of the battery, electric motor and the power electronics – which must be adapted to the ambient and operating conditions. The system also controls the temperature in the interior of the vehicle and simultaneously ensures the best possible vehicle range.
Thermal management systems are now available where two electric water pumps, the central electronic unit for the pumps and valves, and a refrigeration circuit interface are all integrated in the central control unit for coolants and refrigerants. Compared with conventional, non-integrated systems, this reduces the required installation space by up to 60 per cent and, with a hydraulically optimised design, lays the foundation for a high degree of overall system efficiency.
One direction
Although there’s still a long way to go in terms of creating a world of autonomous electric vehicle owners and drivers, the progress made so far is encouraging. Rapid regulatory and technological change, increasing urbanisation and growing social awareness of mobility are also increasing the need for alternative and novel concepts. The next few years promise to be exciting times, and types of pioneering solutions outlined above will smooth the way for autonomous mobility in the future.”
Alena Useinovic vice president for automotive technologies, Schaeffler UK