New components for electromobility require novel manufacturing strategies
According to expert estimates, by 2040 almost 45 percent of all passenger cars sold worldwide will have a battery or fuel cell drive system. This will result in a large number of new systems and components in production. This also poses a challenge to the supplier industry.
Automobile manufacturers worldwide are working to reduce emissions. According to a 2022 study by the German industry association VDMA and FEV Consulting GmbH, almost 45 percent of a total of 128 million passenger cars sold worldwide will be powered purely by battery electricity or fuel cells by 2040. At the same time, the experts expect a worldwide decline in sales figures for vehicles with combustion engines, namely by 16 percent compared to 2019. Following the development, the demand for electrical systems and components is increasing. Efficient fuel cells, batteries, electric motors, and high-performance electronics as well as cooling technologies are the future growth drivers.
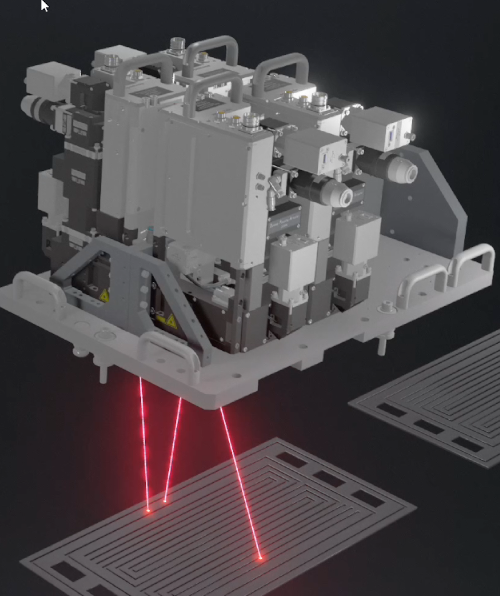
With the new system, Scansonic is responding to the increasing demands for speed and quality in laser processing. For example, for laser welding of bipolar plates, battery contacts, hairpins or surface coolers for car battery trays in electric vehicle drives.
This has a major impact on traditional manufacturing technologies in the automotive industry. Laser processing is also facing new challenges. New processes are emerging. Take bipolar plates, for example: As a stack, they make up the core of the fuel cell and influence the power density of the stack. Their thickness determines the overall weight of the energy source, usually only about 0.1 mm. They account for up to 45 percent of the production costs.
Take battery boxes, for example: They are among the crash-relevant components due to the fire risk of the batteries. The quality of the weld seams makes a decisive contribution to its stability. Most components, and thus every weld, must be helium-tight. If a single individual weld is not in order, the component must be reworked. These costs are to be avoided in any case. Therefore, users expect the highest quality in terms of electrical, mechanical and structural properties of the finished parts. Structures made of high-strength aluminium alloys are generally used in manufacturing, but these have a marked tendency to hot cracking.
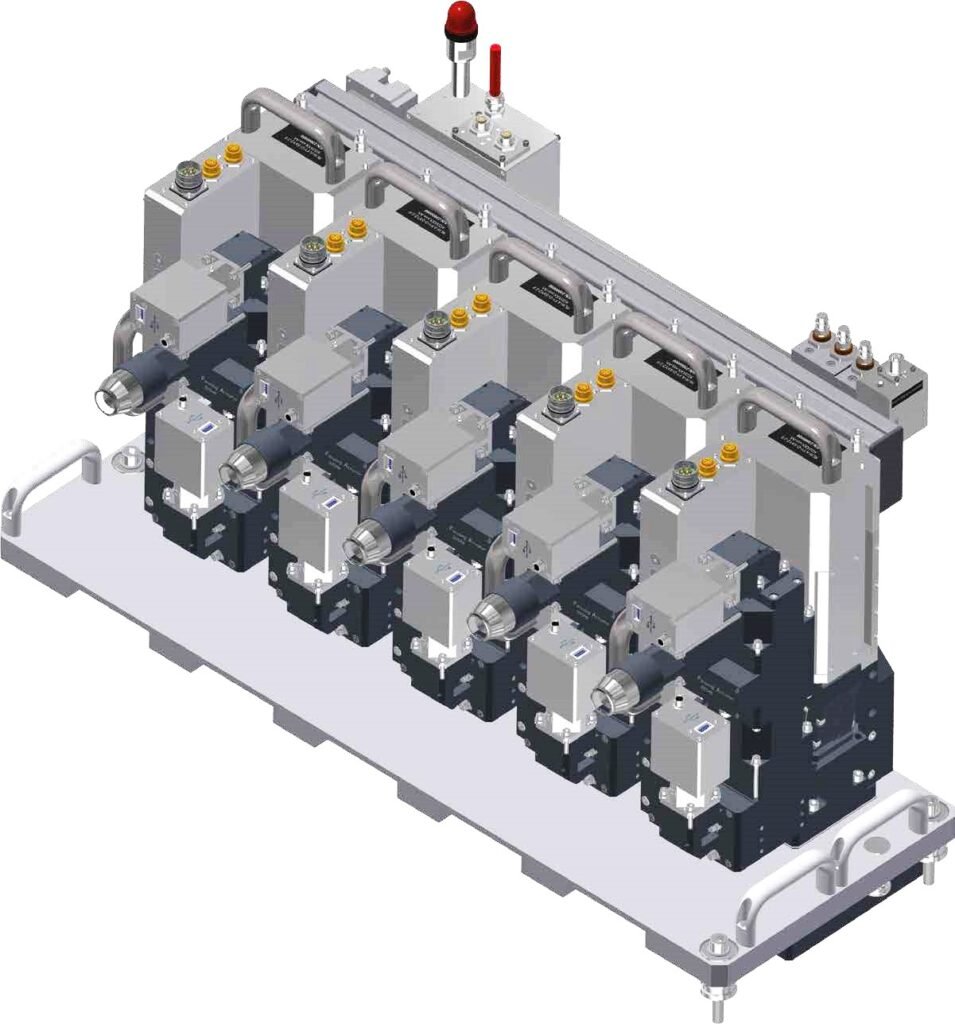
In addition, the requirements for welding speed are high. For example, for a single bipolar plate, welds of up to 4.5 m in total length must be welded; for a cooler plate for batteries, this is up to 100 m. For an electric motor consisting of up to 400 hairpins or battery trays with up to 1,000 battery cells with anode and cathode welding, up to 2,000 welds are required. At the same time, the overall number of parts is increasing with the switch to alternative drives – while the demands on cycle times remain high. In the case of bipolar plates, for example, the goal is to produce one plate per second.
At the same time, the laws of physics set limits for developers. At welding speeds of over 30 m per minute for aluminium processes or >60m/min for welding bipolar plates, the process can no longer be controlled reliably, one risks cracks in the seam.
Faster. Better. Quality Assured
FCW (Fast Component Welding) system technology. This relies on the cost-effective parallelization of laser processes. To achieve this, the developers have integrated complex technology into extremely compact scanner units that can be arranged on a single process-specific application plate. The exact number depends on the desired application. In this way, several components can be processed simultaneously and thus a higher output can be achieved within the same time. Alternatively, the system’s extended scan array allows larger components to be processed in a single step. In an array with four scanner units, the processing time of a component is thus reduced to a quarter. The scanner units are supplied fully calibrated and specially tailored to customer requirements. They can be individually controlled and work in cooperation with each other. This enables simultaneous, independent process control strategies with a high level of quality.
Higher productivity with FCW technology
The scanner units can be set up several times next to each other, both in a row and as a matrix. They thus offer a large scanning field, fast mirror movements, a powerful Z-shifter for height compensation in the workpiece, automatic image recognition, and sophisticated quality monitoring. In the case of bipolar plates and surface coolers for car battery trays, for example, this means a significant increase in the effective welding speed per component, since several seams can be welded simultaneously. The reduction in the angle of inclination that is possible in this process permits a particularly stable process.

One of the most complex components, which accounts for most of the production costs of a battery-powered electric motor, is the stator. The necessary magnetic field is usually generated by so-called hairpins made of copper. Two of each are welded together by laser. Up to now, these have been rotated on a rotary axis until all the hairpins have been welded in turn. This is time-consuming and thus a decisive factor for the productivity of the process.
FCW technology and the simultaneous machining of the component can also make a significant difference in this process, which takes place in a matter of seconds. With the FCW system, a 90° arrangement of a total of four scanner units can be provided for this application. Each unit can approach a segment on the stator, illuminate it homogeneously, detect its position and weld it out. Sophisticated image processing is used to detect all hairpin positions in a single step and direct the laser beam according to the precise welding strategy developed for the customer. The parameters include, for example, the laser power, the shaping of the elliptical motion path or repetitions of the weld path. This means that the stator no longer has to be rotated, regardless of its size.
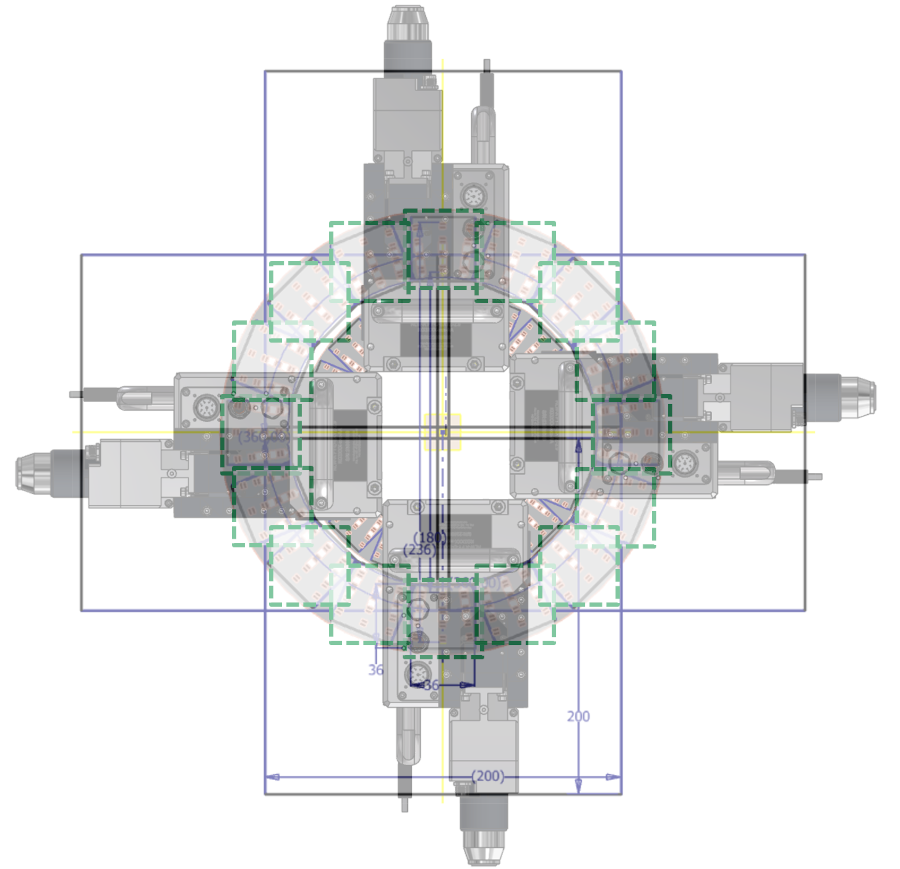
In addition to the applications mentioned, this very compact and lightweight head is also suitable for highly dynamic processes, such as the welding of battery contacts. The head welds battery contacts on the fly at high speed and is moved by a linear axis for this purpose. Depending on the requirements of the application, different laser spots and laser powers can be used. The magnification of the FCW optics range from 2.9 to 6 times. Single mode lasers with fibre diameters of 10 or 14 µm up to multi kW multi-mode lasers with 50 and 100 µm fibres are used.
With FCW system technology, plant and machine manufacturers have a standardized, fully calibrated system for laser welding, which simplifies automation and individual adaptation on site while at the same time shortening work processes.
Author:
Dr. Axel Luft, Scansonic MI GmbH, Managing Director Sales & Marketing