Konrad Lorentz
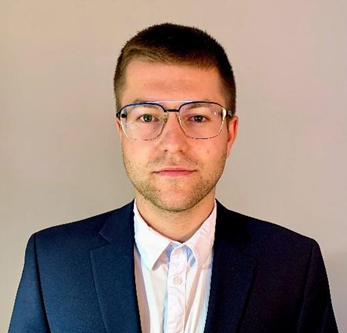
The automotive battery market is growing fast as many brands bring new models into series production in the upcoming years. This rapid rollout accelerates the innovation in battery technology, including battery management semiconductors. This article describes the inner workings of the battery management system (BMS), paying particular attention to the battery junction box (BJB) and shows the advantages that integration can offer in terms of ease of design, safety, and performance.
What is the role of the BMS?
EV batteries can fail for many reasons. Mechanical stress or damage following a crash can puncture the battery pack or, less noticeably, impair individual cells. Electrical stress, such as over-charging, can also lead to safety issues and reduce the overall lifetime of the battery. The BMS assures the highest levels of safety and efficiency.
The BMS comprises three functional modules (Figure 1): BMU (battery management unit), CMU (cell monitoring unit) and BJB (battery junction box). One of the functions of the BMS is to ensure that every Li-ion cell within the battery pack operates within its safe operating area (SOA) defined by voltage, current and temperature. Operating outside the rather tight SOA can result in severe consequences, such as catastrophic failure of the battery or, worse still, thermal runaway.
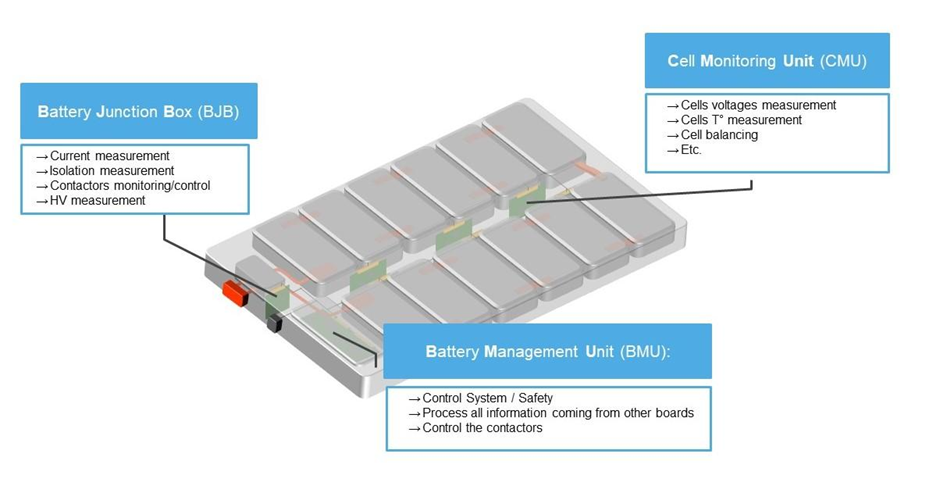
The brain of the BMS is the BMU, where all the precise battery measurements from the CMU and BJB are used to make informed decisions that ensure battery safety and improve performance. Without these measurements, the safety-relevant risks, for example undetected battery overheating, cannot be ruled out, and thus safety and performance are compromised (Figure 2).

Figure 2: The key functions of the BMS.
For OEMs, monitoring the state of health (SoH) of the battery enables them to determine the vehicle’s performance over time and, ultimately, its drivable lifetime. Knowing the battery’s precise state of charge (SoC) gives the driver an accurate range and helps assuage range anxiety.
Another function of the BMS is to balance the charge of the individual cells within the battery pack. Cell balancing takes place during charging as well as while driving, at idle and in standby. Depending on how they are manufactured and their operating lifetime usage, all cells inside each battery module have slightly different remaining charge. When charging is initiated, the CMU measures the voltage of each cell. The balancing current is routed through the resistors on the CMU. The BMU coordinates the balancing function, discharging the highest cells to the lowest cell voltage to get them to the same SoC. When all the cells are balanced, they can reach their maximum SoC upon completion of charging.
Similarly, during driving, each cell inside the battery discharges at a slightly different rate until one cell reaches its minimum charge level. With a more precise cell voltage measurement, the BMU can stop discharging closer to the cell’s safety limit, thereby extracting more energy from the battery. Balancing the cells during charging and driving allows the battery to be operated closer to the cells’ minimum and maximum charge limit, thereby extending the vehicle’s range.
While driving and charging, the contactors are closed, during which time the SoC is monitored via the integration of the current measured in the BJB over time (coulomb counting). This ensures that the cells do not operate outside the SOA as well as providing an accurate remaining range. In standby mode, while the car is stationary, the open-circuit voltage is used to re-calibrate the SoC.
How do batteries recuperate energy?
While driving the EV, the battery either drives the motors or recuperates energy through braking. Recuperation, also known as regenerative braking, extends the range of the EV. As a lot of energy is drawn from or put back into the battery quickly, these power exchanges can lead to significant heat dissipation, increasing the battery cell temperature.
As Li-ion batteries are susceptible to heat, it is crucial to monitor the cell and battery pack temperature and surrounding systems to ensure safe operation, improve performance and longevity. The recuperation power is constrained by the battery system’s electrical and thermal limits; therefore, having accurate data on the battery’s condition optimizes the amount of energy recovered and, in turn, increases the vehicle’s efficiency and range.
Besides the accurate measurement of several temperature points inside the battery, thermal runaway detection via differential pressure monitoring enables the system to react even before it is too late. The pressure rise is caused by the cell(s) venting, which is a pre-stage to auto-propagating thermal runaway. The BMU provides all this precise measurement information, contributing to informed decisions that ensure battery safety and improved performance.
What is the role of the BJB?
One part of the battery system is the BJB, which is the pack-level sensing mechanism of the BMS and the link between the high voltage battery and the drivetrain. It measures and logs the total battery voltage and the current flowing in and out of the battery, allowing a precise calculation of its SOC. This enables precise range calculation, letting the driver know how many kilometres are left in the battery. It also fulfils safety-critical functions like contactor and isolation monitoring as well as overcurrent detection.
The state-of-the-art standalone BJB module has its own intelligence, requiring a microcontroller (MCU) with its dedicated software – this increases BOM cost and local software effort (Figure 3). Due to increasing volume, there is drive in the market for cost reduction at both the hardware and software levels. The BJB solution needs to satisfy ASIL C or D functional safety levels on current and voltage measurements in automotive applications.
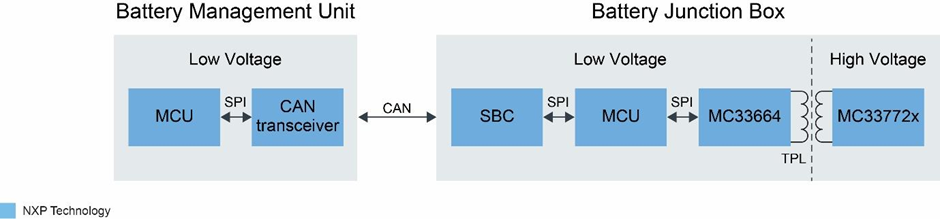
One challenge in high-voltage system communication is isolating the low voltage semiconductors (12V) from the high voltage (400V) battery side. Here, communication with the BMU is traditionally over the CAN bus, but daisy-chaining the BJB via the transformer physical layer (TPL) is an attractive alternative. The TPL interface is designed specifically for BMS, supporting high isolation voltages of up to 2kV. The benefits of such a solution are more robust electromagnetic compatibility (EMC) characteristics, greater high-voltage isolation, better communication speeds, and synchronized measurements, resulting in reduced complexity associated with local software and lower BOM cost.
Communication in the functional safety context
Functionally safe communication can be achieved using a grey channel approach. The grey channel is an abstract term referring to the safe and secure transfer through a neither intrinsically safe nor secure channel. Although it cannot be assigned an ASIL rating, it is considered quality managed (QM) rated, which is the lowest level of safety. Therefore, the grey channel allows the use of QM rated devices to establish an ASIL-rated communication path. To achieve an ASIL rating at the system level, you need to ensure no data manipulation throughout the communication path. Data is secured on the origin and decoded at the destination. What happens can be ignored during the data’s journey because you can always detect errors since the data was secured at the origin and not manipulated.
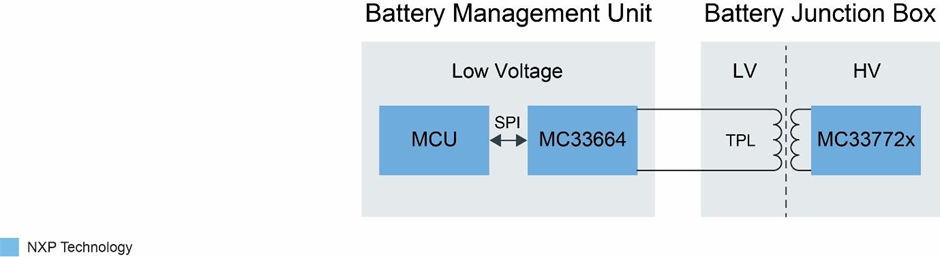
Using the grey channel approach, the intelligence can be moved from the BJB to the BMU without spending additional safety efforts on communication devices (Figure 4). The information is digitally transmitted through the TPL to the MCU for processing. The role of the MCU is to unpack the TPL frames and ensure data integrity. The main benefit of the grey channel is to reduce the complexity of the system in terms of hardware design and safety.
Features required in the BJB
Newly emerging semiconductors that specifically target the BJB integrate all the required functions in one single device. The MC33772C from NXP, for example, provides precise current sensing from milliamps to kiloamps with coulomb counting (Figure 5).
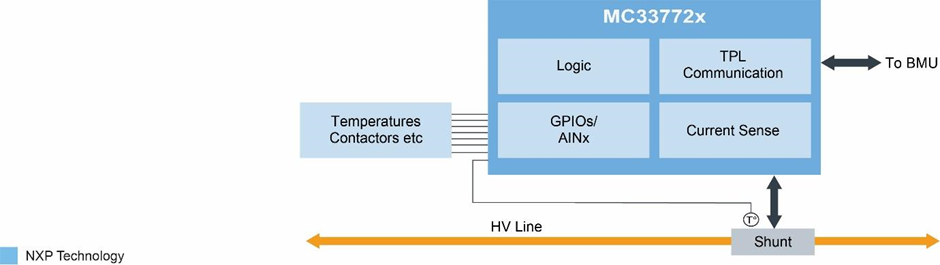
The device offers multiple advanced voltage and temperature measurement functions, and the embedded balancing transistors with diagnostics simplify the BJB application. It also supports standard SPI and isolated daisy chain communication to an MCU to process and control up to 63 nodes. Additional diagnostics and functional safety features include detecting internal and external faults like open lines, shorts, and leakages. The robust AEC Q-100 compliant device is hot-pluggable and supports ISO 26262 with up to ASIL D capability.
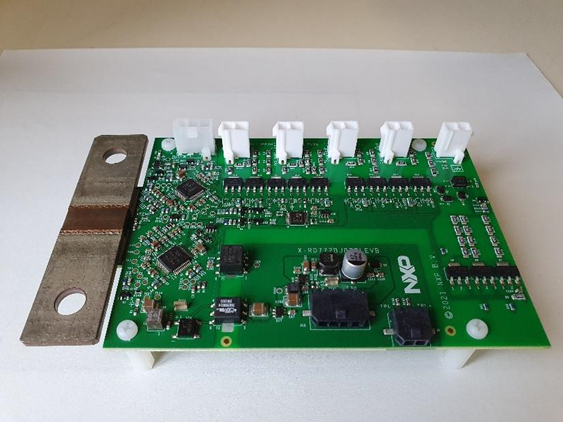
The MC33772C evaluation board and production-ready reference design features a highly accurate shunt solution that enables developers to reduce both time to market and BOM cost. (Figure 6).
Conclusion
In automotive applications, these safety measurements must comply with the functional safety classifications defined in ISO 26262. Coulomb-counting is enabled directly on the chip by integrating the precise current values over time without MCU interaction. Proprietary interfaces offer high isolation voltages and maintain the functional safety level of the communication by using a grey channel approach. This way, a software-free ASIL BJB is enabled. This simplification in design reduces time-to-market and the associated development costs at Tier 1s and OEMs while improving range, safety, and battery lifetime, accelerating the transition to CO₂-emission free transportation.
Konrad Lorentz B.Eng., Product Marketing – Battery Management Systems, Advanced Analog, Drivers & Energy Systems, NXP