Material Solutions for 800 Volt eMotors, SiC Inverters, and eDrive Systems
Brian Baleno, DeeDee Smith, Nicolas Batailley, Luigi Marino, Victoria Lee, Qasim Shaikh, Stefano Montani, Benoit Devaux, Gilles Divoux
Many new battery electric vehicles (BEV) that are in the market today utilize electric powertrain platforms (Battery, eMotor/eDrive, and Power Electronics) that are built around 400-volt systems. The transition to 800-volt systems (several > 800 volts) is well underway as OEMs work to improve efficiency, enable faster charging times, and increase performance. All of these key benefits lend themselves to improvements in range thereby addressing one of BEV consumers’ biggest concerns.
The transition to 800-volt systems does not come without challenges. A balance needs to be struck between improving the performance of the eMotor and power electronics (Silicone carbide inverter) while optimizing the size and weight of the battery.
eMotors
A large number of 800-volt eMotors are focused on permanent magnet synchronous motors (PMSM) technology. eMotor designer engineers are actively seeking higher performance materials that allow for optimized copper slot fill, improved thermal conductivity or reduced the motor temperature, and decreased weight which is achieved by running at higher speeds. Each of these factors contributes to the overall efficiency and performance density of the eMotor.
The first generation of 400-volt eMotors commonly used iso-cyanate polyamide imide (ICN-PAI) for the magnet wire insulation and paper or paper laminates for the secondary insulation (slot liners). Solvay developed PEEK film slot liners in order to increase copper slot fill in the stator. PEEK allows for thinner insulation systems (50 microns) than can be achieved with paper or paper laminates (NKN). There are other benefits of PEEK over NKN as well, including better durability, reduced eMotor temperature achieved by having better thermal conductivity, and also an easier and cleaner manufacturing process.
Durability can be measured by evaluating the materials’ ability to withstand corona discharge. A material with better corona discharge performance has the potential to avoid damage to the electrical insulation which in turn impacts the durability and life of eMotor. The chart below Figure 1 below compares the lifetime of PEEK to Nomex and Nomex laminate materials under corona discharge conditions.
Figure 1: Ajedium™ PEEK film slot liners Corona Discharge Lifetime
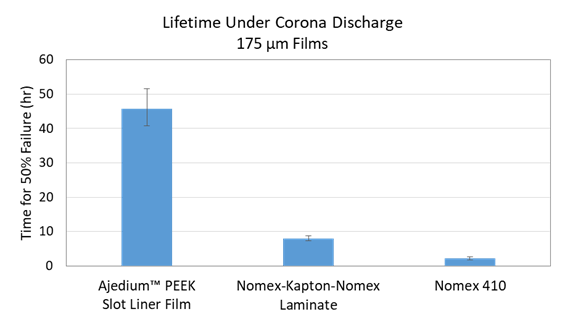
As shown above, the PEEK slot liners provide 7X the corona discharge resistance compared to Nomex and Nomex laminates. The other significant difference between PEEK and paper insulation is the thermal conductivity which is related to both the material properties as well as the material thickness that can be utilized. Figure 2 gives a comparison of the thermal conductivity properties of PEEK to paper insulation systems.
Figure 2: Thermal Conductivity Comparison

The 26 % improvement in thermal conductivity of PEEK versus Nomex at 175 microns combined with the potential to use even thinner PEEK slot liners (125 and 50 micron) leads to potential reductions in slot stator temperature which can range from 3 ℃to 13 ℃. This is highlighted in Figure 3 below.
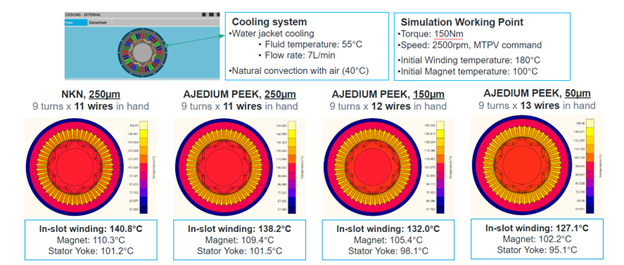
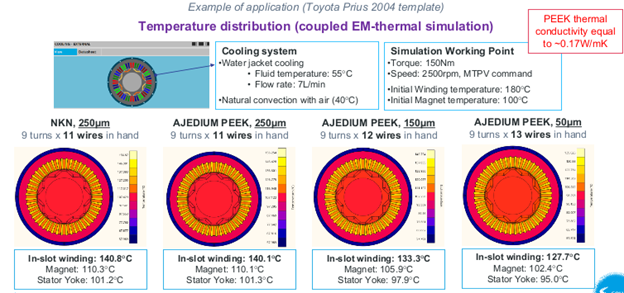
Figure 3: Thermal Improvement PEEK vs. NKN
PEEK magnet wire and PEEK slot liners are enabling eMotors to operate at higher voltages while also looking to reduce the size of the eMotor. Extruded PEEK magnet wire and hairpin winding technology allow for a 10 % improvement in copper fill factor by increasing the amount of copper that can fill the stator slot. This is shown below in Figure 4.
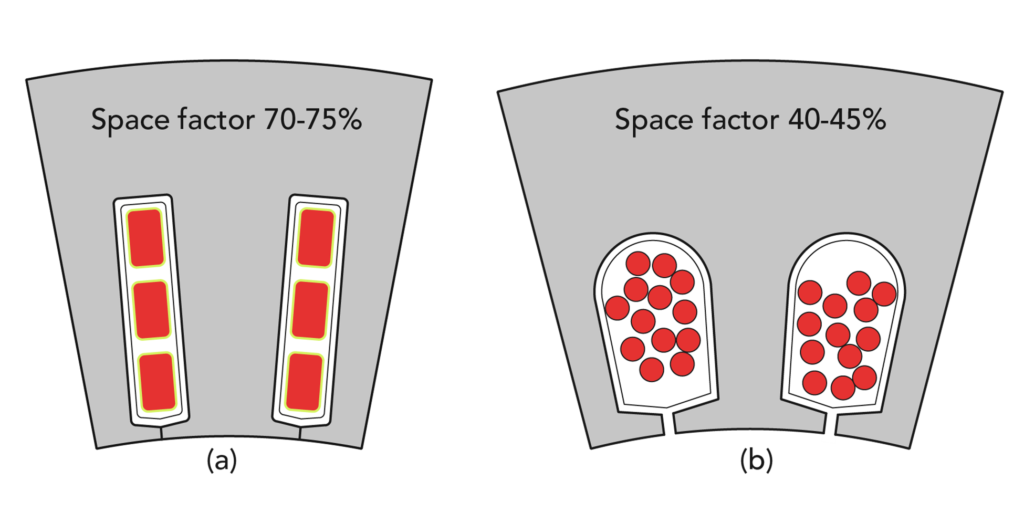
Extrusion technology offers multiple advantages over the traditional enamel process used for ICN-PAI magnet wire. The PEEK extrusion process provides for better concentric control of the insulation thickness, especially around the edges of rectangular copper wire. Additionally, because extrusion is done in a single step instead of multiple passes for enameling, there are less defects which gives an improved safety factor of insulation failure.
Solvay’s KetaSpire® PEEK has been commercial in eMotor magnet wire since 2016. Figures 5 and 6 below detail key criteria such as thermal rating and dielectric constant which contribute to achieving the desired partial discharge inception voltage (PDIV) of the eMotor.
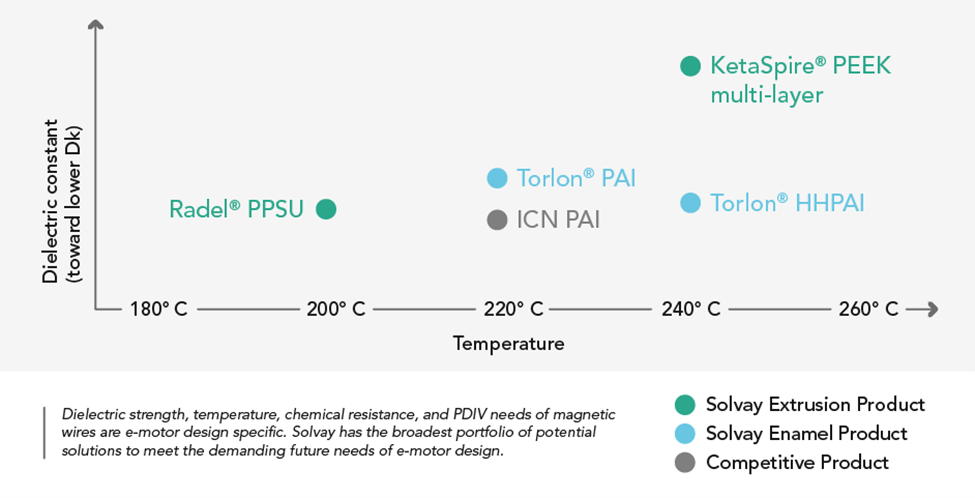
Figure 6: PEEK electric properties
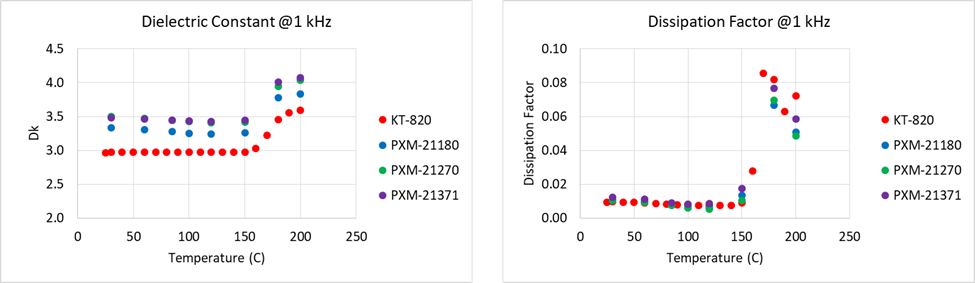
Silicone Carbide (SiC) Inverters
The inverters used in 400 Volts were based on insulated gate bi-polar transistor (IGBT) technology. This technology was widely adopted but in order to enable 800 Volt systems, a more advanced inverter is required. The predominant 800-volt system inverters use SiC mosfets instead of IGBT. Although more expensive than IGBT, the SiC technology increases the power, allows for faster switching frequency, and also provides the opportunity to reduce the overall weight of the system.
Like 800-volt eMotors, the performance requirements for materials used in SiC inverters are more demanding as they operate at higher temperatures. This requires material solutions that can provide better thermal performance, retention of electrical properties at higher temperatures, and resistance to moisture. Additionally, many of the inverter components have a safety requirement for flame retardancy (VO rating). Some of the main components that require higher performing materials are power modules, capacitors, and AC and DC busbars.
Power module housing typically have a range of high temperature technical requirements which include comparative tracking resistance (CTI), relative temperature index (RTI), and flammability resistance. Additionally, these materials must be compatible with electronic chips and manufacturing processes.
Solvay designed both PPA and PPS solutions for power electronics or inverter components. Figure 7 below lists the specific grades of PPA and PPS that were designed for power module housings, capacitor supports, high voltage connectors, and busbars.
Figure 7: Power Module High Performance Polymers with Thermal & Electrical Properties
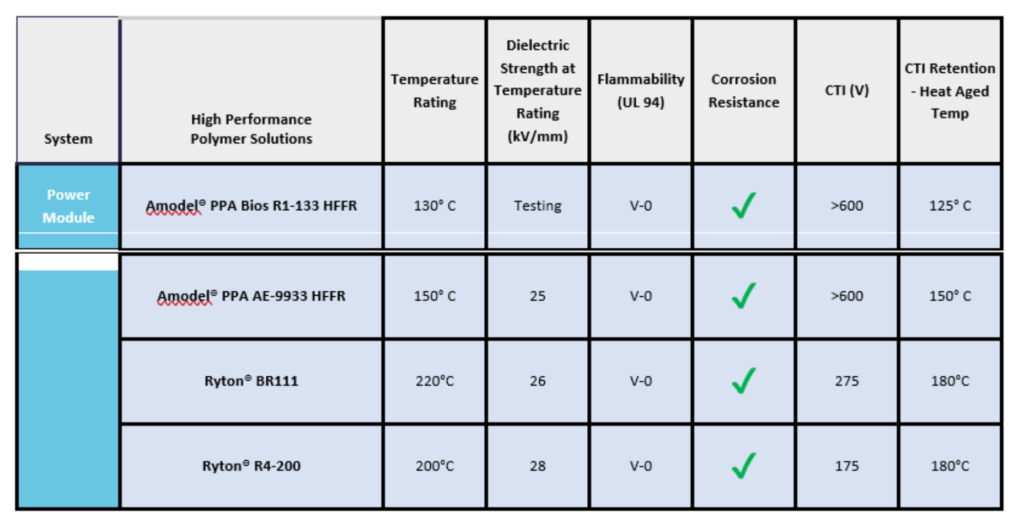
AC and DC busbars have additional requirements including the ability to endure thermal cycling or operate over a broad temperature range which includes -40 C up to 180 C. PPA and PPS have different coefficients of thermal expansion which needs to be accounted for in the busbar design since a failure can occur with insulation loss or short circuiting. Figures 8 below highlights the thermal shock performance of Solvay’s PPA and PPS busbar materials.
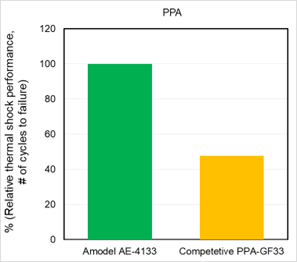
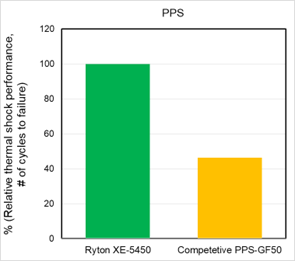
Figure 8: Thermal Shock Cycle Testing: 150 cycles (-40 C for 1 hour followed by 150 C for 1 hour)
eDrive & eAxle
Next generation eDrive systems are being designed to operate at speeds of 20,000 rpms and higher. Some designs utilize planetary gear sets. Engineers are seeking materials that can enable space savings and reduce NVH (noise, vibration, and harshness) in an effort to improve the overall efficiency and performance of the BEV drivetrain. One of the solutions to creating space savings in a planetary gearbox is to use polymeric thrust bearings. Friction and wear resistance plays a critical role in identifying the optimal material. Commonly used materials for gearbox bearings include PAI and PEEK. Figure 8 below shows the wear data of Torlon® PAI and Figure 9 highlights the design benefits of polymeric bearing including elimination of secondary machining, the incorporation of oil flow channels for cooling, and snap-fit features for easier assembly.
Figure 8: Wear data as function of temperature and time

Figure 9: eDrive System Component Design Freedom- Oil Flow Channels Built into part geometry
The use of polymer bearing cages also benefits design engineers by providing cost savings, weight reduction, corrosion resistance, and reducing NVH. Historically, materials like PA66 have been used in bearing cages but with increasing temperature requirements, speeds, and chemical resistance, engineers are evaluating PPA and PEEK. Key material selection criteria include tensile stress at break, tensile strength retention in ATF (automatic transmission fluid) at 150 ℃, and weld line strength. Figures 10, 11, and 12 respectively highlight the differences between PA66, PA46, PPA, and PEEK across a range of operating conditions.
Figure 10: Tensile Stress at Break comparing 30% filled PA66, Amodel® Bios PPA, KetaSpire® PEEK

Figure 11: Tensile Strength after 3500 hrs Toyota ATF exposure on Glass Filled Materials
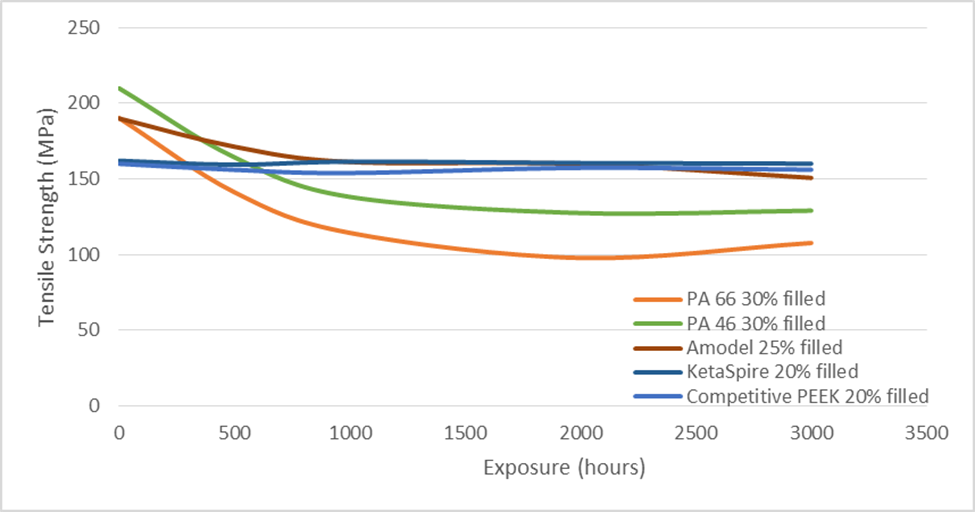
Figure 12: Weldline strength for common bearing cage materialshttps://www.solvay.com/en/solutions-market/automotive
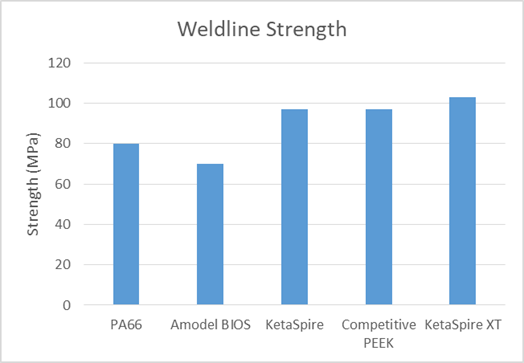
The next generation BEVs are starting to design systems based on 800 volts or higher. eMotors and SiC inverters based on 800 Volts systems will require material solutions that can provide better performance at higher temperatures while retaining electrical properties at these elevated temperatures. Additionally, eDrive systems that utilize planetary gear sets and bearing cages also will need higher performance specialty polymers. Solvay has developed insulation solutions that include PEEK magnet wire and PEEK slot liners to further enable higher voltage PMSM. In order to enable SiC inverters, Solvay has designed specific PPA and PPS solutions for SiC components including power module housings, capacitor supports, and AC and DC busbars. Beyond eMotors and inverters, Solvay is working to introduce new PEEK, PAI, and PPA materials solutions for polymeric bearings and bearing cages.
Brian Baleno, DeeDee Smith, Nicolas Batailley, Luigi Marino, Victoria Lee, Qasim Shaikh, Stefano Montani, Benoit Devaux, Gilles Divoux all from Solvay