A pioneering innovative technology to lower production costs for EV batteries
E-mobility is one of the most discussed issues of our time as it can solve many of the occurring world problems like environment pollution. Still, electric vehicles remain a niche market. The main obstacles to boost an e-mobility revolution lie in the high costs for electric vehicles on the market and underdeveloped charging infrastructure. The high price of electric vehicles is mainly determined by the power unit: the Li-ion battery cells.

The conventional production process of Li-ion pouch cells suffers from a number of disadvantages leading to these extraordinary prices. The key factor is the material costs, especially for electrode materials. Indeed, the expense for the pouch foil is just a fraction in the total costs. At the same time up to one third of the pouch foil is used as a gas bag for collecting formation gas. Finally, the gas bag will be cut off after sealing and disposed as hazardous waste leading to unnecessary expenses and extensive disposal efforts. The new sealed seam is also contaminated which influences the life time of the battery cell. In addition, large dry rooms necessitate high investment costs. High cell prices are also caused by high investment and operating costs needed for a big dry room. The open Li-ion battery cell needs to be handled in a dry atmosphere due to the electrode materials and the electrolyte´s sensitivity to moisture. Long process times are another expense factor.
After extensive research one company has developed a new and efficient solution to overcome these unfavourable issues
In the town of Coswig northwest of Dresden Germany, IP PowerSystems GmbH develops processes and designs machines which offer efficient and ecologically advantageous solutions for the production of lithium-ion battery cells.
Here, Ralf Hock, managing director of IP Power Systems, explains a pioneering technology that he is convinced will lower costs for EV battery production
As a result of the company’s extensive R&D efforts, an innovative technology arose from a project with the aim of finding an efficient and ecological alternative to the conventional production of Li-ion battery cells.


The result of which enables electrolyte filling at ambient atmosphere without a dry room, a process which has not been possible until now. The novel, patent-pending technology also includes a new production process starting with the cell assembly and final sealing before the filling step.
The assembly of the cell components – i.e. the electrode-separator-stack with welded-on tabs and the pouch foil – is completed similar to conventional production. Additionally, closed filling plugs – so called ports – are integrated within the seam of the pouch cell for the sealing process, which can be performed in a dry microenvironment. The sealing machine executes the complete and hermetical sealing of the cell. Due to this innovative technology no special dry/clean atmosphere is needed for the next steps in process.
Subsequently, the hermetically sealed, dry pouch cell is transported to the filling machine under ambient atmosphere. The number and position of ports are adapted to the required cell size and electrolyte quantity. Access into the cell is realised by penetration of one or multiple ports by dosing needles. The needles are designed to draw vacuum or inject electrolyte, enabling a wide range of filling strategies for enhanced and faster electrode wetting. Therefore, one of the bottleneck steps can be significantly improved.
The wetting of the electrode surface, especially wetting of the large pore surface of the chemically active electrode material, is one of the crucial bottleneck steps and can take up to 48 h. This process can be accelerated by adjustment of temperature, pressure, etc. Still, the electrolyte will need a significant amount of time to reach the pores.
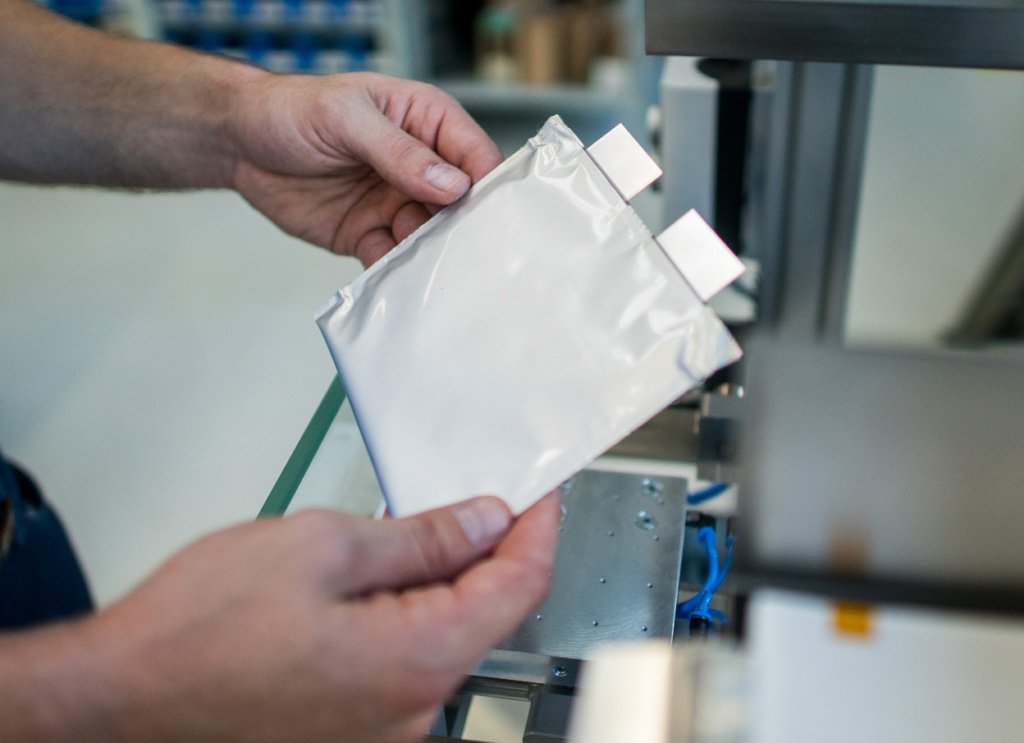

The novel technology of IP PowerSystems GmbH deals with these parameters. The filling machine is able to heat the electrolyte to a defined temperature for a faster wetting. Besides, the aforementioned needles are specially designed which ebalbles vacuumising and filling of the cell with the same needle. Due to the flexibility in filling, the wetting of the electrode surface with electrolyte can be improved.
In the conventional production process the filling is typically done in a vacuum chamber. Such is not required in the filling machine of IP PowerSystems GmbH allowing for a plain machine design and low investment. Here, the filling under standard pressure facilitates a pressure difference between inside (vacuum) and outside (standard pressure) of the cell.
This technology provides the opportunity to reduce process time and hence production costs. Directly after filling, the ports are sealed off by sealing clamp jaws. Thus, the cell is hermetically closed at any time.
After activation/formation, the cell is transported to the degassing machine. This machine utilises port and dosing needles to extract the formation gas and to generate the desired vacuum inside the cell. This eliminates the need for conventionally used gas bags for the collection of formation gas.
These gas bags are typically contaminated with electrolyte resulting in high disposing costs as hazardous waste. In addition, the novel technology minimizes contaminated sealing seam, thus reducing negative effects on the battery´s lifetime.
In conclusion, the innovative technology bears a lot of advantages, especially for mass production of Li-ion pouch cells. The filling at ambient atmosphere results in considerably reduced investment and operating expenses, eliminating requirement for dry rooms. Due to the elimination of the gas bag, no excessive amount of pouch foil is required, and cost as well as effort for the disposal is reduced.
Accessibility of different filling strategies allows for the acceleration of the wetting procedure
Furthermore, the process flexibility is granted for all required process conditions. The requirements and conditions were determined in collaboration with OEMs, manufacturers for niche products and research institutes. This also includes the format flexibility. All existing pouch cell formats can be
produced on the machines based on this innovative technology. The company provides equipment for cell production from sample quantity up to mass production covering niche applications as well as mass applications.
“Thanks to the company’s new technologies and its special expertise we are able to play a big part in our customers’ success. This innovative technology “Method for producing electrolyte pouch cells for electric battery arrangements, corresponding device and electrolyte pouch cells“, is filed for patent with international application number WO 2016/198145 A1.
“We are convinced, the use of this pioneering technology will help pave the way towards the e-mobility revolution “ Hock concluded.