EV Li-ion Battery Separator technology
Dr. Graeme Fraser-Bell
As much as there are Vintage years in Wine there are vintage years in history with 2007 being one such transformative year. Facebook exploded into the public space from its confines within a college campus, a micro-blogging company called Twitter spun-off on its own separate platform, Google launched Android after buying YouTube the year earlier, Airbnb was conceived in an apartment in San Francisco, AT&T invested in software enabled networks to support the exclusive launch of Apple’s iPhone and Intel introduced non-silicon materials into its microchips for the first time.
All of these developments led to 2007 being the tipping point for many of the ubiquitous technologies we take for granted today.
In the same way that 2007 represents one of the greatest steps forward in our technological history, in decades to come will we look back at 2020, of course as the ‘lost-year’ of Covid-19, but perhaps more lastingly as the tipping point for the e-mobility revolution?
In 2020, Norway set a target of 100% EV by 2025. The UK brought forward the ban on sales of new ICE’s to 2030. Tesla became the most valuable OEM. The EU imposed a 95g/km of CO2 limit on OEM’s, forcing an acceleration in transformation of the European OEM fleet. OEM’s announced plans to launch > 200 new EV models. SPAC’s exploded on US exchanges with 248 listings raising $83bn, near double the $47bn raised in the previous 10 years combined. The $100/kWh target for cost parity with ICE’s became recognised as a viable short-term target and President Biden was elected 46th President of the US resulting in a $2 trillion environmental stimulus package.
The impacts of these seismic macro-economic effects have been felt in all sectors of the EV downstream supply-chain, from Lithium battery manufacturers, electric motor producers, electrode material, electrolyte and separator material suppliers all the way to Lithium, Cobalt and Nickel miners.
At the International battery Seminar & Exhibit in July, 2020, Avicenne Energy presented data that showed demand for Lithium-battery separators had increased from 0.4Bn m2 in 2010 to 3.6Bn m2 in 2020 and is projected to triple to 11.3Bn m2 by 2030. To put that in context, that’s the equivalent of building greater than 75 additional ENTEK Membrane Lithium-battery separator facilities between now and 2030.



Fig 1 – ENTEK Membranes vertically integrated plastic equipment processing capabilities
A separator needs to maintain a robust physical separation between the Anode and cathode active materials, be as thin and porous as possible to allow the free flow of electrolyte ions through its structure, exhibit high strength for fault free high-speed assembly and dendrite protection as well as possess high voltage oxidation resistance and high thermal integrity.
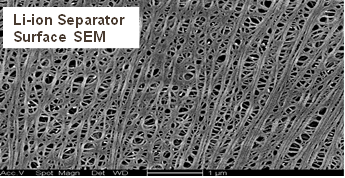
Fig 2 – SEM of ENTEK Membranes ‘Wet-process’ Lithium-ion battery separator micro-structure
Whilst the base microporous polyolefin separator is suitable for use in consumer electronic devices such as mobile phones, laptops, tablets, etc. it is only part of the equation for EV Lithium-ion battery applications. High energy density, stringent safety features, and extended cycle life requirements necessitate a protective ceramic coating on the base film for use in EV applications.

Fig 3 – SEM of ENTEK Membranes double-side coated nano-structured Lithium-ion battery separator composites
Balancing these multi-functional attributes requires multiple trade-offs and optimisations during the manufacture of the Lithium-ion separator composite and is the equivalent of balancing a chemical, engineering and plastics manufacturing process in one operation.
ENTEK Membranes is the only ‘Wet-process’ Lithium-ion battery separator producer in the USA and as such is ideally positioned to meet the IP robust, supply-chain resilience and on-shored regional requirements of the burgeoning US Lithium battery producers.
The innovative and proprietary Lithium-ion ‘Wet-process’ base film process allows for the production of commercial scale volumes of base film as thin as 5um with capability down to as thin as 3.5um for use in portable electronics. When combined with ENTEK’s patented in-house ceramic coating technology (US Patent #9,847,519) the process enables the production of double-side coated, Lithium-ion battery separator nano-composites for maximum durability with exceptionally low thermal shrinkage of < 5% at 180oC for 30 minutes.
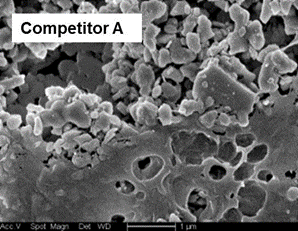


Fig 4 – Surface SEM’s highlighting the nano-structured nature of ENTEK Membranes novel ceramic coated Lithium-ion battery separators
This novel approach for ceramic coated separator development creates a unique coating morphology that facilitates lower coating mass and thickness to achieve high temperature dimensional stability which is remarkably above the melting temperature of the base material. Additionally, the nanoparticle approach allows for higher porosity and smaller pores within the coating layer

Fig 5 – Threshold coating required to reach high temperature dimensional stability when using nanoparticle formulations versus conventional coatings

Fig 6 – Exceptional thermal integrity of the ENTEK Membranes nano-structured ceramic coated Lithium-ion battery separators exhibiting < 5% shrinkage at 200oC
A unique capability of the proprietary ENTEK separator process is the ability to produce Lithium battery separator materials with ceramics intimately mixed within the structure of the base film separator. Such separators provide increased porosity, reduce impedance and increased wettability of benefit for larger ESS battery formats. Such separators are increasingly being manipulated by various OEM’s and Tier-1 Lithium battery suppliers for application in Lithium-metal batteries or quasi-solid-state batteries.

Fig 7 – SEM of ENTEK Membranes unique ceramic filled separator
In 2020 ENTEK Membranes submitted a proposal to the UK’s Advanced Propulsion Centre (APC) as part of the UK’s £1bn Automotive Transformation Fund (ATF) for investment in a full-scale Lithium-ion battery separator facility in the UK, alongside its existing battery separator operation in Newcastle-upon-Tyne. If investment plans are approved ENTEK Membranes will become the UK’s first EV Lithium-ion battery separator producer and will allow the on-shoring and regionalisation of ENTEK’s proprietary separator technology throughout Europe.

Fig 8 – ENTEK’s battery separator operation in Newcastle-upon-Tyne, UK
“Our proprietary mix of battery separator base film production combined with its innovations in nano-structured ceramic coatings allows us to produce IP robust, ultra-thin, low impedance and highly durable separator composites for Lithium-ion, Lithium-primary and next generation Lithium-metal batteries as well as their Sodium variants” concluded Dr. Rick Pekala, CTO, ENTEK Membranes LLC
Dr. Graeme Fraser-Bell VP – Li Sales & Market Development Entek