Enhancements Deliver Positive Customer Benefits in Metal Welding Applications
The pace of change in manufacturing today is such that the technologies used in many production processes must themselves continually evolve to meet the growing demands for increased performance, superior quality standards, and greater levels of digitisation and connectivity.

The variety of different components which together make up the harnesses and terminals used within the EV power train requires a powerful yet highly flexible production solution, capable of rapid deployment to meet current needs, but with the capability of being quickly re-configured for new product variants.
The principles of forward thinking, and the innovative design concepts behind the Telso®Terminal TT7 platform, have enabled the introduction of a wide range of new and enhanced technological features which expand the capability of the system, whilst at the same time providing the digital control and connectivity required to meet the dynamic requirements of the EV component manufacturing sector.
Boosting Productivity And Flexibility
The clever design of the system means that the vibrating components remain in place within the TT7 system at all times, making the replacement of the sonotrode a simple process which can be completed in under 5 minutes. Fan cooling for the converters is standard and temperature monitoring is also available as an option if required.

Telsonic’s unique torsional PowerWheel® technology is an integral part of the Telso®Terminal TT7 platform
The new Telso®Terminal TT7 system is capable of producing welds of up to 200mm2. Sonotrodes with 4 welding surfaces are available, providing up to 19 mm of weld width, or with 2 welding surfaces for weld widths of 20 mm and greater. The cable diameter and terminal height can be pre-defined, and an option is available which will automatically detect incorrectly inserted cables and terminals according to their height and diameter.
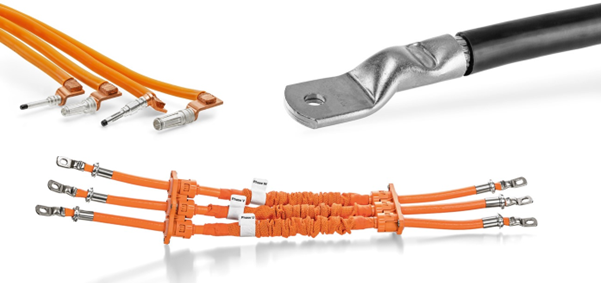
The Telso®Terminal TT7 platform is capable of producing a wide range of cable and terminal assemblies
The system offers a highly flexible welding process for a wide range of cable and terminal assemblies, with a welding force of up to 7,300N, power up to 14.4kW, various different welding and trigger modes, plus multi-stage amplitude and force profiles. Process monitoring is also available for both the terminal and the cable. Quick change tooling is also available for the component clamping jaws which also helps speed up the transition from one product to the next.
The temperature of both the sonotrode and the component clamping jaws can be controlled by water cooling or heating as required, with the desired temperature configurable in software and readable in a data log file. Should the temperature exceed the pre-set threshold, production will be inhibited, protecting both the sonotrode and clamp tooling. The sonotrode is also replaceable without removing the cooling system. These combined features mean that the new Telso®Terminal TT7 system is not only easier to use, faster to set up and change over, but capable of processing a much wider range of cable and terminal assemblies with the highest levels of process control and consistency.
Innovative Digital Control Technology
Using this innovative and intuitive control technology users become productive more quickly. Packed with useful features, Telso®Flex provides operators with instructions and a step-by-step guide during application set up or product changeover. This includes the display of images and information about each of the components to be processed, including colour, dimensions, and part number. User and rights management mean that only authorised personnel are able to make changes to the system.

Telso®Flex also facilitates automatic system configuration, based upon information contained in a unique Parameter Setting Sheet (PSS), supplied with converters, torsion transducers, boosters and sonotrodes. A QR code attached to the PSS contains the article number, serial number, and relevant production data. Once scanned into the system, the digital platform is automatically configured with the production data contained in the QR code, avoiding errors which can sometimes occur with manual input. All tool changes are recorded, and the system performs automatic self-test routines to ensure compliance with the anticipated configuration.
Additional features include a material database for cables and terminals, additional sensors for enhanced quality monitoring, maintenance support functions plus remote access for in-house support.
When in production, the current application is displayed along with a description and images. Welding results and their limits are shown as values and as different colored bars designating status as either within the limits, close to the limits, or outside of the pre-set limits. The welding curves for power, force and displacement are also displayed, and as a option, together with the limit values and additional process phases. Also displayed are the number of parts which have already been produced, identified as good and defective parts, together with the piece part count for the current production run.
Telsonic’s Telso®CON interface enables integration with customers MES systems through a series of standardised and customer-specific data interfaces such as OPC UA (Open Platform Communications Unified Architecture), FTP Client, Shared Network and Socket Server functions.
A Future-Proofed Investment

The Telso®Flex software is designed to be easily customisable to meet individual customers needs. This is especially useful where users may need to re-configure the system to suit the manufacture of new part types, or where they wish to add particular features or functionality. For example, pre-installed options can be activated and evaluated at any time and full operating licenses can easily be ordered using the built in kiosk function. The system also enables data to be saved to local directories, network servers, FTP servers or manually to a USB stick.
The inherent flexibility of the new feature packed Telso®Terminal TT7 system, combined with the power of the MAG Generator range and Telso®Flex software, means that users are not only able to specify a system to meet the needs of today, but can rest assured that their investment is future-proofed and will deliver the functionality, productivity and quality needed for their next generation product ranges.
Christian Huber Market Manager Ultrasonic Metal Welding Telsonic AG