Battery testing: what’s next?
Christopher Giehl and Andre Braun
Testing of battery raw materials and semi-finished products takes battery quality, processing, scaling and safety to the next level.
Common battery test procedures involve a range of electrical, mechanical, environmental, and safety evaluations to determine performance, durability, and resilience of batteries under various conditions. Well-known tests include capacity and cycle life assessments, vibration and shock resistance, temperature and humidity effects, and safety protocols like overcharge, short circuit, and thermal abuse responses, among others. However, final product properties cannot directly elucidate the effect of raw material properties and processing parameters.
Regardless of whether fossil fuel and nuclear power generation capacities will increase or the long-term rise of renewables dominates, the cars of the future will be powered by electricity. Operation of batteries is generally considered safe, but incidents may result in serious scenarios, that can hardly be predicted. Electric car battery fire, airplane battery problems as well as tablet fires and explosions received public attention and are a reminder that battery safety is a prerequisite for the energy transition. Even though these incidents are rare, they have a large media impact and with the expected scaling of electric cars production even a one-in-a-million might damage public trust in the transportation revolution. How can such accidents be avoided? For this, we need to start from scratch, long before performance, cycle life and environmental stability of batteries are assessed.
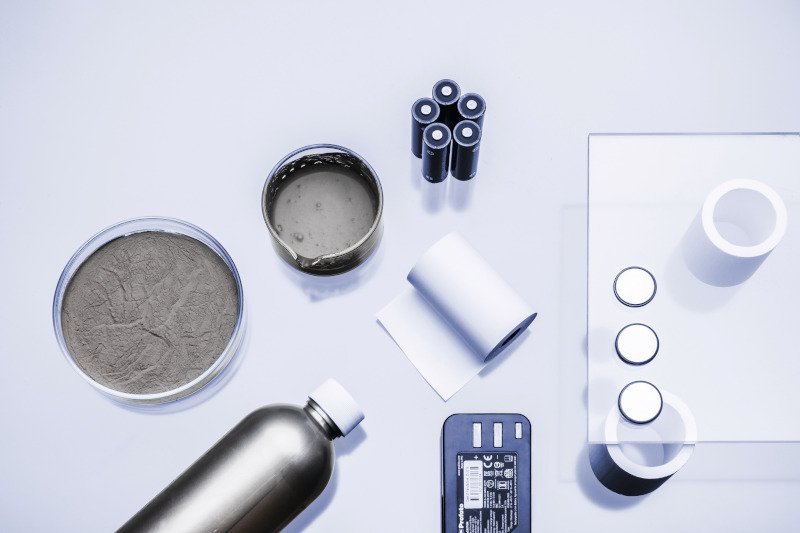

The battery production process
The main ingredients of batteries are active materials of various chemistries, binders, additives and solvents, starting off with dry mixing of these powder raw materials. In the prevalent process for producing battery cells, the powder mixture and the solvent are subsequently mixed to form a homogeneous slurry with target properties of viscosity, particle size (distribution). This slurry is coated on a transfer foil substrate and depending on the slurry properties, the processing speed and other factors, various coating tools can be used. The most common ones are blade coating, slot die coating and spraying. After subsequent drying and calendaring, electrodes, separators and current collectors are stacked, welded and packaged. After filling in the liquid electrolyte, the battery production is finished with formatting and final sealing.
Even though testing is currently focused on final product properties, recent studies increase the emphasis on the importance of characterizing raw materials and semi-finished products, as well as processes (Fig. 1 above left).
Problems & solutions
At the heart of a battery, electrodes, anodes and cathodes, represent crucial building blocks fundamentally responsible for the final battery performance. Quality problems may e. g. result from insufficient knowledge about raw materials and their properties. Possible consequences are decreased capacities, non-ideal charging/discharging behavior and an increased risk for battery fires. The latter often results from imperfections that can be reduced by optimized and standardized processes as well as comprehensive incoming goods inspection. Monitoring of constant quality and material properties not only ensures the targeted quality standards, but also enables faster process speed, upscaling and automation.
Efficient powder handling, powder storage behavior and mixing properties ensure uniform coatings by involving powder rheological tests of active materials as well particle shape and size (distribution) characterization, among others. Rheological tests on visco-elastic slurries help optimizing the flow behavior as well as time-dependent structural recovery (i.e. thixotropy). Using such knowledge, slurry homogeneity, wet layer thickness, leveling and edge shapes of coated slurries can be controlled.
A means to handle mechanical stress or even abuse is to improve the resistance against impact using modified, non-Newtonian electrolytes with shear-thickening flow behavior. Here, e. g. added silica particles induce increasing viscosity of the electrolyte during impact thereby avoiding destructive deformation of solid components. Furthermore, the development of separators and current collectors with improved damping capabilities (flexibility), higher thermal stability and higher electrolyte uptake (for separators) is essential for enhancing safety as well as performance of batteries. Composite current collectors are both side metal-coated polymer foils. Such materials require additional characterization regarding mechanical and thermal stability, e. g. regarding extensional properties and glass transition temperature.
Both the flow behavior of powder, electrolytes, slurries and the mechanical and thermal properties of current collectors and separators can be characterized with rotational rheometers. To date, many such rheometers are used as quality control devices to characterize the flow behavior, e. g. viscosity, of liquid electrolytes, but also the flow properties of powders and the visco-elastic behavior of slurries for formulation and process development, e.g. the coating process onto the current collector. With rheometers, also properties like electrical conductivity of electrolytes and slurries can be investigated, even simultaneously with rheological measurements. Characterization of films, like (coated) current collectors and separators, is an emerging field and can be realized with high-end rheometers by dynamic mechanical analysis.
Characterization of raw materials, slurries and films
Hierarchically structured supraparticles of silicon/carbon composite nanoparticles synthesized in the gas-phase combine the advantages of both nanoparticles and micrometer-sized particles for production of battery anodes. These active material powders inherit nanoparticle-like mechanical stability to resist pulverization but have a reduced surface area and therefore electrolyte contact area. They show very good redispersion stability when processed into electrodes and have an improved density of the coated layer as compared to silicon/carbon composite nanoparticles.
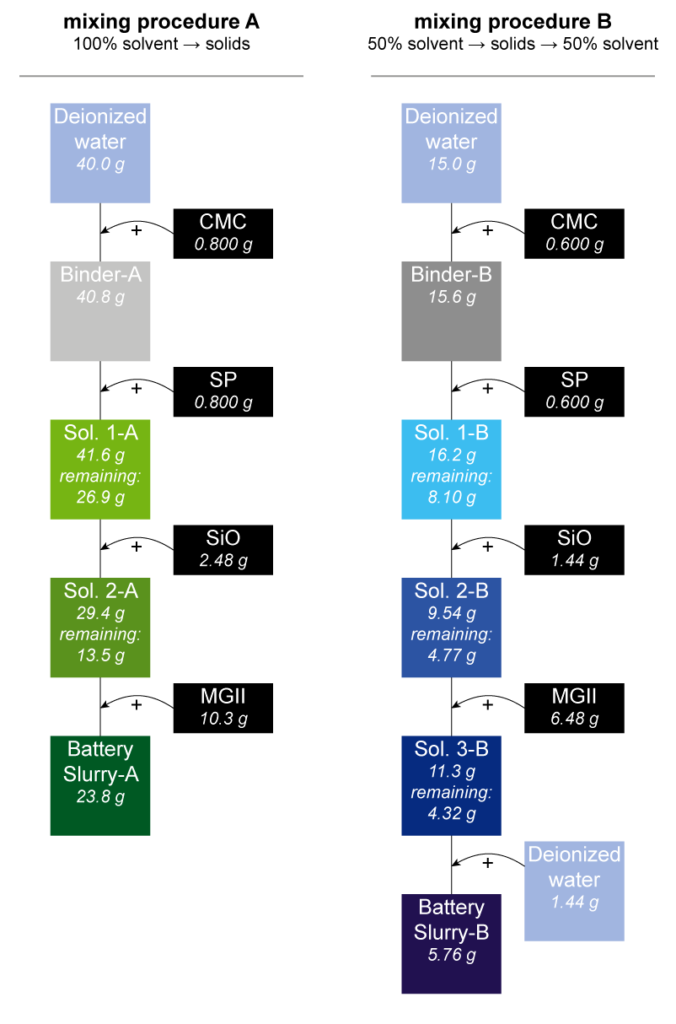
Relevant powder flow properties include the flowability in relation to the consolidation stress, the bulk density and effective angle of internal friction. In general, the flowability of a bulk material cannot be described by a single value due to its dependence on the consolidation stress. Powder rheological measurements show the impact of particle size and carbon content on powder flow behavior, with respect to different synthesis conditions. This underscores the significance of combining particle size analysis and powder rheology to detect slight changes in powder bed behavior.
Rheological properties of slurries during and after mixing are key to ensure smoothness, layer thickness, edge properties, while avoiding pinholes, dripping and spattering (Fig. 2 above right). Optimization of the battery slurry mixing process is accepted as a determining factor for reducing processing time and energy consumption, as well as improving mechanical and electrochemical electrode properties. Viscosity curves are a means to validate the flow behavior of semi-finished battery slurries and to help determine the required dimensions of mixing devices. Also, limits of flowability can be used to adjust maximum solid content while enabling continuous mixing operation.
Variation of multi-step slurry mixing processes demonstrates how rheological characterization aids in monitoring formulation and in improving process design with implications for deagglomeration dynamics. Here, two mixing procedures (Fig. 3 Right), were monitored by measuring viscosity curves with sampling of each addition of a powder component to a solvent. For mixing procedure A, powders were added to the complete quantity of the solvent. For mixing procedure B, 50% of the solvent were only added after all powders were added and mixed in. All semi-finished slurries show shear-thinning behavior with increasing viscosities (Fig. 4 Below left) for increasing solid fractions at a representative shear rate (100 s-1,( Fig. 5 Below right). The same applies for mixing procedure B, however starting at initially higher values. The final dilution step lowers the viscosity, but the final value differs from mixing procedure A. This is the case despite the slurry includes the same components but experienced a modified dispersion history with different solid fractions.

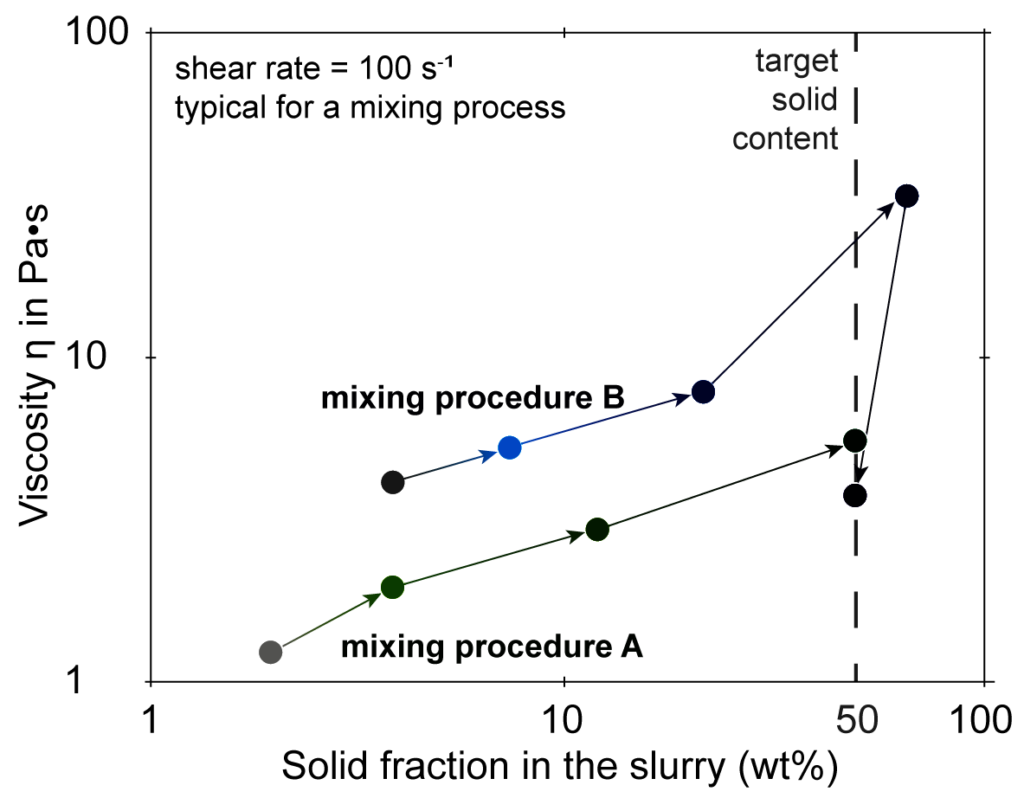
In addition to better understand the mixing process, pump dimensioning benefits from flow stress data derived from tests performed in oscillation, e. g. with amplitude sweeps. Frequency sweeps provide information about particle sedimentation tendency, thus indicate storage behavior. Rheo-impedance measurements offer detailed insights into the internal structure and dispersibility of slurries. Evaluation of impedance spectra under varying shear stresses provides a deeper understanding of slurry behavior with direct links to final battery performance. During slurry coating, three interval structural recovery tests provide indications about the wet layer thickness and smoothness. Coating, drying and calendaring processes, also involve stretching of current collectors. During and after assembly of the battery cell, the same applies for separators and if tensional stresses exceed critical values, films may break. Again, determination of these material limits can be done with a rheometer equipped with an additional linear drive.
High quality raw materials, optimized production processes as well as improved components and cell design are required to design batteries with higher performance, reliability, and safety. Finally, comprehensive characterization of novel battery materials and components with various analytical methods, understanding and optimization of production processes as well as close collaboration of industrial and academic research will be required to merge knowledge between scientific research, industry-scale processing and safety requirements. This will enable development of safe high-performance batteries in large-scale production to cover the enormous amounts of energy storage necessary to make the energy transition a success.