The Road to e-Mobility: Sustainable battery production and job opportunities
To describe the situation for automotive suppliers as challenging is quite an understatement. In an economically strained situation due to the Corona pandemic, supply and raw material bottlenecks, they have to master the balancing act between investments and savings, manage the switch to e-mobility – and at the same time set the course towards sustainable production.
German automotive supplier Webasto shows what opportunities lie in the transformation towards electromobility: six years ago, the company with headquarter in Stockdorf near Munich decided not only to further expand its core business with roofs and heaters, but also to open up additional business areas in the field of electromobility with charging solutions and battery systems. The companys goal is as simple as it is ambitious: Webasto wants to become the leading system provider for electromobility.
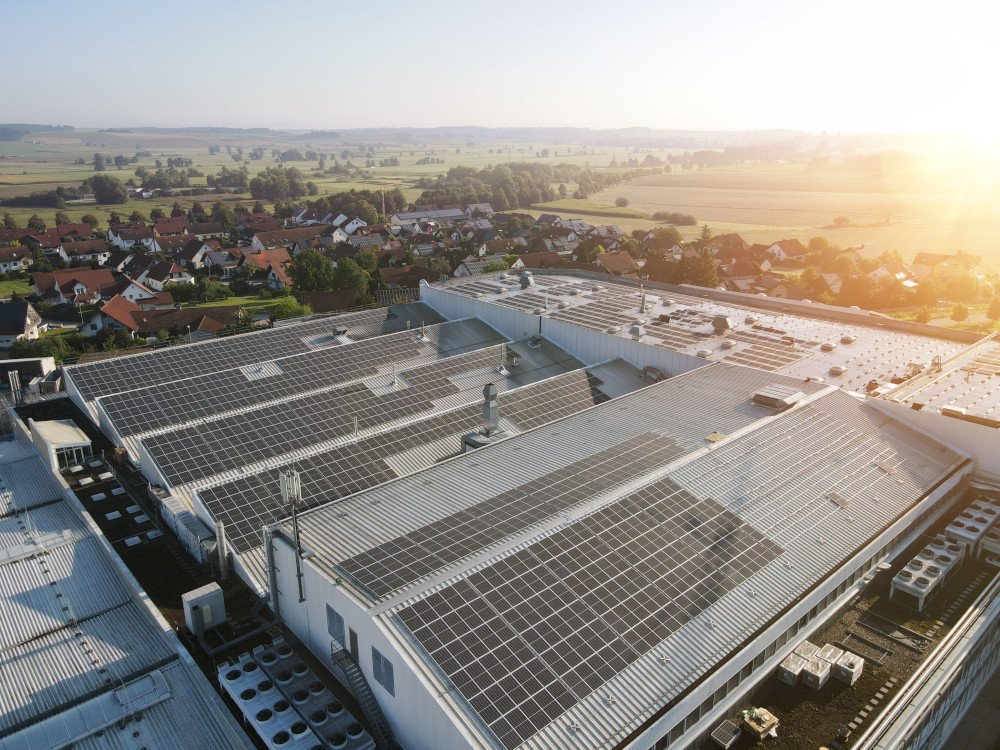
Job opportunities with electric drive
A look at Schierling shows how this could work: Located in the district of Regensburg, Bavaria, for three decades, mainly roof systems were produced in the technology plant of the family owned company. After Webasto set its course in the direction of e-mobility in 2016, the plant became home to one of the most modern production facilities for battery systems. Dozens of employees have been retrained in recent months. The company has invested a lot in this. Of the approximately 450 employees at the plant, around 120 currently work in the battery area. And there are to be even more.
“With our highly flexible multi-product line, we are able to produce up to 40,000 battery systems per year,” explains plant director, Christian Gallner. Webasto invested 11 million euros in setting up the multi-product line. Both battery systems for a European bus manufacturer and, in the meantime, its own modular standard battery system for commercial vehicles and off highway machines are produced here. A benefit of the plant is the extremely versatile production and modularity of the production stations. Plant interlinking with driverless transport vehicles ensures greater flexibility and open floor space. The separation of logistics and production by a kiosk concept enables variable parts logistics. In addition to its advanced technologies, the plant in Schierling is also committed operating sustainably. Since end of 2021 a large portion of the energy needs of Webasto’s plant in Schierling is supplied by the company’s own photovoltaic system. 1,998 solar modules have been installed on the roofs of the production hall.


An output of up to 750 kilowatt peak (kWp) means that the energy needed for battery production can be supplied 100 percent by solar. Covering an area of 4,000 square meters, the photovoltaic system is about half the size of a soccer pitch and generates about 740 megawatt hours (MWh) of electricity per annum. This equates to the annual energy needs of over 180 four-person households. Carbon dioxine emissions are reduced by approximately 447 tons per annum.
“Together with the combined heat and power plants installed in 2014, the photovoltaic system is an essential part of Webasto’s overall strategy for sustainable battery production,” says Christian.
In Schierling not only battery systems and roofs are produced up to six days a week, but also cell modules for electricity storage systems. A cooperation with Solarwatt, a Dresden-based manufacturer of photovoltaic systems enables this next step.
On behalf of Solarwatt, Webasto manufactures cell modules, which are also deployed in BMW Group vehicles, on a specially equipped production line. The components come from BMW and are used according to Solarwatt’s specifications for a cell module, which is then used in the stationary home storage system Solarwatt Battery flex.
New battery plant in Korea
Due to its state-of-the-art equipment, the Schierling plant is a benchmark for other Webasto battery plants, such as the one in Dangjin, Korea, where Webasto will produce its first passenger car battery for Hyundai-Kia Motors Corporation in 2022.
On the highly automated production line, up to 100,000 battery systems per year can be manufactured in a first phase with a cycle time of about 3 minutes. The passenger car battery will be available in two different versions, namely a long-range version and a basic version.
A PV system will also be installed at this plant during the year and will supply electricity for battery production.
”With our battery and charging solutions, we are already making a valuable contribution to electrification. In addition to these investments in e-mobility we are consistently focusing on continuously reducing CO2 emissions at our production sites”, explains Hartung Wilstermann, who holds global responsibility for the Battery Systems division at Webasto.
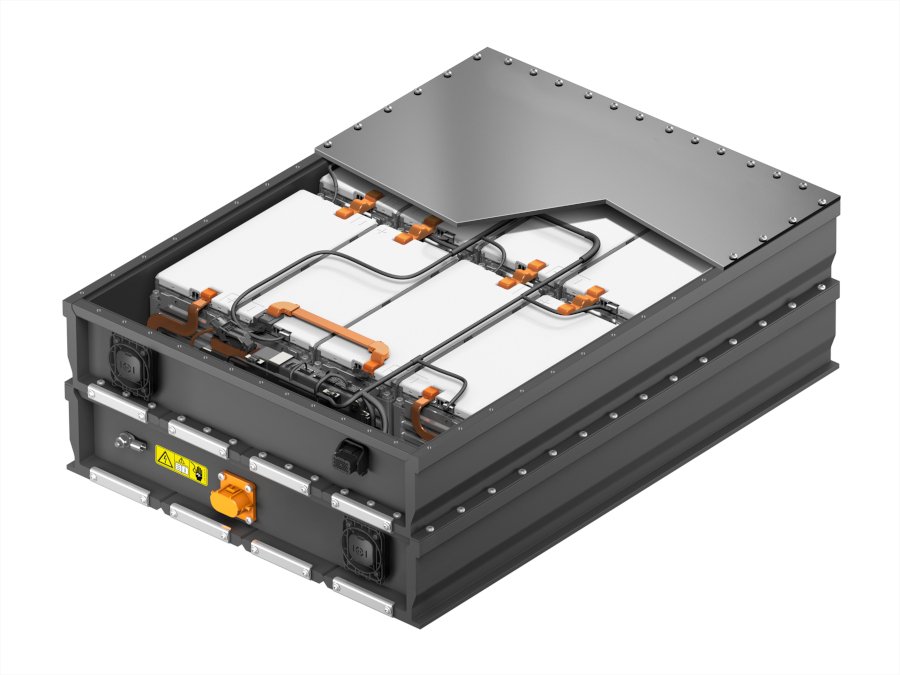
Battery Solutions for the Chinese Market
In mid-2020, the Chinese government announced a new electromobility roadmap, which specifies that half of all new cars will be hybrid vehicles by 2025, and 100 percent of new cars will be electrified by 2035. With its own next-generation battery system for hybrid vehicles, the HEV battery, Webasto is proactively offering solutions to address changing market requirements. The battery system, developed in collaboration with Chinese automakers, can be customised to suit different vehicle models, different environments and body installation requirements, addressing the specific needs of a lightweight and highly integrated battery carrier design.
Webasto has already received an initial order from Great Wall, a leading Chinese manufacturer of hybrid SUVs. The programme will go into production at Webasto’s plant Jiaxing, China.
1 billion euros turnover by 2025
For Webasto, the battery systems business currently still accounts for a relatively small share of sales – in 2020 it was 76 million euros. Wilstermann: “But when I look ahead to the overall market that is waiting for us, there is huge potential for us. We are aiming for a billion euro turnover by 2025.”
To achieve this goal, the company is also focusing on markets beyond the passenger car business. “These are electric buses, trucks, off-highway vehicles at construction sites and airports,” Wilstermann explains. “We have also electrified construction vehicles. There are agricultural vehicles and caravans that will be electric in the future. Mostly we are talking about small numbers, maybe a thousand or ten thousand units. You don’t build your own battery for these, the development would be far too expensive. This is were Webasto comes in: We offer these customers a certified standard battery system developed by us, which can be bought like a consumer product and used immediately.”
Michael Halser,
Spokesman Battery and Charging Solutions