Battery Masses: Process Optimization with Continuous Manufacturing
Dr. Anselm Lorenzoni, Keith Melton
The battery plays a major role in the switch to electromobility. As a result, much focus has been put into improving production processes. The challenge in manufacturing battery masses is that the process must ensure continuous high product quality and needs to be designed with a high level of containment to prevent the escape of toxic materials into the environment. Continuously operating system solutions are designed especially for this area of application. They encompass the entire manufacturing process — from secure containment bulk material handling to dustproof and extremely accurate feeding on to extrusion of the battery masses themselves. The necessary twin screw extruder, together with high-accuracy feeders, affords high reliability, longer uptimes, and numerous characteristics that ensure high, reproducible end-product quality. Moreover, greater material efficiency, as well as more cost-efficient and climate-friendly battery cell production is achieved using continuous production as compared to conventional batch processing.
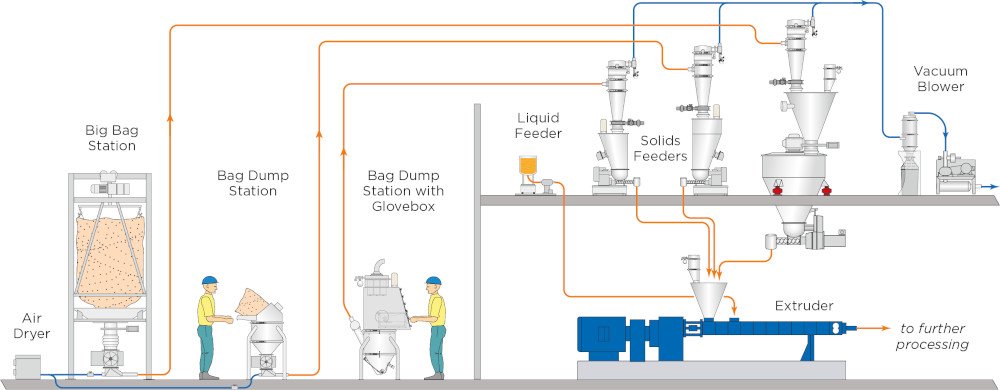
In almost all industries, companies encounter high cost pressures and growing environmental protection requirements, and are increasingly following the trend toward continuous mixing and dispersion processes. A number of arguments speak for continuous production, also in regards to the production of cathode and anode masses. The higher degree of automation drops operating costs and makes it easier to precisely adhere to the formulation for a reproducible, consistently high product quality. Likewise, quick, flexible adaptation to new active materials provides future sustainability, such as simplified scale up to further increases in throughput and efficiency. What is more, thanks to the higher efficiency, greater output per line and year can be achieved.
Continuous Extrusion of Battery Masses to Increase Production Efficiency
When manufacturing battery masses, slurry homogeneity is of vital importance. The ZSK twin screw extruder is ideally suited for this manufacturing as it provides targeted dispersive mixing, thus breaking up solid agglomerates. Together with the subsequent distributive mixing and homogenization this results in a very homogeneous final product. The extruder’s interlocking, intermeshing twin screws generate a constantly high conveying efficiency and thus optimal self-cleaning in the process section, reducing the remaining material in the extruder and thus assuring more material-efficient production. Moreover, the twin screw extruder’s modular construction allows for the implementation of application-specific requirements. The process section is modularly constructed and can be individually, flexibly configured as needed. With regard to climate friendliness, continuous extrusion is persuasive as well: solvent use can be reduced or replaced with non-toxic alternatives. Even energy use decreases thanks to shorter drying times so that production can be more environmentally friendly.
Due to the often abrasive and partially corrosive properties of the raw materials being processed, it is also important that the system’s product-contacting parts are made from material compounds with especially high wear and corrosion resistance, avoiding end product contamination from detached metal particles, over the long term, even when processing heavy-wearing raw materials.

Containment-Secure Feeding of Toxic Raw Materials
Another key aspect of the production process is the feeding of raw materials into the process.
When it comes to feeding powders, there can be some challenges: Solids tend to compress and change form, even to degrade or de-mix while being handled. This means great care has to be taken to not disturb them while keeping a consistent material form. A suitable feeder and the best choice for this task is an accurate twin screw feeder as:
- Powders have a tendency to adhere to surfaces and a twin screw can self-clean.
- Powders tend to flow poorly and twin screws have a greater inlet volume compared to a single screw, and carry the material to the outlet more reliably.
- Twin screws commonly have a double winding (two profiles on each screw element). This reduces the pulsing effect at the screw discharge, improving short term accuracy.
- Twin screws are very versatile because by changing a screw profile many forms of material can be fed successfully.
The challenges in feeding a liquid are very different to those in feeding a bulk solid. Liquids are mainly incompressible, which means their form and specific gravity do not alter during handling, and the challenge is really all about getting the material into the weighed tank and then getting it out again in the right proportion. For this, it is important that there are many pump types available, each optimal for a certain type of liquid. Particular attention needs to be paid to the viscosity of the liquid. In battery applications the binder or solvent solutions generally have quite low viscosities, less than 100cPs, so using a gear-pump or screw-pump provides an excellent solution.
With toxic materials in either liquid or solid form, containment is essential. It is critical that containment designs be practically implemented so that the equipment can be handled and cleaned. While interfaces may have to be sealed to avoid contamination, they also have to be easy to dismantle. The approach to the design is to have a gas-tight system. The feeder hopper and bowl can be considered as a closed vessel, and with the addition of jet-filter ventilation, essential for a loss-in-weight feeder, the unit can be allowed to breathe, while not allowing dust particles to escape into the atmosphere. If required, the whole unit can then be set under a nitrogen blanket so that the material is handled in an inert environment. Upstream and downstream process connections then interface with the plant or the rest of the processing steps. Provided that those connections are closed, also dust-tight, then the entire system can safely contain the toxic material. Coperion K-Tron’s high-accuracy loss-in-weight feeders are exceptionally suited for precise, reliable feeding of even the most difficult flowing ingredients used in the manufacturing of electrode compounds.
Authors:
Dr. Anselm Lorenzoni, Manager Battery Extrusion and Chemical Applications at Coperion
Keith Melton, Manager Battery and Chemical Applications at Coperion K-Tron