Functionality is absolutely paramount
All means of transportation are powered by energy, derived from renewable sources. A simple check-in with a mobile phone allows the uncomplicated use of bus, train or car – the bill comes at the end of the month and is paid depending on the power consumption. This idea is still a utopia. But our metropolises need new traffic concepts and our vehicles need new drives. Climate change, shortage of raw materials and the impending traffic gridlocks are forcing a switch to post-fossil energy sources. The solution is: Electromobility. It can create the freedom of movement that modern societies need. New materials are used because new design concepts and functionalities will be realized and integrated in the car of the future Design, entertainment and communication play an important role as do new energy storage systems such as the fuel cell or the lithium ion battery. This is where the “Bonding Engineers” from Lohmann come into play with their adhesive solutions. In the field of functional tapes in particular, a team of bonding engineers from Lohmann, a leading global manufacturer of high-end adhesive bonds, have been using their inventiveness to introduce innovations that play a considerable role in developments in the electromobility sector.
Functional tapes: Bonding isn’t the only task
Functional tapes do more than just connect two objects with one another. These adhesive tapes feature additional properties like insulation, conductivity, grip, shielding and much more. Functional tapes are in great demand, particularly in the field of electromobility, because here it is not primarily a question of bonding per se, but rather of thermal and electrical conductivity and thus shielding or grounding in the component, as is required for sensors, for example. In addition, electronic devices are becoming smaller and smaller, even in vehicles. In principle, this is advantageous, but the tight space also increases the probability of short circuits or disruption from electromagnetic interference. This is where functional adhesive tapes are the right choice, because they not only ensure precise bonding of different components, but can also be used for earthing, heat dissipation or shielding. Adhesive tapes are also used in the area of sealing: To protect the highly sensitive electronic components, materials are used that adapt perfectly and seal gaps. These not only ensure that dust, dirt and moisture cannot penetrate, but in the field of display technology, for example, they also have a damping effect and protect the sensitive technology from impact. It is actually no wonder that an average of around 4.5 m² of adhesive tape is used in an automobile today.
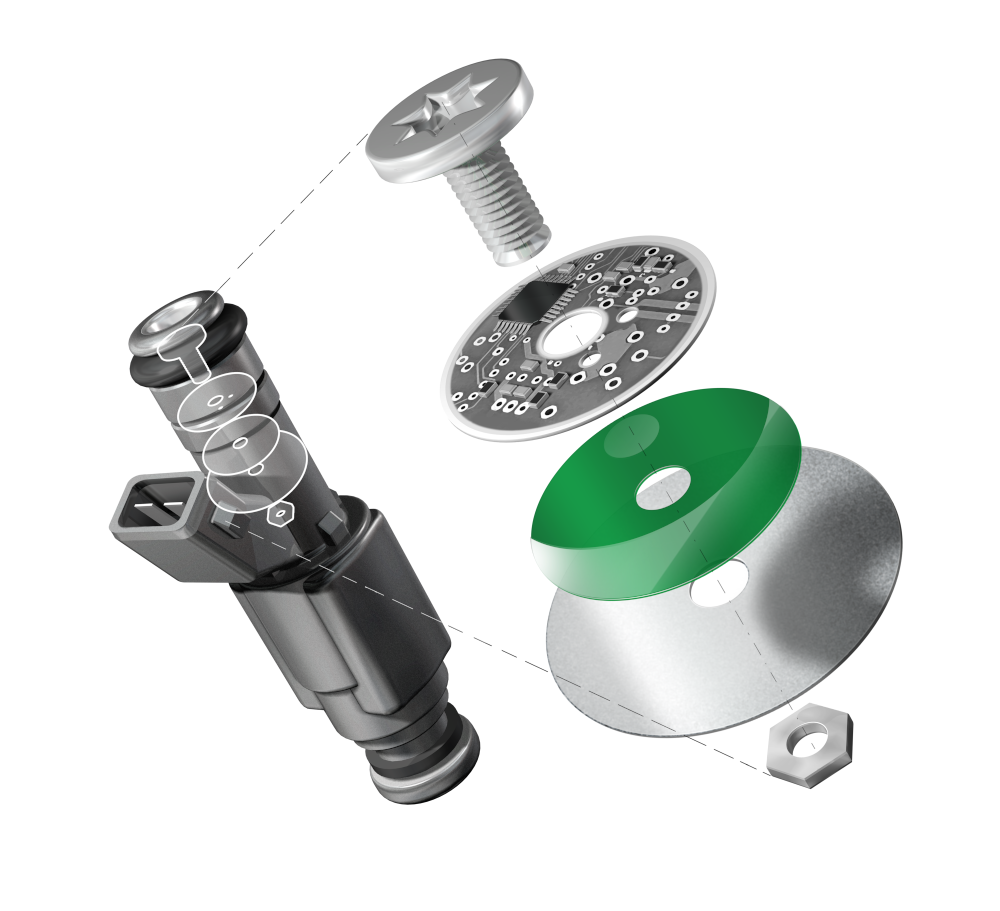
Every enterprise that is researching and developing pioneering technologies to make electromobility a reality, is confronted with the question: What motivates consumers to buy new cars and choose certain options? One point is certainly design. Today’s cares often share either the same or similar exterior design whereas interior design offers various options for individuality. Here, displays with curved screens or functional surfaces and touch applications as well as LED or OLED interior designs are in high demand. These individual design solutions require individual bonding solutions. Our AS (antistatic) range offers e.g. display protection against dust, scratches and electrostatic discharge – until the car reaches its new owner. Design and function of an electrical car thus often are more important than they are for conventional automobiles. Antistatic films (DuploCOLL AS) help to protect the function of lenses, TFT and LCD modules as well as optically bonded touch displays.
When it comes to function and safety topics such as ADAS (advanced driver assistance systems) or highly automated or fully autonomous driving, different issues than those concerning design need to be taken into consideration. A rising number of sensors and devices accompanying the above-mentioned issues need to be safely bonded within the vehicle. Here, EC (electrically conductive) and TC (thermal conductive) tapes come into play. Lohmann’s Bonding Engineers have found diverse TC solutions for the application fields of LED, power transistors, heat sinks or PCB heating parts – only to name a few. EC solutions are required for low current electrical interconnections, grounding (sensor bonding e.g.) or the connection of conductive materials e.g. These two functional materials add to a car’s fulfilment of function and safety issues. The task of the functional tape is, on the one hand, to enable good thermal management of the component, for example, by efficiently connecting the heat sink or heating element, and, on the other hand, of course, the adhesive bond itself as the connection, which must meet different mechanical requirements. In most cases, the functional adhesive tape must also fulfil other tasks, such as tolerance compensation of the components to be joined or it is used as a seal against dust or moisture. To be able to meet these requirements and at the same time – even in unusual times – to be a reliable partner, Lohmann develops and produces at its headquarters in Neuwied.
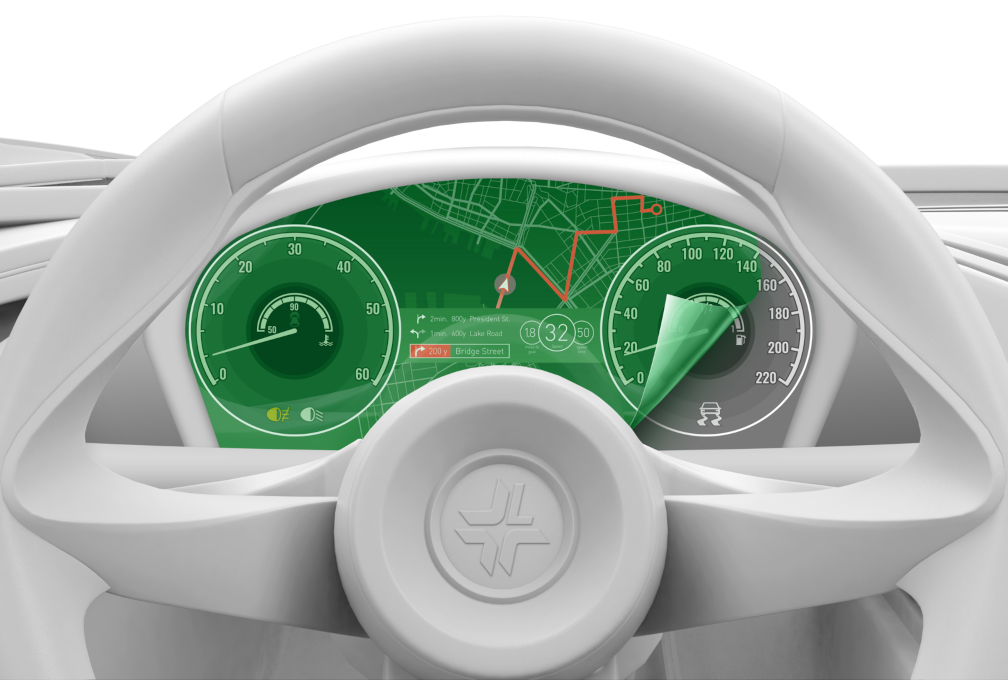
Another thing is the fact that manufacturers in the automotive and electronics sector are increasingly demanding silicone-free bonding solutions for parts and components. For this we have developed the DuploCOLL® HCR range. The disadvantages of silicone products are obvious: The properties of electrical and electronic components can be significantly changed or impaired. Silicones also hinder the painting process. The DuploCOLL® HCR range meets these new demands. The adhesive solutions are silicone-free, highly chemical- and temperature-resistant and resistant to all kinds of environmental influences.
The double-sided PE foam adhesive tape DuploCOLL® G, which is equipped with a customized activator, is particularly suitable for the assembly and permanent fixation of mounting parts on large glass surfaces, as are often used in the construction of electric vehicles. In this case it is all about design. Ever larger glass surfaces and more and more applications are a continuing trend in the production of new vehicles. However, this development also harbors risks: If emblems, lettering and plastic attachments are to be affixed securely on glass, this means that the glass surface must be pre-treated with an activator in an additional step. This is labor intensive and costly. DuploCOLL® G was developed by Bonding Engineers exactly in order to save this additional process step. The double-sided foam adhesive tape possesses an activator that is already implemented in the special adhesive. This eliminates the customary use of an activator in addition to cleaning. It is also temperature, weather and moisture resistant whilst maintaining its consistently good performance. A compressible carrier made of permanently elastic PE foam to compensate for component tolerances, a pure acrylic adhesive on the open side for excellent final adhesion and the aforementioned integrated activator in the special adhesive ensure a quick and efficient adhesive bond. The maximum adhesion is reached after 24 hours, an initial tack after 30 minutes. In addition, an excellent adhesion to the substrates has also been confirmed.
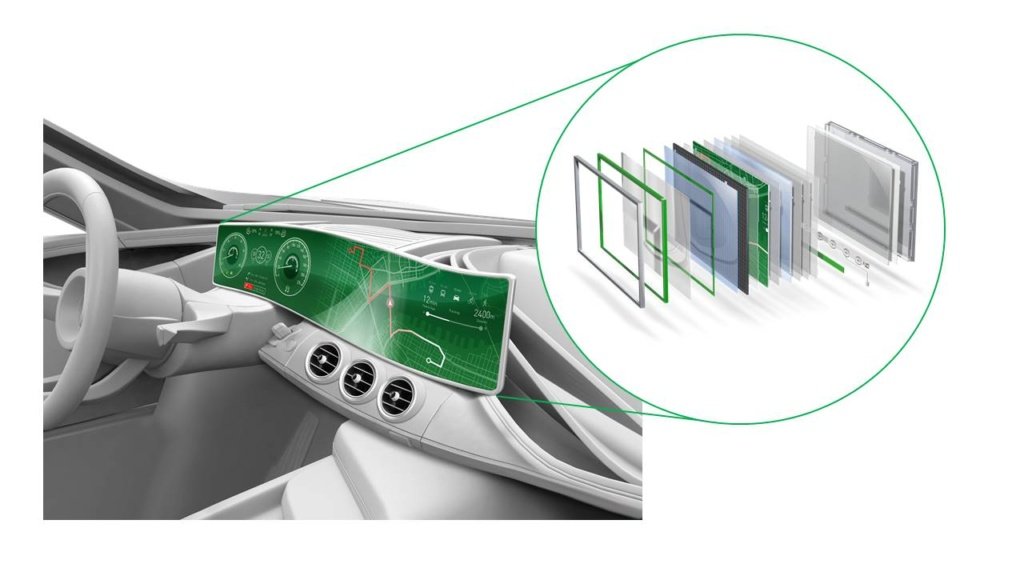
Summary and final considerations
The numerous fields of application of adhesive tapes are exhausting but include infotainment systems such as radio, navigation systems, mobile communication or mirrors, drive trains such as electric motors, air conditioning systems or batteries, sensors such as safety sensors or camera systems as well as charging systems, both in the vehicle itself and the charging stations. In the field of functional adhesive tapes, Lohmann distinguishes between thermally resilient applications, shielding applications and signal connections, electrically insulating applications and antistatic applications in the area of infotainment.
The developments in the field of electromobility and digitization with the integration of stationary and portable modules continually require new bonding solutions. Interference signals from vehicle components among each other, but also from and to external sources, play an equally important role in the development of adhesive solutions, as do temperature fluctuations and susceptibility to interference of high-frequency signals, which are a result of the size reduction and weight savings of individual components and complete assemblies. Here, it is important to offer revolutionary bonding solutions in the areas of temperature management and shielding materials and also to continually develop them in the future. One common denominator exists: All adhesive tapes have a dual function, with the bond itself actually playing a subordinate role. The focus clearly lies on the thermal or electrical conductivity, Lohmann sees a far-reaching potential for electromobility in the future and wants to position itself clearly in this sector.
Our “Bonding Engineers” are proud to be part of this automotive revolution.
Nicole Ehrmann, Lohmann’s market manager for transportation Lohmann GmbH& Co.KG