Jim Chen
- Market demand – Fast charging stations
Energy density technology for batteries is the main determinant affecting the popularization of electric vehicles (EVs). Before 2019, the energy density of batteries was approximately 120 ~150 Wh/Kg; therefore, EVs were unable to be loaded with huge battery capacity (such as Nissan Leaf with .40 kWh, BMW i3 with .42 kWh, etc.). Most of the DC charging stations on the market have also been designed with the energy output of 50 kW to meet the demands for the EVs on the market. In the past, due to the power requirement being 50 kW, the size of the charging station was relatively small. There was not much heat dissipation or noise problem associated with the charging station, and the appearance of the charging station mostly adopted an integrated design (Figure 1). Now, with the advancement of the technology, the energy density of the battery used in today’s EVs has been enhanced to 160 ~200 Wh/Kg due to the material used in the battery. Since 2021, all EVs are to be designed with large-capacity batteries to increase the driving distance, which can now exceed 400 kilometers, as seen in vehicles such as Audi e-tron (rated at 71 kWh) and Benz EQC 400 (rated at 80 kWh). With slow charging speed, the former charging stations of 50 kW can no longer meet the demands of new vehicles for higher charging speed. To this end, a larger charging power source is required, such as 180 kW or even 360 kW. Accordingly, due to the increased energy capacity, the size of the charging station is getting larger as well. An integrated charging station usually occupies significant parking space. More important, the higher the power of the charging stations, the more significant the heat dissipation problem is, and the more fans are required for heat ventilation. This also results in a higher volume of fan noise, which directly affects the environment. As a result, separate charging stations (Figure 2) are often designed for high power applications (such as Tesla charger, Phihong charger, etc.). The advantages of this type of separate charging station lie in two aspects:
- Away from the noise: Generally, the noise of the charging station is mainly attributed to heat dissipation of the power module. A separate charging station is designed with a separate power cabinet away from users, thus keeping the high decibel noise away from the user. Alternatively, power cabinets can be set up underground, making the entire charging area neat and convenient.
- Reduction of the base area of the charging station: In the design of the separate charging station, only dispensers are required to be installed in the parking lot. Since a dispenser only comes with functions of screen display and charging gun, the dispenser is thinner and compact in size without occupying a large base area, allowing better utilization of the parking spaces.
Therefore, separate charging systems designed with high power are to become the mainstream of the charging systems on the market in the future.

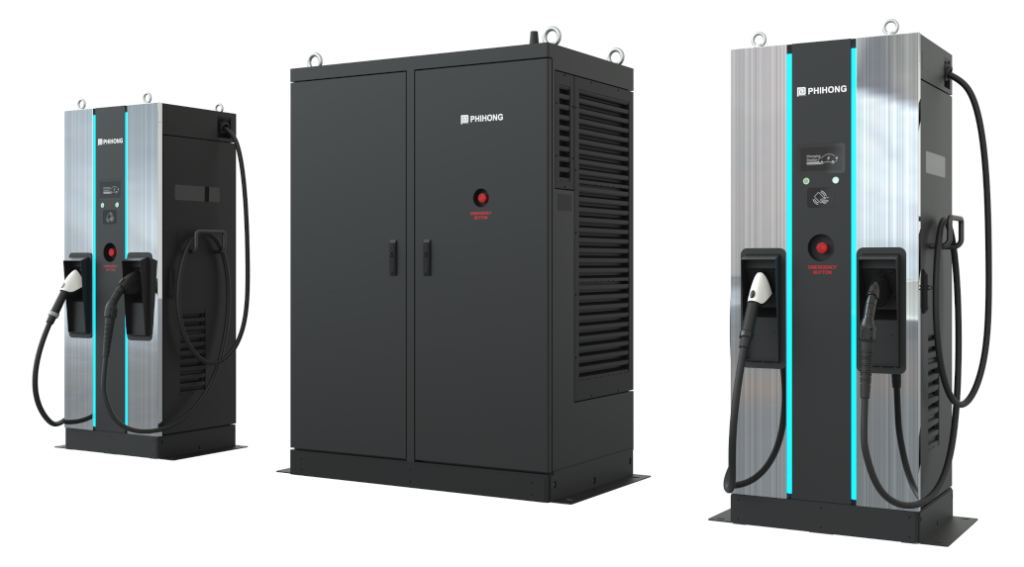
Figure 1: Integrated charging station
- Laws and regulations governing charging stations and main technologies around the world
- Material composition of the charging station
A DC charger is composed of about 300~400 different components, including a breaker, contactor, power module, controller, fan, etc. (Figure 3). These components are arranged according to their functions into a power cabinet for energy conversion (Figure 4), which mainly perform the following functions: A) Energy conversion: Multiple power units are deployed to convert power from AC to DC to charge EVs; B) Protection: When the system detects situations like excessive current leakage or abnormal insulation impedance, power is cut off instantly to protect the user’s personal safety; C) Control: Commands from the EV and cloud platform can be accepted to monitor and control the vehicle charging status. A remote control can also be connected to achieve a balance with the power grid via reduction of the output energy; and D) Communication: The communication methods between charging stations and EVs of different brands differ according to different laws and regulations in different countries, which aims to ensure accident-free charging of EVs.
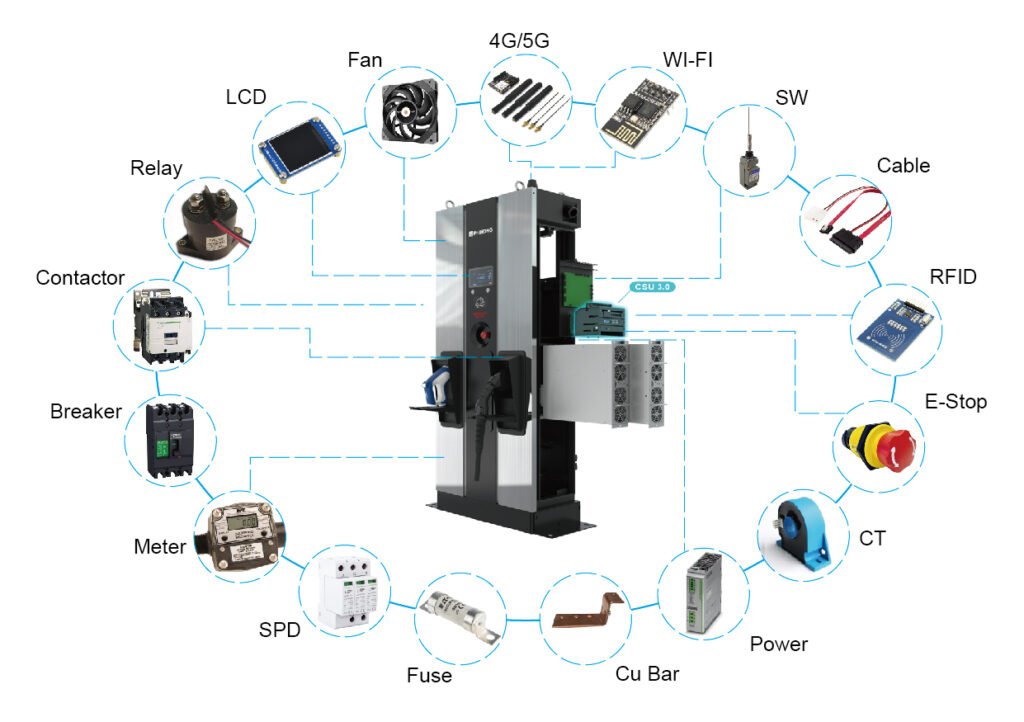

Figure 3: Main components of DC charger Figure 4: Exploded view of the power cabinet
- Laws and regulations governing charging for EVs around the world
- CHAdeMO charging standard, developed by a Japanese industrial consortium. CHAdeMO has already enabled in its version 1.2 (published in March 2017) high-power charging up to 200kW (400A x 500V). CHAdeMO 2.0 now allows for up to 400kW, making high voltage charging up to 1kV possible.
- GB/T 18487.1-2015 Conducting charging systems for electric vehicles – part 1: general requirements; GB/T 27930-2015 communication protocol between off-board conductive charger and battery management system of an electric vehicle.
- Combined charging system (CCS), favored by European and American manufacturers.
- Handshaking between the charging station and the electric vehicle:
The main function of the charging station lies in energy conversion. Special care must be taken in controlling a large amount of energy conversion during the charging process. Therefore, communication between the charging station and the EV is critical, especially the handshaking when the charging gun is inserted for vehicle charging, as the handshaking determines all details of the vehicle charging. Taking CCS as an example for illustration, the handshaking for EV charging involves Stages A, B, C, and D, and multiple sequential actions from t0 to t17. Basically, when the charging station connects with the EV, Stage A, and action t0 start. During this stage, the PLC in the charging station and the PLC in the EV start to exchange all charging parameters, including requirements of maximum voltage and current sent from the EV and the maximum available voltage and current capacity sent from the charger. Meanwhile, actions such as leakage self-check of the charging station and the self-check of the EV take place, until both the charging station and the EV complete their preparation, respectively. Once both sides are ready, a READY signal is mutually sent to each other from the two ends, signifying the readiness for EV charging. During the handshaking, if there is missing data, unmatched parameters, or the handshaking fails to complete within a time limit, the charging sequence is to jump to action t16, and the charging process is ended. In the examples of CHAdeMO and GB/T, a similar handshaking protocol applies. Please refer to Table 1 for comparisons among the charging handshaking for the three examples.
Standard | Communication | Signal on Charger-Connector | GFD |
CCS | PLC | Normal-(Plug-in) CP-PE(9V) Abnormal-(Plug-out) CP-PE(12V) | Detecting during charging 50Ω/V ← (Pass) |
CHAdeMO | CanBus- (CAN-H&CAN-L) | Normal-(Plug-in) Proximity(2V) AbNormal-(Plug-out) Proximity(0V) | Detected before charging 100Ω/V ← (Pass) |
GB/T | CanBus (CAN-H&CAN-L) | Normal-(Plus-in) CC1(6V→4V) AbNormal-(Plug-out) CC1(12V) | Detected before charging 100Ω/V ← (Pass) |
Table 1: Comparison between DC charging handshaking
- Main technology for the charging station
- Power module:
At present, air-cooling power modules of 30 kW make up the mainstream products used for charging stations. Charging modules available on the market mainly include three-phase PFC and DC/ DC converters. Commonly seen PFC circuits are three-phase six-switch PFC circuits and three-phase Vienna PFCs, where the main control methods are triangular wave comparison method, hysteresis current control, and space vector pulse width modulation (SVPWM). Commonly seen DC/ DC converters are ZVS phase shift full bridge converters and LLC resonant converters, where the working principle of a ZVS phase shift full bridge converter adopts two arm switches – one advance switch and the other lag switch – with a phase difference of 180 degrees, and the working principle of a full bridge LLC resonant converter adopts frequency control – one top and the other bottom MOSFETs – with 50% duty, each for the purpose of zero voltage switching based on leakage inductance of the resonant inductor and the transformer. Multiple power sources can be connected in different types of modules in parallel, to jointly generate energy output. For example, 12 power modules can be connected in parallel, to produce a maximum of 360 kW.
Usually, the input to a power module is either one of two types, namely 3-phase 3-wire Delta and 3-phase 4-wire Y, with an input voltage of 380Vac~480Vac, whereas the output voltage from a power module is mostly 150V~950V. Such specifications can meet the requirements of charging for EVs, such as electric cars (requiring a voltage of 300V~450V) and electric buses (requiring a voltage of 600V~850V), while reaching an energy conversion effectiveness of 95% or higher.
In response to the demand for high-power fast charging, the technology of heat generation also needs to be overcome. In conventional charging system, fans are deployed to control air cooling, which results in not only an inferior heat dissipation effect, but also extra noise pollution due to fast-rotating fans. In view of this, water-cooled power modules, with superior heat dissipation effect, have become one of the technologies for the future development of DC fast charging stations.
- CSU controller (CSU):
The CSU controller is the signal control center, which is responsible for communications with the EV, control of the power module and other protection components, and detection of all sensors within the charging station. Most importantly, the CSU controller can transmit data to the cloud through backend communications, for example, Open Charge Point Protocol (OCPP) , allowing the recording of the entire charging process, including any error messages. Please refer to Figure 5 below or pages 60 ~63 of “e-mobility” of the 2020 winter edition.
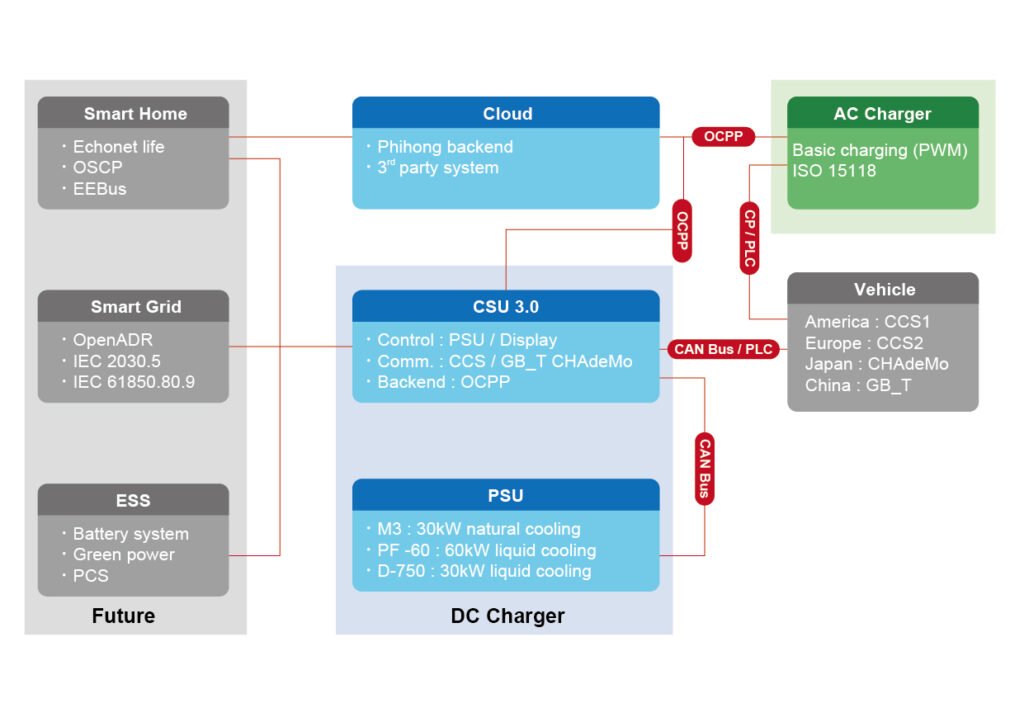
Figure 5: EV charging post and CSU3.0
Due to the large charging capacity of the fast charging stations, safety protection and operating stability are especially important. As the brain of the fast charging stations, the CSU not only requires responsive measures for timely problem detection and correct solution implementation, but also needs to be equipped with hardware redundant mechanisms for safety protection and to safeguard function effectiveness.
- Cloud backend:
The main purpose of the cloud backend is to record all information during the charging process. The charging station transmits heartbeat packages through OCPP to the cloud backend, which ensures the proper working of the charging station. New versions of software can be downloaded from the cloud backend to the charging station for software updates, as well as data on the cloud backend can be transmitted to other cloud platforms through API.
- Applications of charging stations:
In recent years, the break-through development of information, communications, and artificial intelligence, as well as the integration of such breakthroughs and energy saving, carbon reduction, and environmental protection have become popular applications and topics. Although the main function of fast EV charging stations is to supply electric power to EVs, yet the charging stations themselves come with the advantage of substantial electric power, which can also be applied to current popular technologies.
- Integration of charging stations and smart lamp poles:
Energy saving and carbon reduction are a global consensus. The integration of street lamps and information & communications technology allows the street lamps to serve their lighting function in the time of need, while supplementing additional functions to the street lamps besides their lighting function.
The integration of charging stations and smart lamp poles allows EVs to supplement electric power when temporarily parked on the roadside or in the parking lot. This allows EVs to be charged by making use of fragmented time, anywhere, anytime, so that EVs do not have to be charged at specific sites, which makes a break-through energization way for EVs not possible for conventional vehicles fueled by gasoline.
- Integration of charging stations and green energy:
Conventional vehicles are fueled by gasoline, a consumable fuel that cannot be recycled. The production of gasoline also adversely impacts the environment in a big way. The integration of charging stations and renewable green energy based on energy storage and electricity conversion technologies allows for the supply of electric power to EVs from solar energy, biomass energy, etc. Such integration not only saves the consumption of limited resources on the Earth, but also reduces the impact on the environment, while saving on operating costs for business operators.
- Integration of charging stations and smart power grid:
Currently, the distributed smart micro-grid is a development trend in the world which can provide stable electricity supply and better respond to energy capacity requirements, compared to a conventional centralized power grid. The integration of bi-directional charging stations and smart micro-grids can provide EVs with electric power under stable grid electricity, as well as provide electricity, in the opposite direction, from EVs to the power grid under critical circumstances or unstable grid electricity.
- Future trends
Battery technologies continue to evolve, innovate, and break-through barriers. It is expected that batteries with higher energy density and higher discharging current will emerge on the market, and that newer and more advanced batteries are to be available on the market. It is projected that improved battery technology may result in batteries with twice current energy density or more. As people expect an increasingly shorter charging time for the battery, it is foreseeable that the future trends will hold according to the market demand.
- Demands on charging stations with higher energy capacity are expected. For now, charging stations with a maximum capacity of 360 kW still cannot meet the needs in the future. It is estimated that the physical limit of a charging gun stands at around 800 A, whereas charging guns currently available on the market stand at 500 A. If the voltage limit of the charging gun remains at 850 V as now, then the energy transformation in the future can reach 680 kW. Therefore, it is estimated the power of next-generation charging stations can be expected at about 720 kW.
- Insufficient capacity of the power grid will also hinder the development of charging stations for higher energy capacity, because a power grid with insufficient capacity will be forced into overload and fail to support charging stations with higher energy capacity. Another concern is that costs for increasing the capacity of the power grid may not be economical. Therefore, the deployment of local energy storage systems needs to be incorporated into the application of the charging stations, so as to supplement the insufficient capacity of the power grid and save costs.
- Once EVs are designed to accommodate higher battery capacity, relatively speaking, EVs will become a huge mobile energy storage system. Therefore, the energy inside the EV can be sent back to the power grid for energy reuse. The utilization of energy feedback from the EV for family energy storage makes the EV a power supplier for a smart home. Furthermore, EVs can also be a power supplier for a smart grid by utilization of the energy feedback from the EV for the power grid. In this regard, charging stations also play the role of reverse power feed for energy conversion. Therefore, bi-directional charging systems will become necessary equipment in the future.
- Conclusions
In the future, energy conversion, energy storage, and energy management and dispatch will constitute the core of power supply in urban living. Relying on all public charging stations or home-use charging stations deployed in urban construction, AC power from the power plant or from renewable green energy, such as solar power or wind power, can be converted for EV use or home-based energy storage systems for home appliance use. Furthermore, the battery energy stored in the EV can be transmitted back to the power grid. It is foreseeable that charging stations with bi-directional energy conversion ability will create an infrastructure in the future. Accordingly, businesses operating in the dispatch of network power are to emerge, which will benefit from the deployment of power balance and power dispatch, including buying and selling the electricity. In the bigger picture, such development trends help shape smart power grids, smart cities, smart homes, mobile energy storage, power grids for electric cars, etc. Looking ahead, it is hoped that such visions will become a reality in 2025 to 2030.
Jim Chen, Phihong Technology-Electric Vehicle BU RD VP