With a system-level approach, it potentially opens the door to adopting new technologies sooner
Although consumer interest in electric vehicles is steadily increasing, there is a risk their comparatively high cost will remain a barrier to their adoption across the wider mass market, slowing our transition towards an electrified future and dampening our efforts to reach net-zero in our economy.
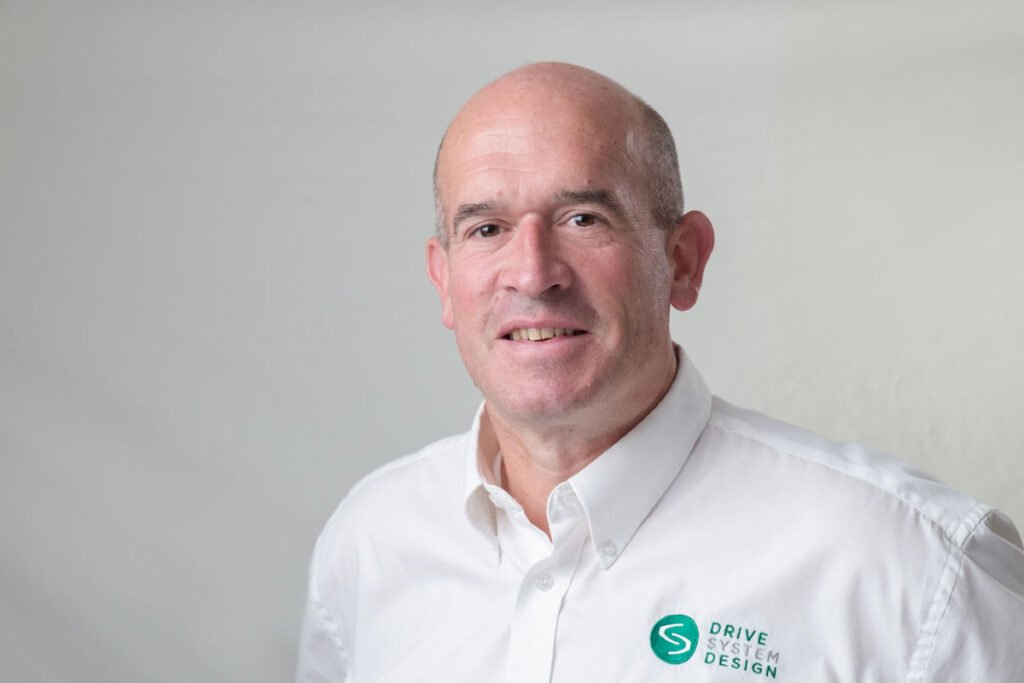
In addition, the expensive nature of some crucial components may hamper attempts by manufacturers to drive down vehicle prices, even in the face of rising volumes. And while new technologies may arrive that can improve efficiency and, ultimately, headline figures such as vehicle range, their relatively high cost may rule out or delay their adoption.
This all comes at a time when OEMs are investing huge sums in redeveloping and redeploying their manufacturing base away from the ICE-based technologies of today, and that creates the temptation to repurpose existing but less-optimal architectures to protect profitability during a time of upheaval. As new technologies become available, simply substituting one component for another may lead to small gains in efficiency or range, but with an increased bill-of-materials cost; by considering the system as a whole, however, optimisations can be made to take advantage of any new technology that may even help drive down the overall cost of the whole powertrain. By taking a system-level approach, it potentially opens the door to adopting these new technologies sooner.
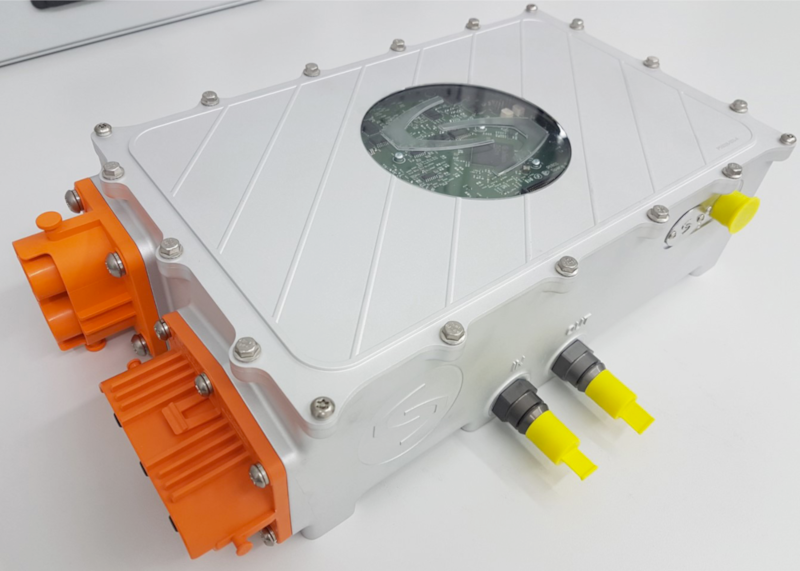
Silicon carbide inverters
Inverters play a crucial role in electric vehicles. In converting the DC electricity from the batteries to the AC required by the traction motor, they generate the variable frequency that is central to controlling the motor. As a result, they form a key part of the operation of the vehicle and have a considerable effect on its overall efficiency.
Most inverters are of the IGBT (insulated gate bipolar transistor) type that are well known within the industry. However, with relatively high switching losses the time spent in the switching transition is extended, and at higher frequencies this introduces limitations that can lead to much reduced current at higher speeds. Typically this makes using IGBT inverters problematic for applications with frequencies of 20kHz and beyond.
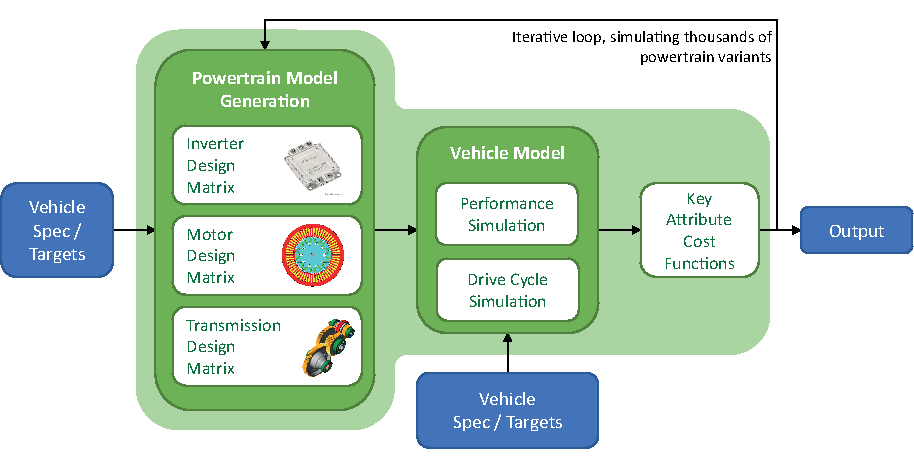
Overview of DSD ePOP simulation model
By contrast, newer silicon carbide (SiC) inverters offer significant advantages, thanks to their inherently reduced switching losses. In fact, system designers are more likely to find themselves limited by the speed of calculations in the microcontroller and the performance of the gate driver circuits.
As a wide bandgap technology, SiC has a lower gate charge which means it needs less energy to switch. Heat dissipation is also increased allowing it to switch faster, leading to the ability to drive more power. And while IGBT inverters have nominal voltage ranges of perhaps 300 – 600V, the stability of SiC permits operation well beyond this point, often as high as 1,200 or 1,500V.
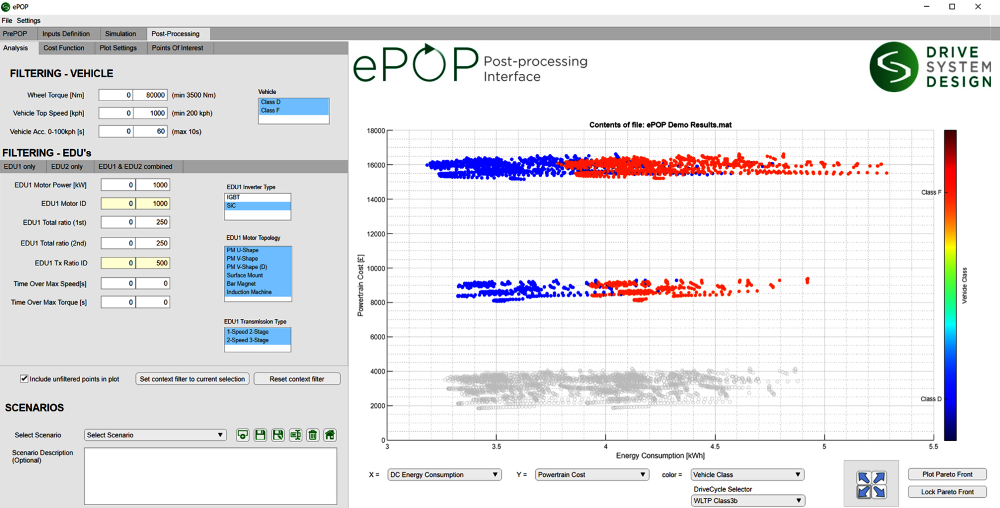
However, these advantages come at an increased financial cost.
Some of these improvements have ancillary benefits that can offset some of the cost increase – the increased power density means the overall size of the inverter can be reduced, while the lower switching losses allow other major components such as coils and inductors to also be reduced in size. Even so, there is still a premium to pay.
“Simply swapping out a conventional IGBT inverter or power module for a silicon carbide equivalent may deliver a modest increase in efficiency by itself. But at the system level, you have failed to make the best possible use of it unless you’ve also adopted, say, a higher frequency drive and a high-speed motor,” says John Morton, Engineering Director at Drive System Design (DSD).
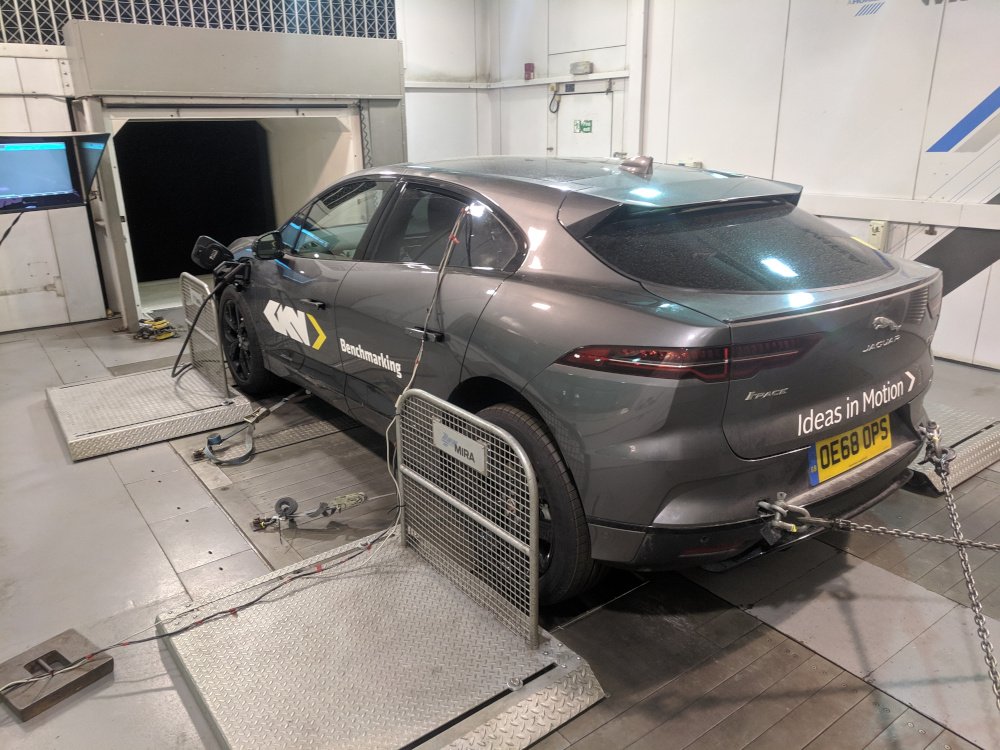
System-level analysis
The challenge comes in discovering where the trade-offs lie between the various components in a system, and the point at which it becomes viable to adopt a new technology once the full impact across an entire platform is considered.
That’s part of the reason why DSD developed their Electrified Propulsion Optimisation Process (ePOP) tool. After generating thousands of powertrain combinations within a pre-defined design space, it accurately calculates losses and efficiency at every point in the drive cycle for each combination, while also determining the mass of every material type within the system in order to contribute to the overall cost analysis.
The analysis may reveal, for example, that adopting an SiC inverter for a particular vehicle platform allows for the use of a smaller, lighter, and cheaper battery while preserving the desired overall vehicle range. Alternatively, given the high cost of new and emerging technologies such as SiC, the process may help to forecast where the tipping point towards financial viability might occur and which applications are likely to benefit the most. This might permit development to start in advance so that, once the economics improve, the products have a head start in the marketplace.
“It might be two or three years before we start seeing SiC devices at prices the mass market can support. At the moment, they’re restricted largely to niche vehicles,” continued Morton. “Of course, if you can show the incremental value of a particular technology, that by itself will contribute to speeding up the process of reaching a volume where the finances make more sense.”
Multi-speed motors
Similar trade-offs reveal themselves when evaluating motor and transmission selection, too. For example, two-speed transmissions may increase overall cost and complexity but often demonstrate greater flexibility when it comes to achieving performance targets, particularly for heavier vehicles.
“We recently worked on just such a project; a vehicle application that required a 250 kW motor to meet the performance targets in a single-speed system, but only a 100 kW motor to satisfy the same requirements in a multi-speed architecture.”
By more effectively utilising the peak efficiency region of the motor, overall energy consumption may be reduced. And by optimising the transmission ratios to suit a particular application, it may be possible to negate the weight and cost impact that would be imposed by specifying a high-capacity battery pack.
“In fact, given the high price of today’s battery technology, we find that putting money into an electric drive system yields roughly twice the bang for your buck over simply investing in a larger battery,” said Morton.
By analysing the trade-offs between the various components that make up an entire powertrain, it becomes possible to ask hundreds, perhaps thousands of ‘what-if’ questions in a way that hasn’t been possible before. That can lead to innovative solutions that help deliver advances in e-mobility at a greater pace than traditional architecture development allows, all while preserving profitability for manufacturers and potentially exposing opportunities to drive down costs for the consumer.
John Morton Engineering Director, Drive System Design.