Why Liquid Cooling?
Electric vehicles (EVs) are now gradually eroding the market share of traditional fuel vehicles, but are they fully accepted by the market and rapidly popularized? In addition to solving the problem of mileage anxiety, the real key is whether the charging time can be shortened to the equivalent of traditional gasoline vehicles.
Due to electric vehicles are hindered by the material problems of the battery and the charging gun capacity, the recharging time for a traditional gasoline-fueled vehicle is about 5 minutes, whereas that for EVs nowadays is 20 minutes or more. To speed up the charging time, the questions we faced are “What capacity does a charging system require?” and how much heat loss will be produced?
Based on different battery capacities of EVs, to travel 500 kilometers, the battery capacity required would be at least 100kW. Ideally, for the battery to be fully charged within 10 minutes, a 600kWh system would be required (certainly, we still face technical constraints such as batteries performance and EV chargers power capacities.) At present, the conversion efficiency of EV chargers is about 95%, which means there is 5% energy loss. A charging system of 600kWh would result in 30kW energy loss all the time. To solve the heat dissipation problem, the traditional method is used the fans to dissipate the heat. With such high amount of heat, a larger fan or an increase in the fan speed would be deployed to solve the heat dissipation issue, which consequently would lead to noise problems and reduced reliability. Therefore, the optimum heat dissipation solution for charging systems of 300kW or above should be liquid cooling technology which will maintain temperature stability, reduce noise, and improve product reliability.
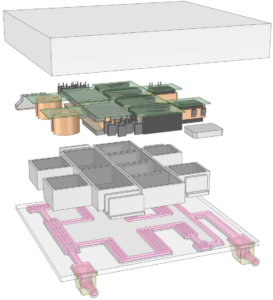
The Proof of The Concept
Phihong Technology’s 30kW liquid cooling power module try to prove that the temperature of the electrical components will not exceed its standard limit. Figure 1 is exposure views of 30KW liquid cooling module. Figure 2 is water flow of cold plate. It is an explanation of the temperature simulation of this liquid cooling module below.
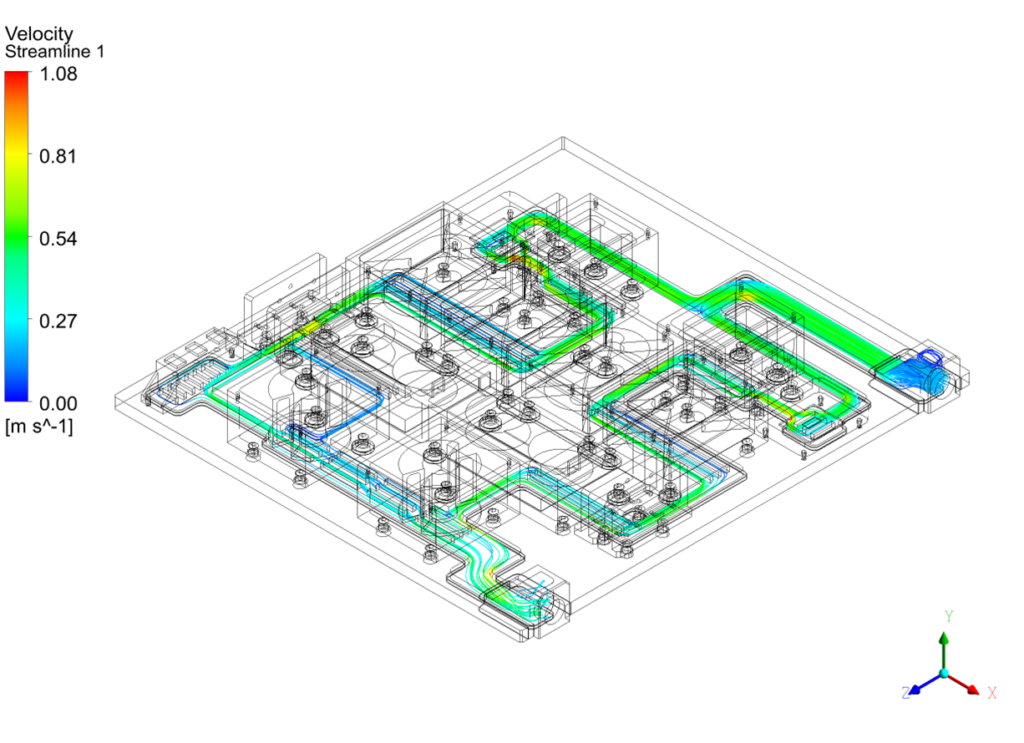
Set up Model of Thermal Simulation
This heat dissipation module is designed with a combination of liquid antifreeze and an aluminum alloy thermal module.
- Inductive components are placed in the aluminum alloy area. We use high thermal conductivity potting as thermal fill.
- Setting at 60 degrees temperature for the inlet, the ambient temperature is also set to 60 degrees. Observe the overall cooling effect of various flow rates through the inlet.
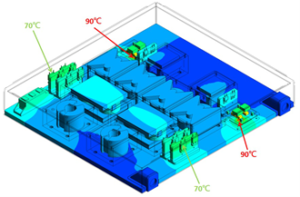
According to the simulation result as shown in Fig.3, to remain the temperature of the SiC MOSFET and Choke below the safety limit, the diameter of the water passage shall be 10mm and the inlet flow rate of cooling liquid needs to be kept higher than 2.0L/min.
Applications of The Liquid Cooling Charging System
The 30kW DC power module can be Integrated with AC/DC liquid cooling PFC modules to build up a DC quick charging system. For example, Phihong Technology takes 12pcs of 30kW modules to assemble into a 360kW liquid-cooled charging system within which a water tank and a pump are used to form a cycle of water flow in the water passage. (Refer to Fig. 4 and Fig. 5.) Pumping cold water into the power modules, the water absorbing heat and then drains out. Meanwhile, the radiator cools the hot water and pump into the water tank for storage after then. In this way, the water circulation can also guide the hot water to a distance away, such as a rooftop or other places where the water can be cooled and avoid noise at the same time.
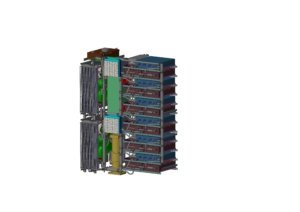
The 30kW DC liquid cooling power module can also be used for Energy Storage System after adding bi-direction functions, which can charge with battery system or discharge energy to the electrical grid. Subsequently, the bi-direction charging system can be charged for EVs or feedback the energy to grid tie.

Liquid Cooling Technology-The Critical Step to High Speed & High Efficiency Technology
Liquid cooling technology is used widely in many applications such as charging system, data center, 5G infrastructure, gaming power or mineral digger. We could expect that liquid cooling technology will help charger increase its power rating significantly, which must be the real key to heat dissipation challenge we have suffered for a long time.
- Increasing the IP level and reliability: we can leave out fan for heat dissipation if we adopt the liquid cooling technology. It enables our cabinet design to meet IP66 requirement and extend product life of charging station at the same time.
- A big leap to improve the noise issue: in the past, the fans are noisy when they are dissipating the heat, especially in the night. With liquid cooling technology, the water circulation can also guide the hot water to a distance away, such as a rooftop or other places where the water can be cooled and avoid noise at the same time.
- Excepting the advantages mentioned above: The 30kW DC liquid cooling power module can also be used for energy storage system after adding bi-direction functions, which can charge with battery system or discharge energy to the electrical grid. Subsequently, the bi-direction charging system can be charged for EVs or feedback the energy to grid tie.
Jim Chen, Phihong Technology-Electric Vehicle BU RD VP